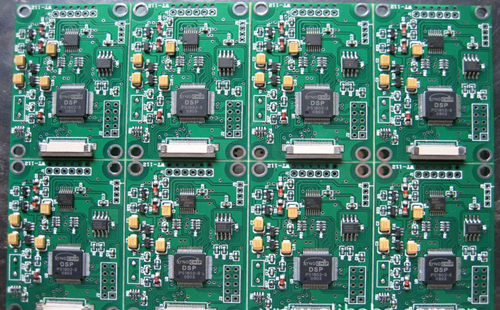
How long will the PCBA be kept? And PCBA aging test.
In consideration of the differences in PCBA production process and storage conditions, the PCB (recommended within 24 hours) should be pre dried before use, and chemical impregnated tin or silver products should be repackaged after unpacking within 12 hours. If the valid shelf life is exceeded, it can be dried after trial use: some properties can be retested, and can still be used after inspection if necessary.
For PCB boards, they are usually stored for more than 3 months before being placed on the machine to avoid the risk of moisture, and need to be baked at 150 ° C for 2 hours. PCBA shelf life
PCBA storage environment:
A. Good storage conditions: temperature is less than 25 ℃, relative humidity is less than 65%, temperature control is available, and indoor environment is free of corrosive gas.
B. General storage conditions: temperature is not higher than 35 ℃, relative humidity is less than 75%, and indoor environment is free of corrosive gas.
The temperature of the warehouse where PCBA is stored should be better controlled at 23 ± 3 ℃ and 55 ± 10% RH. Under such conditions, PCBA boards with surface treatment such as gold deposition, electrowinning, tin spraying and silver plating can be stored for 6 months, and PCBA boards with surface treatment such as silver deposition, tin deposition and OSP can be stored for 3 months.
For PCBA boards that have not been used for a long time, the Circuit board manufacturer should brush a layer of three proof paint on them, which can prevent moisture, dust and oxidation. In this way, the retention period of PCBA will be increased to 9 months.
At present, PCBA electronic processing factory will conduct aging test according to customer demand or PCBA product characteristics when conducting PCBA production. The aging test generally simulates the external humid and high temperature environment to test the PCBA finished products, so that the function board can withstand the changes of air temperature in a thermal aging equipment with temperature changes, and expose the defects of the function board, such as poor welding, mismatched component parameters, temperature drift and faults caused in the commissioning process through the combined effects of high temperature, low temperature, high and low temperature changes and electrical power, so as to eliminate them, It will play a role of stabilizing parameters for the function board without defects. Because this situation has also occurred in electronic processing plants, PCBA boards are normal at the time of shipment, but all kinds of defects appear after a short time of use. In fact, it is necessary to carry out aging test on PCBA boards.
How to perform aging test? The following is our test method for reference only:
Premise: The test shall be conducted under the following environmental conditions: temperature: 15~35 ℃; relative humidity: 45%~75%; atmospheric pressure: 86~106Kpa
The aging method is generally divided into seven steps, which are:
1. Put the function board at the ambient temperature into the thermal aging equipment at the same temperature.
2. The PCBA board is in operation.
3. Then the temperature in the equipment shall be reduced to the specified temperature value at the specified rate.
4. When the temperature in the equipment reaches stability, the PCBA board shall be exposed to low temperature for 2h.
5. The temperature in the equipment shall then rise to the specified temperature at the specified rate.
6. When the temperature in the equipment reaches stability, the PCBA board shall be exposed to high temperature for 2h.
7. The temperature in the equipment shall then be reduced to room temperature at the specified rate.
8. Repeat 3 to 7 consecutively. Until the specified aging time, PCBA board shall be measured and recorded once according to the specified aging time.
The PCBA board shall not be taken out of the box until the temperature inside the equipment reaches room temperature and is stable.