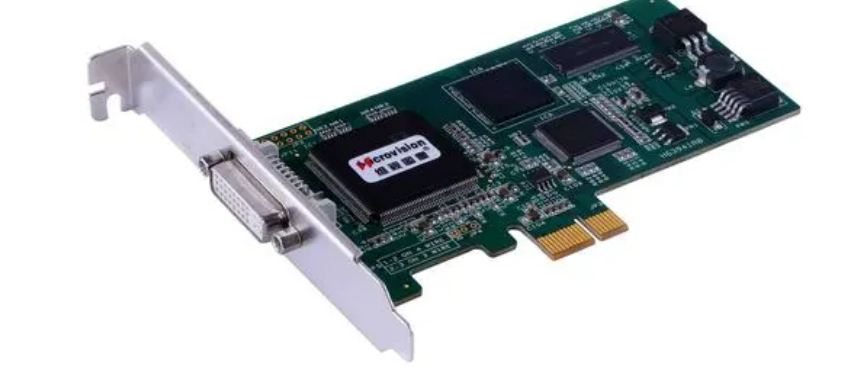
It has been said that there are only two kinds of electronic engineers in the world: those who have experienced electromagnetic interference and those who have not. With the increase of PCB wire delivery, EMC design is a problem that we electronic engineers have to consider. Faced with a design, there are five important attributes to consider when conducting EMC analysis of a product and design:
(1) Key device size: the physical size of the emitting device that generates radiation. Radio-frequency (RF) currents will generate an electromagnetic field that will leak out of the housing through it. The wire length on PCB as the transmission path has a direct effect on the RF current.
(2) Impedance matching: the impedance of the source and receiver, and the transmission impedance between them.
(3) The temporal nature of the interference signal: whether the problem is a continuous (periodic signal) event, or whether it is only a specific operating cycle (for example, a single keystroke or power-on interference, periodic disk drive operation or network burst transmission).
(4) The intensity of the interference signal: how strong the source energy level is, and how much potential it has to produce harmful interference.
(5) Frequency characteristics of interference signals: waveform observation is carried out with a spectrum analyzer. Where is the observed problem in the spectrum? It is convenient to find the problem.
In addition, some low-frequency circuit design habits need attention. For example, my usual single-point grounding is very suitable for low-frequency applications, but when I talked with the company boss, I found that it is not suitable for the RF signal situation, because there are more EMI problems in the RF signal situation. It is believed that some engineers apply single point grounding to all product designs without realizing that using this grounding method may create more or more complex EMC problems.
We should also pay attention to the current flow within the circuit components. With circuit knowledge we know that current flows from high voltage to low voltage, and that current always flows through one or more paths in a closed loop circuit, so a minimum loop and a very important law. For those directions where interference current is measured, PCB wiring is modified so that it does not affect the load or sensitive circuit. Applications that require a high impedance path from the power supply to the load must consider all possible paths through which the return current can flow.
There is also a PCB wiring problem. The impedance of a conductor or wire consists of resistance R and inductive reactance. Impedance at high frequencies, no capacitive reactance exists. When the line frequency is higher than 100kHz, the conductor or line becomes an inductor. The wires or wires that work above the audio may become radio frequency antennas. In EMC specifications, it is not allowed for conductors or wires to operate below λ/20 of a certain frequency (the design length of the antenna is equal to λ/4 or λ/2 of a certain frequency). When the design is not careful, the wires become a highly efficient antenna, which makes later debugging more difficult.
Finally, the PCB layout. First, the size of PCB should be considered. When the size of PCB is too large, the anti-interference ability of the system decreases and the cost increases with the increase of the wiring, while the size is too small and easy to cause the problem of heat dissipation and interference. Second, to determine the position of special components (such as clock components) (it is best that the clock line is not paved around the ground and do not go up and down the key signal line, to avoid interference). Third, according to the circuit function, the overall layout of PCB. In component layout, relevant components should be as close as possible, so that better anti-interference effect can be obtained.
6. Design Rule Check (DRC)
After the wiring design is completed, it is necessary to carefully check whether the wiring design conforms to the rules formulated by the designer, and also confirm whether the rules formulated meet the requirements of the printed board production process. The general inspection includes the following aspects: Whether the distance between wire and wire, wire and component pad, wire and through hole, component pad and through hole, through hole and through hole is reasonable, whether it meets the Production requirements. Whether the width of the power cord and ground wire is appropriate, whether the tight coupling between the power supply and ground wire (low wave impedance) is there any place in the PCB where the ground wire can be widened.
Are optimal measures taken for critical signal lines, such as minimum length, protected lines, and clearly separated input and output lines. Analog circuit and digital circuit parts, whether there are independent ground. Whether the graphics (such as ICONS, marking) added to the PCB will cause signal short circuit. Modify some lines that are not ideal. Is there a process line on the PCB? Whether the solder resistance meets the requirements of the production process, whether the solder resistance size is appropriate, whether the character mark is pressed on the device pad, so as not to affect the quality of the electrical equipment. Whether the outer frame edge of the power layer in the multilayer panel is reduced, such as the copper foil of the power layer exposed outside the panel, it is easy to cause short circuit.
7. Design of through hole (via
Through hole (via) is one of the important components of multilayer PCB, the cost of drilling usually accounts for 30% to 40% of the PCB board. Simply put, every hole in the PCB can be called a pass hole. From the point of view of function, the hole can be divided into two categories: one is used as an electrical connection between the layers; The second is used for fixing or positioning devices. In terms of technological process, through holes are generally divided into three categories, namely blind via, buried via and through via.