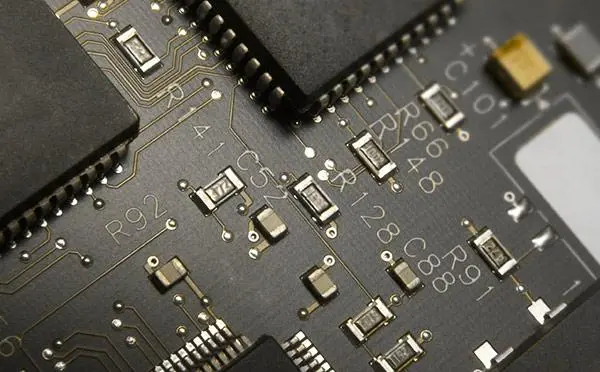
PCBA manufacturers sometimes encounter some special components during chip processing, such as MSD, which is humidity sensitive components, referred to as humidity sensitive components for short, which are a class of electronic components vulnerable to environmental temperature, humidity and static electricity. The influence of humidity sensors on SMT chip processing is no less than that of ESD. It is necessary to strengthen the storage and use management of humidity sensors in SMT processing.
How do PCBA manufacturers properly handle humidity sensors?
PCBA manufacturers can standardize the process control method of MSD, so as to avoid damage to components during reflow soldering due to moisture absorption of humidity sensors, reduce the defective rate of products caused thereby, and improve the reliability of products.
In actual processing, MSDs affected with moisture are generally baked according to the baking conditions in the warning label on the manufacturer's original packaging bag. For PCB component manufacturers without corresponding requirements, high-temperature baking is recommended. Pay attention to prevent ESD damage of devices during MSD carrier replacement. Low temperature baking conditions are not recommended for general MSD baking treatment.
Precautions for Use of PCBA in Processing Moisture Sensitive Devices
1. The oven used for baking shall be ventilated and able to maintain the required temperature under the condition that the humidity is less than 5%.
2. If the manufacturer has no special statement, SMT patch elements transported in the high-temperature carrier can be baked at 125 ℃.
3. SMT patch components transported in low-temperature carriers cannot be baked at temperatures higher than 40 ℃. If higher temperature baking is used, remove the low temperature carrier and replace it with a high temperature resistant carrier.
4. Paper or plastic carrier shall be removed before baking, and rubber belt or plastic tray shall also be removed when baking at 125 ℃.
PCBA manufacturers are specialized in providing overall PCBA electronic manufacturing services, including one-stop services from upstream electronic component procurement to PCB production and processing, SMT patch, DIP plug-in, PCBA testing, and finished product assembly.
The company gives full play to its competitive advantages in scale procurement and quality control, and signs long-term cooperation agreements with a number of electronic component manufacturers at home and abroad and around the world to ensure the quality and stable supply of raw materials and transfer the preferential treatment to customers.
Keeping the procurement advantages of IC, resistor, capacitor, inductor, diode and triode and other components for a long time can greatly save customers' inventory costs, improve the production turnover efficiency and save time. At present, we provide PCBA processing services to customers in the United States, Britain, Japan, Russia, France, Canada, Australia, Romania, Switzerland and other countries and regions.