Шэньчжэнь, район Баоань, улица Фуюн, улица Фуцяо, район 3, промышленный парк Лонгхуй 6
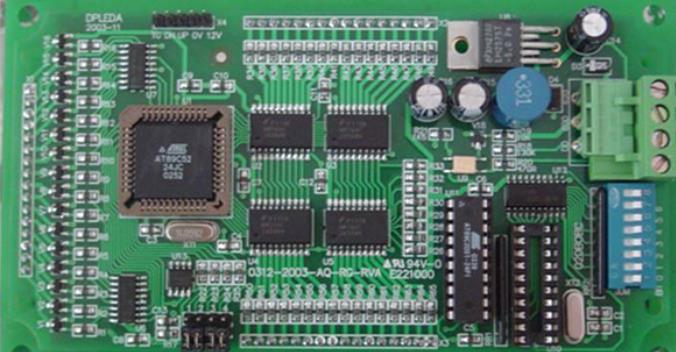
Application of PCBA organic silicon three proofing coating
It is applicable to electronic equipment and equipment working in harsh environments such as high humidity, high salt, dust and vibration. Their PCB boards are vulnerable to salt spray, and moisture and mold will cause system failures Therefore, this PCBA organic silicon 3 paint proof technology PCB is certain Added attention 3 Anti paint refers to that a layer of 3 anti paint with uniform thickness is applied on the printed circuit board to protect it It can effectively isolate the area where PCB is located and the electronic equipment circuit board needs to be protected, as well as its working environment Protect PCB circuit board from damage, so as to improve the reliability of PCB. The circuit board further improves the reliability of electronic equipment
1. 3 Anti coating technology and construction process
Before using 3 anti paint, ensure that the PCB surface circuit board is clean and tidy, and ensure that 3 anti paint adheres well PCBA organic silicon 3 anti painting includes spraying, brushing and dipping The requirements for viscosity resistance of the three paints are different with different coating processes When selecting the spraying process, it is required that the viscosity of anti paint 3 is the lowest to meet the requirements of "spraying" capacity, while the viscosity of anti paint 3 is the highest for impregnation 3 The viscosity of the paint is determined by the solid content of the paint 3 Anti paint manufacturers usually have their own thinners to dilute products with different concentrations to meet the requirements of different painting processes
Although the manual spraying, dipping and brushing methods are simple in operation and convenient in use, and do not require any mechanical equipment investment, the coating quality is difficult to guarantee, and there are problems such as poor uniformity of paint film thickness, high consumption of anti paint, and large environmental impact. During the coating process, it is easy to splash and affect the adjacent sockets, so selective spraying is impossible. It is necessary to manually paste adhesive tape to cover the equipment that needs to be protected before coating, and some gaps between the parts and the side of the parts cannot be sprayed. The existence of these problems has affected the quality of products, which needs to be solved urgently. Selective automatic coater is the perfect solution to the above problems. Precise spraying of PCB can be realized, and the spraying head can avoid non stick paint components, with uniform spraying thickness.
Third, the efficiency of selective automatic coating equipment
In order to ensure the high quality of 3 anti coating, the selective automatic coater shall meet the following technical parameters and efficiency requirements:
1. On line automatic flow operation reduces manual turnover program;
2. With continuous irregular curves such as point/line/surface/arc/circle and 3-axis linkage function;
3. Several different nozzles can be hung at the same time, and the machine equipment can automatically switch according to different spraying requirements to meet the requirements of different spraying areas;
4. CCD visual centering system can be selected to eliminate PCB board or fixture positioning error and improve spraying accuracy;
5. It can accurately control the spraying amount of 3 anti paint.
4、 3 Anti coating process requirements
In order to obtain high-quality 3 anti coating, 3 anti coating process must meet the following process requirements:
1. For connectors, connectors, buttons, light-emitting diodes, gold fingers and other parts that cannot be painted with 3 anti paint, when brushing, dipping or manual spraying is selected, adhesive tape must be affixed. Even if the fully automatic selective coating machine is used, if the coating area is too close to the non painting position (less than 5 mm), it must be isolated and protected.
2. The surface of PCB should be cleaned before painting to remove foreign matters on the surface of PCB. For products with strict requirements, such as automotive, aerospace, navigation and military industries, PCB circuit boards need to be cleaned and dried before being coated. For general products with low requirements, dry high-pressure air can be used to remove dust and other dirt on the surface of PCB.
3. Before selecting the optional automatic coater for mass production, first article inspection must be paid attention to. Ensure that there is no coating loss, coating reduction, coating addition, bubble and other problems, and that the equipment or area (such as connector) that is prohibited from coating cannot have adhesive coating, and the coating thickness is uniform before baking.
4. The humanity of the working environment should be controlled below 65% RH during the PCBA organic silicon 3 anti paint As a composite material, PCB will absorb water If moisture absorption occurs, 3 the paint will not completely protect it Therefore, 3 anti coating process circuit boards shall be assembled as soon as possible after the test If the PCB is placed for a long time and then sprayed with 3 anti paint, it is better to pre bake before spraying Bake at 60 ℃ for 24 hours
It is applicable to electronic equipment and equipment working in harsh environments such as high humidity, high salt, dust and vibration. Their PCB boards are vulnerable to salt spray, and moisture and mold will cause system failures Therefore, this PCBA organic silicon 3 paint proof technology PCB is certain Added attention 3 Anti paint refers to that a layer of 3 anti paint with uniform thickness is applied on the printed circuit board to protect it It can effectively isolate the area where PCB is located and the electronic equipment circuit board needs to be protected, as well as its working environment Protect PCB circuit board from damage, so as to improve the reliability of PCB. The circuit board further improves the reliability of electronic equipment
1. 3 Anti coating technology and construction process
Before using 3 anti paint, ensure that the PCB surface circuit board is clean and tidy, and ensure that 3 anti paint adheres well PCBA organic silicon 3 anti painting includes spraying, brushing and dipping The requirements for viscosity resistance of the three paints are different with different coating processes When selecting the spraying process, it is required that the viscosity of anti paint 3 is the lowest to meet the requirements of "spraying" capacity, while the viscosity of anti paint 3 is the highest for impregnation 3 The viscosity of the paint is determined by the solid content of the paint 3 Anti paint manufacturers usually have their own thinners to dilute products with different concentrations to meet the requirements of different painting processes
Although the manual spraying, dipping and brushing methods are simple in operation and convenient in use, and do not require any mechanical equipment investment, the coating quality is difficult to guarantee, and there are problems such as poor uniformity of paint film thickness, high consumption of anti paint, and large environmental impact. During the coating process, it is easy to splash and affect the adjacent sockets, so selective spraying is impossible. It is necessary to manually paste adhesive tape to cover the equipment that needs to be protected before coating, and some gaps between the parts and the side of the parts cannot be sprayed. The existence of these problems has affected the quality of products, which needs to be solved urgently. Selective automatic coater is the perfect solution to the above problems. Precise spraying of PCB can be realized, and the spraying head can avoid non stick paint components, with uniform spraying thickness.
Third, the efficiency of selective automatic coating equipment
In order to ensure the high quality of 3 anti coating, the selective automatic coater shall meet the following technical parameters and efficiency requirements:
1. On line automatic flow operation reduces manual turnover program;
2. With continuous irregular curves such as point/line/surface/arc/circle and 3-axis linkage function;
3. Several different nozzles can be hung at the same time, and the machine equipment can automatically switch according to different spraying requirements to meet the requirements of different spraying areas;
4. CCD visual centering system can be selected to eliminate PCB board or fixture positioning error and improve spraying accuracy;
5. It can accurately control the spraying amount of 3 anti paint.
4、 3 Anti coating process requirements
In order to obtain high-quality 3 anti coating, 3 anti coating process must meet the following process requirements:
1. For connectors, connectors, buttons, light-emitting diodes, gold fingers and other parts that cannot be painted with 3 anti paint, when brushing, dipping or manual spraying is selected, adhesive tape must be affixed. Even if the fully automatic selective coating machine is used, if the coating area is too close to the non painting position (less than 5 mm), it must be isolated and protected.
2. The surface of PCB should be cleaned before painting to remove foreign matters on the surface of PCB. For products with strict requirements, such as automotive, aerospace, navigation and military industries, PCB circuit boards need to be cleaned and dried before being coated. For general products with low requirements, dry high-pressure air can be used to remove dust and other dirt on the surface of PCB.
3. Before selecting the optional automatic coater for mass production, first article inspection must be paid attention to. Ensure that there is no coating loss, coating reduction, coating addition, bubble and other problems, and that the equipment or area (such as connector) that is prohibited from coating cannot have adhesive coating, and the coating thickness is uniform before baking.
4. The humanity of the working environment should be controlled below 65% RH during the PCBA organic silicon 3 anti paint As a composite material, PCB will absorb water If moisture absorption occurs, 3 the paint will not completely protect it Therefore, 3 anti coating process circuit boards shall be assembled as soon as possible after the test If the PCB is placed for a long time and then sprayed with 3 anti paint, it is better to pre bake before spraying Bake at 60 ℃ for 24 hours
Достаточно загрузить файлы Gerber, BOM и проектные документы, и команда KINGFORD предоставит полное предложение в течение 24 часов.