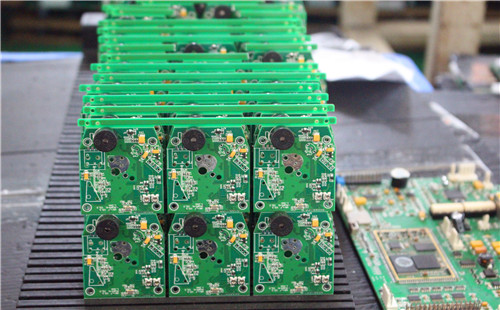
Circuit board manufacturer's explanation: SMT production site management
① Material management.
Establish material placement standards. All materials shall be placed in a fixed area, frame and position according to the requirements and shall be labeled accordingly; The retrieval and playback of materials are guided by corresponding operation specifications and recorded accordingly.
Management of SMT production site
② Environmental management of SMT production workshop.
Formulate civilized production management system for SMT processing site. Require workshop personnel to observe the process discipline and act in strict accordance with the operating procedures; All equipment, articles, raw materials and tools shall be free of dust; Stairs and floors shall be smooth and clean without garbage; Doors and windows are clean and dust-free; The public passage is smooth and free of sundries; "One day inspection" and "daily inspection and daily clearing" shall be achieved, and corresponding inspection and records shall be made every day.
The cleanliness, temperature and humidity of SMT production workshop shall be controlled according to the process documents. Workshop air cleanliness is 100 000 (BGJ73-84). In an air-conditioned environment, there should be a certain amount of fresh air. Try to control the CO2 content below 1000 PPM and the CO content below 10 PPM to ensure human health. Workshop ambient temperature: 23 ± 3 ℃ is the best, generally 17~28 ℃, and the limit temperature is 15~35 ℃ (the printing workshop ambient temperature is 23 ± 3 ℃ is the best). Relative humidity: 45% ~ 70% RH. Curtain the windows on the wall to avoid direct sunlight on the equipment. Different measures shall be taken for standardized control according to the climate characteristics of the plant area, and all operations shall be recorded in detail.
Reasonably arrange lighting in the plant, and the ideal illumination is 800LUX × 1200LUX, at least 300 LUX. When the illumination is low, install local lighting in inspection, repair, measurement and other work areas.
③ Auxiliary environment control of production line.
Control of power supply: power supply voltage and power shall meet equipment requirements; The voltage shall be stable. Generally, single-phase AC 220V (220 ± 10%, 50/60Hz) and three-phase AC 380V (220 ± 10%, 50/60Hz) are required. The power supply of the mounting machine is required to be grounded independently. Generally, the three-phase five wire wiring method should be adopted. The working zero line of the power supply and the protective ground wire should be connected strictly separately. Line filter or AC voltage stabilizer shall be installed in front of the transformer of the equipment.
Control of air source: configure the pressure of air source according to the requirements of equipment. Generally, the pressure shall be greater than 7kg/cm2. The compressed air shall be introduced into the corresponding equipment of the production line through the uniformly equipped air supply network, and the air compressor shall be at a certain distance from the SMT production workshop; The compressed air shall be subject to oil removal, dust removal and water removal.
Control of exhaust air volume: Both reflow welding and wave soldering equipment have exhaust requirements, and exhaust fans are configured according to equipment requirements. The minimum flow value of exhaust duct of full hot blast furnace is generally controlled at 500 cubic feet/minute (14.15m3/min).
PCB manufacturers, PCB designers and PCBA manufacturers will explain SMT production site management to you.