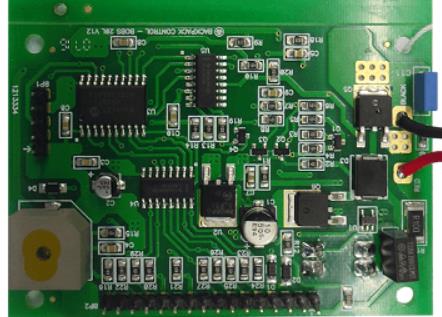
Classification and use of SMT industry terms and fixtures
SMT chip processing industry commonly used terms
With the development of SMT chip processing industry, some general terms in the industry are also widely disseminated. As a beginner, it is very necessary to understand the special terms of the electronic processing industry. Terminology can make our communication easier and our learning efficiency greatly improved.
1. Ideal solder joints:
(1) The solder joint surface shall have good wettability, that is, the melted solder shall be spread on the welding metal surface to form a continuous, uniform and complete solder coating, and the contact angle shall be less than or equal to 90 °;
(2) Use the correct amount of solder, which should be sufficient;
(3) It has a good welding surface. The surface of solder joints shall be continuous, complete and smooth, but the appearance shall not be very bright;
Circuit board
(4) In order to obtain a good solder joint position, the position deviation of the pin or welding end of the component on the bonding pad shall be within the specified range.
2. Non wetting: the contact angle between the welding metal surface and the solder on the solder joint is greater than 90 °.
3. Soldering off: after welding, PCB board is separated from bonding pad surface
4. Suspension bridge: one end of the component leaves the base plate and is inclined or upright.
5. Bridging: the welding point connection between two or more welding points that should not be connected, or the welding point of the welding point is connected with the adjacent conductor.
6. Welding: After welding, electric isolation may sometimes occur between the welding end or pin and the bonding pad
7. Tip: The solder joint has burrs, but does not contact with other solder joints or conductors.
Solder ball: A small solder ball that sticks to the conductor, welding film or printed circuit board during welding.
9. Holes: There are holes of different sizes at the welding point.
10. Position offset: when the welding point deviates from the predetermined position in the longitudinal direction, the rotation direction or transverse direction in the plane
11. Visual inspection method: with the help of a low power magnifying glass, visually inspect the quality of PCBA solder joints.
12. Post welding inspection: post welding quality inspection PCBA welding has been completed
Rework: repair process to eliminate local defects of surface mounted components.
14. Installation inspection: during or after the installation of surface mounted components, the quality inspection shall be conducted to check whether there is any missing, misplacement, wrong installation, damage, etc.
Classification and application of fixtures in SMT chip processing plant
In the production process of smt chip processing plant, some fixed devices are often used. Today, I will briefly introduce the classification and use of fixed devices:
Fixture classification: Fixtures can be divided into 3 categories: process assembly fixture, project test fixture and circuit board test fixture. The process assembly fixture includes assembly fixture, welding fixture, disassembly fixture, distribution fixture, irradiation fixture, adjustment fixture and cutting fixture. The project test fixture includes life test fixture, packaging test fixture, environmental test fixture, optical test fixture, mask test fixture, sound insulation test fixture, etc.; The circuit board test fixture mainly includes ICT test fixture, FCT function fixture, SMT furnace fixture and BGA test fixture.
The use of SMT fixtures: fixtures are produced for commercial needs, including mechanical fixtures, woodworking fixtures, SMT welding fixtures, jewelry fixtures and other fields Some types of jigs are also known as "dies" or "aids" and their primary purpose is to reproduce specific parts with repeatability and accuracy Various types of fixtures can be customized, some of which can improve productivity or make work more accurate