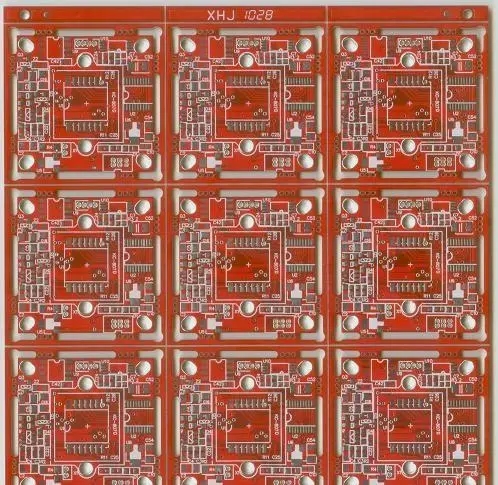
PCB manufacturers explain in detail the process flow of patch processing
There are different processing processes in SMT chip processing. Different SMT chip processing processes can be used according to customer needs, and different processes can also be used according to different conditions of components. The basic process elements of patch processing include: silk screen (dispensing), mounting, reflow welding, cleaning, detection and repair. There are four main methods: single-sided assembly, double-sided assembly, single-sided mixed loading and double-sided mixed loading. 1、 Single side assembly incoming material detection → silk screen solder paste (dispensing) → mounting → reflow soldering → cleaning → detection → repair II. Single side mixed packaging incoming material detection → silk screen solder paste (dispensing) → mounting → reflow soldering → cleaning → DIP
There are different processing processes in SMT chip processing. Different SMT chip processing processes can be used according to customer needs, and different processes can also be used according to different conditions of components.
The basic process elements of patch processing include: silk screen (dispensing), mounting, reflow welding, cleaning, detection and repair. There are four main methods: single-sided assembly, double-sided assembly, single-sided mixed loading and double-sided mixed loading.
1、 Single side assembly
Incoming material detection → silk screen solder paste (dispensing) → mounting → reflow welding → cleaning → detection → repair
2、 One side mixed loading
Incoming material detection → silk screen solder paste (dispensing) → mounting → reflow soldering → cleaning → DIP plug-in → wave soldering → cleaning → detection → repair
3、 Double side assembly
Incoming material detection → B-side silkscreen solder paste → mounting → reflow soldering → overturning → A-side silkscreen solder paste → mounting → reflow soldering → cleaning → testing → repair
This process is applicable to reflow soldering on the A side of PCB and wave soldering on the B side. This process should be used when there are only SOTs or SOIC (28) pins below in the SMDs assembled on the B side of PCB.
4、 Double sided mixed packing
Incoming material detection → A-side silkscreen solder paste → mounting → reflow soldering → cleaning → turnover → B-side silkscreen solder paste → mounting → reflow soldering → turnover → plug-in → wave soldering → cleaning → detection → repair
1. Silk screen printing: It is used to leak solder paste or paster onto the bonding pad of PCB to prepare for the welding of components. The equipment used is a screen printing machine (screen printing machine), which is located at the front end of the SMT production line.
2. Glue dispensing: it drops glue on the fixed position of PCB board, and its main function is to fix components on PCB board. The equipment used is the dispensing machine, which is located at the front end of the SMT production line or behind the detection equipment.
3. Mounting: It is used to accurately install the surface mounted components on the fixed position of PCB. The equipment used is the mounting machine, which is located behind the screen printing machine in the SMT production line.
4. Reflow soldering: Its function is to melt the solder paste, so that the surface mounted components and PCB board are firmly bonded together. The equipment used is a reflow furnace, which is located behind the SMT mounter in the SMT production line.
5. Cleaning: It is used to remove harmful welding residues such as flux on the assembled PCB board. The equipment used is a cleaning machine, which can be either online or offline, and its location can be unfixed.
6. Detection: It is used to detect the welding quality and assembly quality of the assembled PCB. The equipment used includes magnifying glass, microscope, on-line tester (ICT), flying probe tester, automatic optical inspection (AOI), X-RAY detection system, function tester, etc. The position can be configured in the appropriate place of the production line according to the needs of detection.
7. Rework: it is used to rework the PCB board that has been detected to be faulty. The tools used are soldering iron, repair workstation, etc. Configured anywhere in the production line.
SMT processing process has an important impact on product quality. Different processes have different characteristics and advantages. SMT processing manufacturers should choose the most appropriate process according to the specific conditions of processing components.