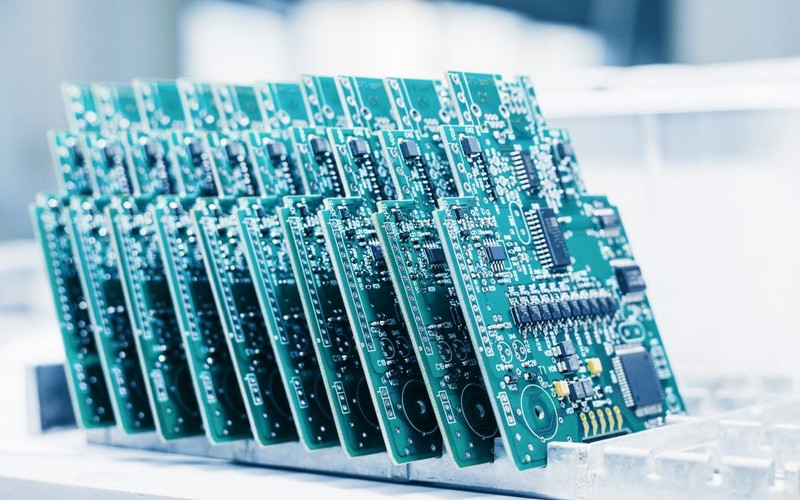
What are the cleaning solvents for PCBA circuit board surface?
Circuit board cleaning agent, also called board washing water, refers to the chemical and electronic industry cleaning agent used for residual flux, rosin, welding slag, ink, etc. on the surface of PCBA circuit board after processing and welding. Usually, ultrasonic cleaning machine, spray, immersion or other equipment and manual cleaning are used. When cleaning PCBA and other electronic products, we need to use plate washing water. This article mainly introduces what is the mainstream plate washing water on the market and how to choose it.
Generally, there are three kinds of washing water on the market: one is chlorinated solvent washing water, two are hydrocarbon solvent washing water, and three are water-based washing water.
Why should I use washing water?
In order to ensure higher reliability, circuit board stability and service life, improve the appearance quality and yield of PCBA, and avoid pollution of pollutants, resulting in electromigration and electrochemical corrosion, resulting in circuit failure. Therefore, it is necessary to clean tin oxide residue, flux residue, oil stain, dust, pad oxide layer, fingerprints, organic pollutants and particles after PCBA welding process.
Do you still need cleaning agent to use the wash free solder paste?
During the processing and production of PCBA circuit boards, solder paste and flux are used for welding. The solder paste also contains flux, and the flux will produce residues. These residues contain organic acids and decomposable electric ions, among which organic acids may cause residues that corrode electric ions of PCBA. During the power on process, the existence of the potential difference between the two pads will cause the movement of electrons, It is possible to form a short circuit and make the product invalid. At present, the space between pads of electronic products is becoming smaller and smaller, so the existence of residues increases the possibility of short circuit, so cleaning in the production process becomes very important. (At present, the use of non ODS (ozone depleting substances) cleaning processes is being promoted all over the world, which can also be called environment-friendly cleaning processes, including: which process to choose for water-based cleaning, semi water-based cleaning, and solvent cleaning, should be determined according to the importance of electronic products, the type of flux used, the requirements for cleaning quality, and the actual situation of the factory. If conditions permit, water-based cleaning and semi water-based cleaning are recommended.) Even the wash free solder paste needs to comply with some current high standards. The word "wash free" means that the residues of the circuit board are safe from the chemical point of view, will not have any impact on the circuit board production line, and can be left on the circuit board. Corrosion detection, SIR, electromigration and other special detection methods are mainly used to determine the content of halogen/halide, so as to determine the safety of cleaning free assemblies after assembly.
However, even if no cleaning flux with low solid content is used, there will still be more or less residues. For products with high reliability requirements, no residues or contaminants are allowed on the circuit board. Especially for aerospace and military applications, even the washfree electronic assemblies must be cleaned.
In the process of PCBA processing, the use of solder paste and flux will produce residual substances, and the flux residue will gradually harden over time and form corrosives such as metal halides, which will adversely affect the reliability and service life of PCB. Therefore, after PCBA processing, it is necessary to thoroughly remove the residual flux, solder and other pollutants on the PCB to keep the PCBA surface clean and tidy, There are many kinds of cleaning solvents for PCBA circuit boards on the market, so how do we choose?
1. Solvent cleaner
Solvent cleaner can be divided into hydrocarbon solvent, halogenated solvent and fluorinated solvent. Solvent based cleaning agent is self-cleaning and low residue cleaning agent. Its disadvantage is that it is easy to evaporate and volatilize, so special attention should be paid to storage. Due to the requirements of environmental protection policies, halogenated solvents and fluorinated solvents have been used less in recent years. When using hydrocarbon cleaning agents, attention should be paid to the fire protection measures of the machine and the environment. At the same time, the leakage prevention treatment of volatile organic compounds should also be considered. Only after these conditions are handled, can hydrocarbon solvent cleaning agents be used in small batches of PCBA proofing. Hydrocarbon cleaning agent has good effect on some rosin type and some non cleaning flux residues, oil stains and dirt.
2. Water based cleaning agent
The water-based cleaning agent can be used in most scenes, but when selecting the water-based cleaning agent, it is necessary to consider the limitations of the circuit board surface, metallization and compatibility, including the compatibility of lead oxide reactants, white metals, yellow metals, ink marks and coating materials, followed by the size, spacing and complexity of the assembly. Different types of flux residues have different compositions, and the cleaning materials of water-based cleaning agents have different abilities to remove welding residues. At the same time, the water-based cleaning agent cleaning process is also the atmosphere ultrasonic cleaning process and spray cleaning process. In the spray cleaning attack, the tolerance of foam is lower. It is required that there is no foam or foam is very small and can dissipate quickly.
When we know the residues on the PCBA circuit board, we can choose whether to use solvent cleaner or water-based cleaner according to the actual needs. When we meet the cleaning conditions, we also need to consider environmental protection issues.