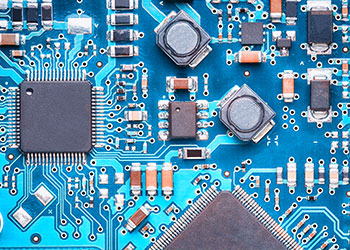
Essence of SMT component placement for flexible PCB
According to the requirements of placement accuracy and the type and quantity of components, the commonly used solutions are as follows:
Solution 1. Multi chip placement: The multi chip FPC is positioned on the tray by the positioning template and fixed on the tray during the SMT placement process
1. Scope of application:
A. Module type: The volume of the chip module is usually greater than 0603, and the QFQ and other components with lead spacing greater than or equal to 0.65 are acceptable.
B. Number of components: There are several to ten components on each FPC.
C. Installation accuracy: Medium installation accuracy is required.
D. FPC characteristics: the area is slightly large, there are no components in the appropriate area, and each FPC has two optical positioning marks and more than two positioning holes.
2. FPC fixing:
Read the internal positioning data of the FPC to manufacture a high precision FPC positioning template according to the CAD data of the metal sliding plate Match the diameter of the locating pin on the template with the hole diameter of the locating hole on the FPC, and the height is about 2.5 mm There are two lower pallet pin FPC positioning templates on the Create a batch of pallets based on the same CAD data The thickness of the wallet is about 2mm, and the warpage of the data after multiple thermal shocks should be small Good FR-4 data and other high-quality data are better Before SMT, place the pallet on the pallet locating pin on the template so that the locating pin is exposed through the hole on the pallet
Circuit board
Place the FPCs on the exposed locating pins one by one, and fix them on the tray with thin high temperature resistant tape to prevent FPC from moving. Then, put the tray from the FPC locating template for sealing printing and mounting, high temperature resistance The adaptive pressure of the tape (PA protective film) should be modeled. It must be easy to peel off after high temperature impact And there is no residual glue on the FPC.
Special attention shall be paid to the storage time between FPC fixed on the tray and welding printing, and the storage time shall be as short as possible.
Solution 2. High precision placement: fix one or more FPCs on the high-precision positioning tray for SMT placement
1. Scope of application:
A. Component type: QFP with pin spacing less than 0.65mm can also be used for almost all traditional components.
B. Number of components: more than dozens of components.
C. Placement accuracy: In contrast, the placement accuracy of QFP is as high as 0.5mm spacing, which can also be guaranteed.
D. FPC features: large area, multiple locating holes, FPC optical locating marks, QFP and other important parts' optical locating marks.
2. FPC fixing:
The FPC is fixed on the part tray. This kind of positioning pallet is customized in batch, with extremely high precision and high precision, and the positioning difference between each pallet can be ignored. After dozens of high temperature impacts, the size change and warpage deformation of the tray are very small. There are two locating pins on this locating tray. One has the same height as the thickness of the FPC, and its diameter matches the aperture of the positioning hole of the FPC. The other T-shaped locating pin is slightly higher than the previous one. On the one hand, because the FPC is very flexible, large in area and irregular in shape, the function of the T-shaped locating pin is to limit the deviation of some parts of the FPC to ensure the accuracy of printing and placement. For this fixing method, the metal plate corresponding to the T-shaped locating pin can be properly treated.
The FPC is fixed on the positioning tray. Although the storage time is not limited, due to environmental conditions, the storage time should not be too long. Otherwise, FPCs are prone to moisture, which will lead to warping and deformation, thus affecting the placement quality.
High precision placement, process requirements and precautions of FPC:
1. Fixing direction of FPC: Before making templates and trays, the fixing direction of FPC should be considered first to reduce the possibility of poor welding during reflow welding. The preferred solution is to place the wafer components in the vertical, SOT and SOP horizontal directions.
2. FPC and plastic encapsulated SMD components are also "humidity sensors". After absorbing water, flexible circuit boards are more likely to cause warping and deformation, and are easy to delaminate at high temperatures. This Flexible circuit board is the same as all plastic patches. It must be dried before it is. High drying methods are commonly used in large production plants. The drying time at 125 ° C is about 12 hours. Place the plastic packaging patch at 80 ℃ - 120 ℃ for 16-24 hours.
3. Storage of solder paste and preparation before use:
The composition of solder paste is more complex. When the temperature is high, some components are very unstable and volatile. In this case, the solder paste should be sealed and stored in a low temperature environment. The temperature should be greater than 0 ℃, 4 ℃ - 8 ℃ is the most appropriate. Before use, when its temperature is consistent with the room temperature, recover it to the room temperature for about 8 hours (under sealed conditions). It can be opened for use after mixing. If used before reaching room temperature, the solder paste will absorb moisture in the air, which will cause spatter and solder bead formation during reflow soldering. At the same time, the absorbed water is easy to react with some activators at high temperatures, consuming the activators, and easy to weld poorly. It is also strictly prohibited to quickly recover the temperature of solder paste under high temperature (higher than 32 ° C). Stir evenly and forcefully by hand. When the solder paste is stirred like a thick solder paste, pick it up with a spatula. If it can be naturally divided into several parts, that means it can be used. It is better to use centrifugal automatic mixer for better effect, which can avoid the phenomenon of residual bubbles in solder paste during manual mixing, and make the printing effect better.
4. Ambient temperature and humidity:
In general, the ambient temperature requires a constant temperature of about 20 ° C and a relative humidity of less than 60%. Solder paste printing requires a relatively closed space with almost no air convection.
5. Wire mesh
The thickness of metal drain plate is usually selected between 0.1mm-0.5mm. According to the actual effect, when the thickness of the drain plate is less than half of the minimum pad width, the effect of the solder paste peeling plate is good, and there is almost no solder residue in the leakage space. The area of the leak hole is usually about 10% smaller than the area of the gasket.
Due to the accuracy requirement of SMT components, the common chemical corrosion does not meet the requirements It is recommended to use chemical etching and local chemical polishing, laser and electroforming to manufacture metal leakage plates From the comparison of price and efficiency, the laser method is preferred