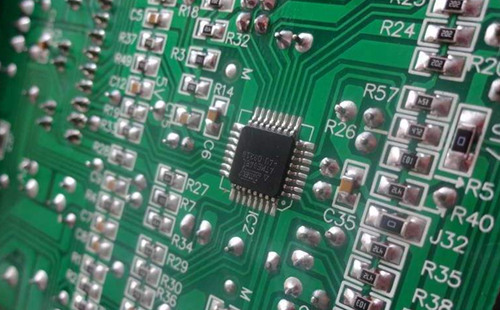
PCBA welding processing first article check items and incoming inspection of circuit boards
PCBA welding refers to the process of connecting bare PCB and components through a series of processes. Generally, prior to online production, the first piece must be confirmed, data checked, and special equipment tested to ensure the welding quality of the first piece. What are the items checked for the first article?
1. BOM check
The BOM is the bill of materials for components, which is provided by the electronic product developer. PCBA welding process is in the process of confirming the first article. The first article is checked with the BOM provided by the R&D supplier to see whether the corresponding materials are mounted in the correct position, whether there are inclined, missing/wrong parts, and whether there is displacement. To ensure the processing quality during formal production.
2. Check of Gerber files
When PCBA welding processing is used for first article confirmation, Gerber documents can also be checked, the silk screen layer can be checked, and the identification on SMD components can be checked for correctness and legibility.
3. Sample check
If it is not a new product, there is usually a sample. During the first article confirmation, the sample shall be checked to ensure the welding quality of the product.
When confirming the first piece of PCBA welding processing, by checking the above items, we can ensure that the PCB board can be correctly mounted with materials according to the requirements of the R&D provider. Finally, we can use special equipment to test the first piece to ensure the welding quality of the first piece.
Incoming inspection items of PCB during PCBA production
PCBA production refers to providing one-stop processing services for circuit board procurement, component procurement, SMT chip processing, DIP plug-in processing, PCBA testing and finished product assembly. In order to ensure the processing quality of products, incoming inspection of purchased circuit boards is required.
The incoming inspection items of PCB during PCBA production include:
1. Circuit board number
First, check whether the board number of the circuit board is consistent with that in the BOM. If the board number is inconsistent with that in the BOM, it will be treated as scrap. Generally, the inconsistent board numbers of the circuit boards are mainly caused by the mixing of the newly modified new products with the original old ones.
2. Color of PCB paint
Check whether the paint color of the circuit board is consistent with that of the product R&D manufacturer.
3. Circuit layer on the surface of circuit board
Check whether the circuit on the surface of the circuit board is scratched or cut. In order to save costs, some circuit board manufacturers will recombine some broken circuits, which will greatly affect the reliability of the product.
4. Plug in hole
During the production process of Circuit board manufacturers, the paint is printed to the plug-in hole, and the copper sheet is too large, which will make it difficult for plug-in components to be inserted into the plug-in hole. During the incoming material inspection, the plug-in components can be used for trial insertion to check whether the plug-in holes meet the requirements.
5. Pad
Check whether the copper sheet on the bonding pad is in good condition. The defective bonding pad will cause difficulty in tinning.
6. Inspection of inner line
In addition to the appearance inspection of the circuit board, the internal circuit of the circuit board shall also be inspected. Generally, flying probe test equipment or ICT test equipment shall be used to detect the open circuit and short circuit of the inner circuit.
In the PCBA production process, strict incoming inspection of the circuit board can ensure the quality of the circuit board, reduce the defective rate in the PCBA production process, and improve the pass through rate of the product.