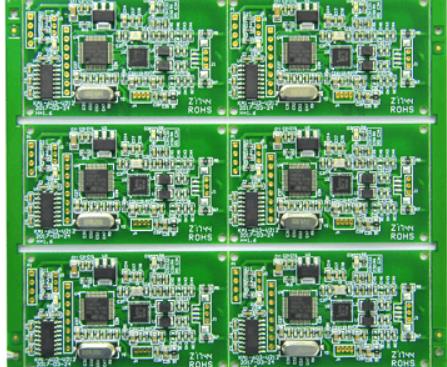
SMT on-site problem solution and process optimization
SMT patch solution to solve on-site problems
The patch has borrowed from other production management methods, and the current Japanese production management methods have been recognized by the world, especially the continuous improvement of the site is considered to be the secret of the success of Japanese enterprises. The "three site principles" of "site, site and reality" reflect the emphasis on the site and the concept of continuous improvement. "Site" is the place where products are produced and services are provided; "Real things" are the main body of the website, which may be machine failures, unqualified products, damaged tools or customer complaints; "Reality" is to analyze real things on the spot and solve problems. This is a very effective production enterprise management concept.
With regard to the principle of "three representatives", it is emphasized that managers should go to the site to analyze and solve the problems of existing objects. When a problem occurs, the place to solve the problem should be the site, not the office or meeting room.
Circuit board
On the spot, management personnel can usually find problems by checking physical objects and take countermeasures in time, observe, touch, feel, and combine their own experience Give play to the "three presence principle" and develop into the "five presence technology": on-site, physical, realistic, cash, and current confirmation The addition of "cash" and "confirmation" on the basis of the "three present principle" means that the results of on-site improvement will be converted into the amount to be confirmed, emphasizing the quantification of improvement results and cost awareness The essence of the "Three Presence Principles" is to attach importance to the scene As a factory manager, we have gained the experience that to solve on-site problems, we must go to the site
On site problem solving method:
1. In case of problems, go to the site first;
2. Check the physical objects;
3. Take temporary measures on site;
4. Analyze the causes and find out the countermeasures;
5. SMT patch adopts standardized processing technology to prevent accidents from happening again.
Process optimization in smt
With the increasing demand for electronic devices, smt patches are facing upgrading challenges in terms of functions and hardware The volume is smaller and smaller, and the PCBA processing and assembly are higher and higher The required volume of all electronic components can no longer be described as small. It immediately becomes a small electronic device In addition, in the wave soldering process, processing technology, raw materials of welding materials, PCB processing circuit board quality, machine equipment and other factors are harmful to the welding quality Therefore, there are many invisible defects in the whole process of wave soldering, and the appearance inspection is generally not easy find. Generally, after delivery to the customer, early failure, vibration and working temperature change of spot welding due to power on and other factors during the whole application process
Many years of smt processing experience put forward some suggestions on wave soldering process:
Many shortcomings of wave soldering clock are related to PCB design, and DFM must be considered.
2. Many defects are related to the quality of PCB and SMT chip processing electronic equipment to prevent counterfeit products from damaging the quality of electronic equipment. Select dealers that meet the standards, and the freight logistics and warehousing standards can be controlled.
3. The lack of specificity of flux leads to many shortcomings. Good flux can withstand high temperature, avoid bridging, and improve the tin permeability of buried holes.
4. The wave soldering temperature should be as low as possible to avoid excessive element temperature and damage to raw materials, especially the secondary melting of tin in the mixing process.
5. Low welding material temperature can reduce the air oxidation of welding wire, reduce tin slag, and reduce the deposition of molten welding materials on the welding material tank and centrifugal impeller. Limiting the transformation of FeSn2 crystals.
6. Outstanding SMT processing technology control can reduce the defect level The main parameters of the processing technology should be comprehensively adjusted, and the temperature curve must be operated
7. Pay attention to the maintenance of solder for smt tin furnace, and strengthen the daily maintenance of mechanical equipment.