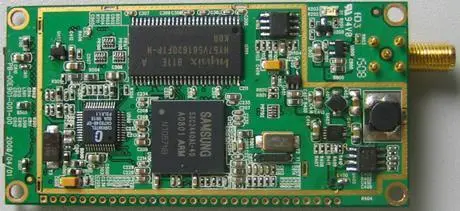
When PCBA solder paste is placed in a heated environment, the backflow of PCBA solder paste is divided into five stages. First, the solvent used to achieve the required viscosity and screen printing performance starts to evaporate, and the temperature rise must be slow (about 3C per second) to limit boiling and splashing and prevent the formation of small solder beads
When PCBA solder paste is placed in a heated environment, the backflow of PCBA solder paste is divided into five stages,
First, the solvent used to achieve the required viscosity and screen printing performance starts to evaporate, and the temperature must rise slowly (about 3 ° C per second) to limit boiling and splashing and prevent the formation of small tin beads. In addition, some elements are sensitive to internal stress, and if the external temperature of the element rises too fast, it will cause fracture.
When the flux is active, the chemical cleaning action starts. The same cleaning action will occur for both water-soluble flux and non cleaning flux, but the temperature is slightly different. Remove metal oxides and some contaminants from the metal and solder particles to be bonded. Good metallurgical solder joints require a "clean" surface.
When the temperature continues to rise, the solder particles first melt separately, and begin to liquefy and absorb tin on the surface. This covers all possible surfaces and starts to form solder joints.
This stage is the most important. When all the individual solder particles are melted, they are combined to form liquid tin. At this time, the surface tension starts to form the surface of the solder pin. If the gap between the component pin and the PCB pad exceeds 4mil, the surface tension is likely to separate the pin and the pad, causing an open tin point.
In the cooling phase, if the cooling is fast, the tin spot strength will be slightly higher, but it cannot cause the temperature stress inside the PCB component too fast.
Summary of reflow requirements:
It is important to have sufficient slow heating to safely evaporate the solvent, prevent the formation of tin beads and limit the internal stress of the element caused by temperature expansion, resulting in reliability problems of fracture marks.
Secondly, the active phase of the flux must have an appropriate time and temperature to allow the cleaning phase to be completed when the solder particles are just beginning to melt.
The melting stage of solder in the time temperature curve is the most important stage. Solder particles must be fully melted to form metallurgical welding, and residual solvent and flux must be evaporated to form the surface of solder legs. If this stage is too hot or too long, it may cause damage to components and PCBs.
The setting of PCBA solder paste reflow temperature curve should preferably be based on the data provided by the PCBA solder paste supplier, and at the same time, grasp the principle of temperature stress change inside the element, that is, the heating temperature rise rate is less than 3 ° C per second, and the cooling temperature drop rate is less than 5 ° C.
If the size and weight of PCB assembly are very similar, the same temperature curve can be used.
It is important to check whether the temperature curve is correct frequently or even every day.