Шэньчжэнь, район Баоань, улица Фуюн, улица Фуцяо, район 3, промышленный парк Лонгхуй 6
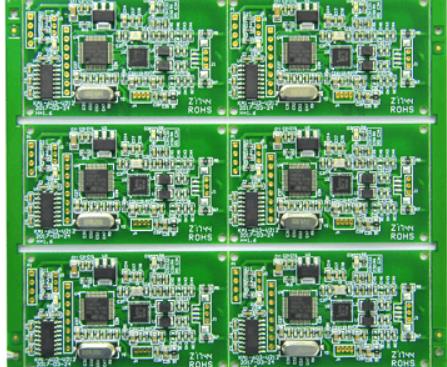
How to Improve SMT Processing Efficiency
Today, let's talk about the efficiency of the placement machine in placement processing? The core of this problem is the delivery date Assuming that the data is available, the delivery date after online production depends on the processing speed and efficiency of the machine's<one href="/tw/" target="_blank">SMT chip The core point is to return to the placement machine and the placement speed of the placement machine The placement speed determines the production capacity of the placement machine and the placement processing plant, and is an important limiting factor for the production capacity of the entire placement processing line
1. Resettlement period.
The placement period is the most basic parameter of the placement speed of the marker. It refers to the time spent in picking up components, placing them on PCB after testing, and returning to the position of picking components. Each time these strokes are performed,
2. Placement rate.
Placement rate refers to the number of components placed within 1h, organized as ch It is the patch speed measured by the patch machine manufacturer under ideal conditions The calculation of theoretical speed does not consider PCB loading and unloading time, and only a small number of components (about 150 chip components) are attached. Then calculate the time used to install components, and calculate the 1h placement amount based on this
However, the following auxiliary time should be considered in actual SMT wafer processing and production.
a. PCB loading overhead time, usually 5-10 seconds.
b. Components on large (rectangular) PCBs are far apart, so the placement time will be extended.
c. Refueling time.
d. Machine maintenance time (days, weeks and months).
e. Unpredictable downtime.
In short, the actual placement speed is much lower than the theoretical placement speed, usually 65% - 70% of the theoretical placement speed. This is a problem that should be considered when selecting the mounter or calculating the production capacity of the mounter.
Methods to Improve the Production Efficiency of Chip Processing
SMT wafer processing efficiency has many aspects. For example, if the overall production capacity remains unchanged and the number of smt wafer production lines is large, the production speed can also be improved. However, operating costs are also increasing. Nowadays, the fierce competition in the electronic industry is unimaginable. For the existing patch production line, we must improve the patch rate and win customer satisfaction. The factors of resettlement rate and improvement measures are briefly introduced as follows:
The SMT production line is mainly composed of screen printing machine, high-speed SMT machine, multi-functional SMT machine, reflow welder and AOI automatic detector. If two placement machines complete a placement process (hereinafter referred to as placement time) when they are equal, the placement rate will be affected. The specific methods are as follows:
1. Balance load distribution. Reasonably allocate the number of two placement components to achieve balanced load distribution, so that the placement time of two placement machines is equal;
2. This smt is placed on the machine itself The placement machine itself has the maximum placement speed value, but it is usually not easy to realize this value This is related to the structure of the mounter itself For example, X's placement machine/Y structure takes the measure of making the placement head pick up components as many as possible at the same time On the other hand, when arranging the placement plan, the components of the same type are arranged together to reduce the number of nozzle changes when the placement head picks up the components and save placement time
Today, let's talk about the efficiency of the placement machine in placement processing? The core of this problem is the delivery date Assuming that the data is available, the delivery date after online production depends on the processing speed and efficiency of the machine's<one href="/tw/" target="_blank">SMT chip The core point is to return to the placement machine and the placement speed of the placement machine The placement speed determines the production capacity of the placement machine and the placement processing plant, and is an important limiting factor for the production capacity of the entire placement processing line
1. Resettlement period.
The placement period is the most basic parameter of the placement speed of the marker. It refers to the time spent in picking up components, placing them on PCB after testing, and returning to the position of picking components. Each time these strokes are performed,
2. Placement rate.
Placement rate refers to the number of components placed within 1h, organized as ch It is the patch speed measured by the patch machine manufacturer under ideal conditions The calculation of theoretical speed does not consider PCB loading and unloading time, and only a small number of components (about 150 chip components) are attached. Then calculate the time used to install components, and calculate the 1h placement amount based on this
However, the following auxiliary time should be considered in actual SMT wafer processing and production.
a. PCB loading overhead time, usually 5-10 seconds.
b. Components on large (rectangular) PCBs are far apart, so the placement time will be extended.
c. Refueling time.
d. Machine maintenance time (days, weeks and months).
e. Unpredictable downtime.
In short, the actual placement speed is much lower than the theoretical placement speed, usually 65% - 70% of the theoretical placement speed. This is a problem that should be considered when selecting the mounter or calculating the production capacity of the mounter.
Methods to Improve the Production Efficiency of Chip Processing
SMT wafer processing efficiency has many aspects. For example, if the overall production capacity remains unchanged and the number of smt wafer production lines is large, the production speed can also be improved. However, operating costs are also increasing. Nowadays, the fierce competition in the electronic industry is unimaginable. For the existing patch production line, we must improve the patch rate and win customer satisfaction. The factors of resettlement rate and improvement measures are briefly introduced as follows:
The SMT production line is mainly composed of screen printing machine, high-speed SMT machine, multi-functional SMT machine, reflow welder and AOI automatic detector. If two placement machines complete a placement process (hereinafter referred to as placement time) when they are equal, the placement rate will be affected. The specific methods are as follows:
1. Balance load distribution. Reasonably allocate the number of two placement components to achieve balanced load distribution, so that the placement time of two placement machines is equal;
2. This smt is placed on the machine itself The placement machine itself has the maximum placement speed value, but it is usually not easy to realize this value This is related to the structure of the mounter itself For example, X's placement machine/Y structure takes the measure of making the placement head pick up components as many as possible at the same time On the other hand, when arranging the placement plan, the components of the same type are arranged together to reduce the number of nozzle changes when the placement head picks up the components and save placement time
Достаточно загрузить файлы Gerber, BOM и проектные документы, и команда KINGFORD предоставит полное предложение в течение 24 часов.