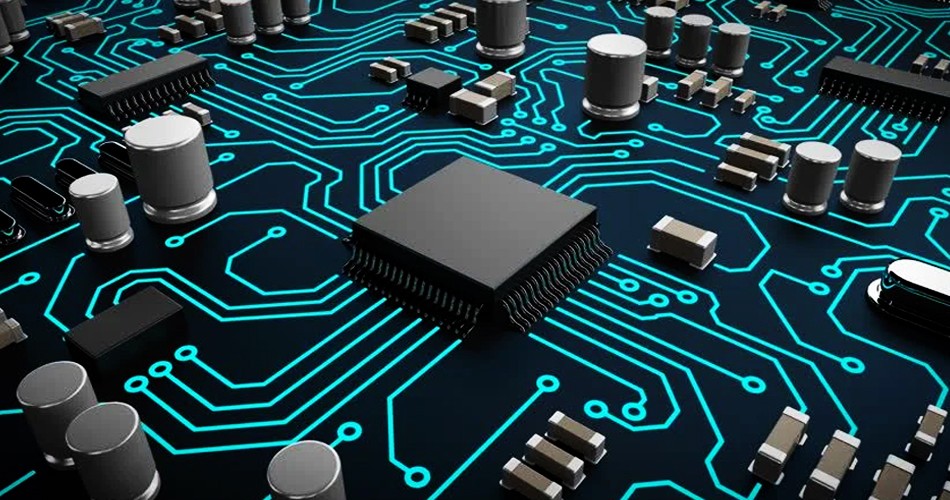
The circuit board factory explains the bill of materials
PCBA processing and manufacturers let you know what BOM is in one minute!
The full English name of BOM is Bill of Material, the Chinese name is "Bill of Materials", and the English abbreviation is "BOM". We are used to calling the English abbreviation BOM.
BOM is the product structure data file that can be recognized by the computer, and it is also the leading document of ERP. BOM enables the system to identify the product structure, and it is also the link to contact and communicate various businesses of the enterprise. The types of BOMs in the ERP system mainly include five categories: indented BOMs, summarized BOMs, reverse query BOMs, cost BOMs, and plan BOMs.
When adopting computer aided production management, first of all, the computer should be able to read out the product composition and all materials involved. In order to facilitate computer identification, the product structure expressed in diagrams must be converted into a data format. This document that describes the product structure in a data format is the bill of materials, or BOM. It is a technical document that defines product structure. Therefore, it is also called product structure table or product structure tree. In some industrial fields, it may be called "formula", "element table" or other names. In MRP II and ERP systems, the term "material" has a broad meaning. It is a general term for all products, semi-finished products, work in progress, raw materials, accessories, collaborative parts, consumables and other production related materials. In MRP II and ERP systems, pcb BOM refers to the relationship tree composed of parent and child components. BOM can provide information in the form of top-down decomposition or bottom-up tracking. In MRP II and ERP systems, BOM is an organizational relationship between data. The hierarchical relationship between these data can be used as the basis for the design of many functional modules. Some forms of these data are summary reports that we are familiar with.
What is the function of BOM?
BOM is the most important basic data in the PDM/MRP Ⅱ/ERP information system. The design of its organization format directly affects the processing performance of the system. Therefore, it is very important to flexibly design a reasonable and effective BOM according to the actual use environment.
The BOM is not only an important input data in the MRP II system, but also an important basis for the financial department to calculate costs and the manufacturing department to organize production. Therefore, the BOM has the largest impact and requires the highest accuracy. It is very important to use and maintain BOM correctly during the operation of management system.
In addition, BOM is also an important interface between CIMS/MIS/MRP Ⅱ/ERP and CAD, CAPP and other subsystems, which is the key point of system integration. Therefore, when implementing BOM management by computer, information exchange between BOM and other subsystems should be fully considered.
BOM information is used in MRP II/ERP system for MRP calculation, cost calculation and inventory management. BOM has various forms, which depend on its use. The specific uses of BOM are:
1. It is the basic basis for computer identification of materials.
2. It is the basis for preparing plans.
3. It is the basis for matching and picking.
4. Follow up the machining process according to it.
5. It is the basis for purchasing and outsourcing.
6. Calculate the cost according to it.
7. It can be used as quotation reference.
8. Carry out material traceability.
9. Make the design serialized, standardized and generalized.
What are the forms of BOM?
Classified by use
The product goes through three stages: engineering design, process manufacturing design, and production manufacturing. In these three stages, the bill of materials EBOM, PBOM, and CBOM with very similar names but very different contents are respectively generated. These are three main BOM concepts.
Engineering BOM - E-BOM:
The data structure used in product engineering design management usually accurately describes the design indexes of products and the design relationship between parts. The corresponding documents mainly include product list, drawing directory, material quota list, various product classification list, etc. E-BOM is usually limited to the materials appearing in the drawing parts list, indicating the hierarchy and subordination of drawings, and managing technical documents. Although it also has the function of guiding procurement and estimating quotation, it is mainly used to manage drawings.
Plan BOM - P-BOM:
The process engineer redesigned EBOM according to the processing level and capacity of the factory. It is used for process design and manufacturing management. It can be used to clearly understand the manufacturing relationship between parts, track how parts are manufactured, where they are manufactured, by whom, with what and other information. At the same time, PBOM is also one of the key management data structures of MRP II/ERP production management.
In fact, BOM is a broad concept. According to different purposes, there are many kinds of BOM; BOM on design drawings, planned BOM, manufacturing BOM for final product assembly, cost BOM for cost calculation, maintenance and repair BOM, etc. According to different application priorities in different stages, we often see different BOM formulations, including:
Design BOM - D-BOM (Design BOM):
The DBOM of the design department is the overall information of the product, and the corresponding common text formats include product list, drawing catalog, material quota list, etc.
The design BOM information source is generally the title block and parts list information in the complete set of design drawings provided by the design department. Sometimes it involves some information on the process card prepared by the process department.
Design BOMs are generally summarized at the end of design. If there are a lot of borrowing relationships, design BOMs can be summarized at the beginning of the design phase, and then design tasks can be arranged according to the newly generated components.
The corresponding electronic view is often in the form of a product structure tree. Each node in the tree is associated with various attributes or graphic information. It is mainly used as the basic data of product management and drawing management in PDM software.
Virtual BOM (virtual part):
The virtual part represents an item that does not exist and does not appear on the drawing or in the processing process. It is a "fictitious" item. It is only used to achieve certain management purposes, such as combined purchase, combined storage, and combined issue. In this way, when processing business, only virtual parts need to be queried by the computer, and actual business documents can be automatically generated. You can even query its inventory quantity and amount, but inventory accounting is only for actual materials. Virtual parts can simplify the management of product structure. In order to simplify the management of the bill of materials, an article is invented in the product structure.
Bill of Material (BOM for short) is a detailed record of all the lower level materials and related attributes used in a project, that is, the dependency, unit consumption and other attributes of the parent part and all child parts. In some systems, it is called material list or formula list. In order to correctly calculate the required quantity and time of materials in the ERP system, an accurate and complete product structure table must be available to reflect the quantity and subordinate relationship between the production products and their components. Among all the data, the bill of materials has the largest influence and requires high accuracy.
The bill of materials is an indispensable and important document for receiving customer orders, selecting assembly, calculating the cumulative lead time, preparing production and purchase plans, supporting picking, tracking logistics, tracking tasks, calculating costs, and changing cost design. The above work involves the sales, planning, production, supply, cost, design, and process departments of the enterprise. Therefore, it is also said that the BOM is not only a technical document, but also a management document. It is the link to contact and communicate with all departments. All departments of the enterprise need to use the BOM.
The bill of materials fully reflects the data sharing and integration, and is the framework of the ERP system. It must be highly accurate, appropriate and structured. ". Therefore, to make ERP work well, enterprises must have a sound and mature mechanism to maintain BOM creation and change. On the other hand, good management of BOM change is more important than BOM filing management, because it is a dynamic management.
The basic feature of ERP is to arrange the material supply and production plan according to the demand and forecast, and put forward what is needed, the required time and quantity. The management object of the ERP method is mainly the materials required by the manufacturing industry. Therefore, the basic content of the product database should be the item master file and the product structure list. The gross demand for materials at all levels can be calculated according to the master production plan and BOM, and the dynamic net demand for materials can be calculated by considering the existing inventory and the in process quantity. This generates the material demand plan ERP according to the production schedule requirements. ERP is just a kind of instruction plan. In order to ensure the realization of ERP, the implementation and control of the plan need to be considered, so it has developed into manufacturing resource planning ERP, in which the important content is workshop operation planning and control.
Therefore, BOM is the basis for the operation of ERP system. The breadth and depth of ERP implementation depends on the coverage and data content of BOM. The establishment of BOM, especially the timely entry of new product BOM, has become the bottleneck that restricts the successful operation of ERP.
Differences between BOM and parts list
The bill of materials is different from the familiar product parts list, mainly in the following aspects:
1. Each material in the bill of materials has its unique code, that is, the material number, which is very clear about the material. There is no such strict regulation in the detail list of general parts. Parts lists attached to individual products do not necessarily take into account the uniqueness of the entire enterprise's material code.
2. The hierarchical relationship between parts and departments in the bill of materials must reflect the actual assembly process. Some assembly parts on drawings may not appear in the actual assembly process, but may also appear in the bill of materials;
3. The bill of materials should include the raw materials, blanks and some consumables required by the product, and the yield should also be considered. The parts list does not include materials that do not appear on the drawings, nor does it reflect the consumption quota of materials. The bill of materials is mainly used for planning and control. Therefore, in principle, all planning objects can be included in the bill of materials;
4. According to the needs of management, several different shapes of a part, such as casting and forging blanks and processed parts, and processed parts and repainted parts with different colors, should be given different codes in the bill of materials to distinguish and manage. Parts lists are generally not treated like this.
5. It is very flexible and can be completely defined by the user. For example, processing a stamping part requires a special die in addition to the raw steel plate. When creating the bill of materials, you can hang the die as a purchased part at the lower level of the stamping part. The quantity relationship between the die and the stamping part is the die consumption quota.
6. The sequence of a parent part and its sub components in the bill of materials should reflect the assembly sequence of each sub component, while the sequence of part numbers in the parts list is mainly for the convenience of drawing.
ERP system itself is a planning system, and BOM is the framework of this planning system. The quality of BOM production directly determines the quality of ERP system operation. Therefore, BOM preparation is the top priority of the whole data preparation work, and the requirements are almost strict. There are two specific requirements:
1. Coverage: BOM needs to be made for all products under production, so the coverage should be above 99%. Because there is no product BOM, it is impossible to calculate the purchase demand plan and manufacturing plan, and it is also impossible to perform nesting control;
2. Timeliness rate; Both BOM production and engineering changes need to be made in time. The BOM must be completed before MRP, and engineering changes need to be made before issuing nested materials. This has two meanings: 1) timely production; 2) Update timely. The two should be closely linked to avoid "two skins".
3. Accuracy: The accuracy of the BOM should be above 98%.
The above is the BOM explained to you by the manufacturer of KingFord pcb.