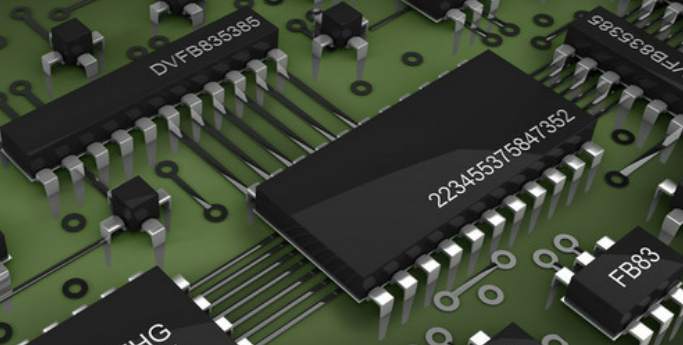
The charge flowing into the transmission line (which ultimately comes from the signal source) is used to charge the capacitor δC formed between the signal line added during transmission and the return path to the voltage V, so
The delta delta Q = V C
We can relate the capacitance caused by every certain distance the signal travels in the process of propagation with the capacitance value CL of the unit length of the transmission line and the speed U of the signal propagating on the transmission line. And the distance the signal travels is the velocity U times the time interval delta t. So
The delta C = CLU delta t
Combining all the above equations, we can derive the instantaneous impedance as follows:
Z = V/I = V/(delta Q/delta t) = V/(C/V delta delta t) = V/(VCLU delta t/delta t) = 1 / (CLU)
It can be seen that the instantaneous impedance is related to the capacitance value per unit line length and the speed of signal transmission. It can also be artificial and this is the definition of the characteristic impedance of a transmission line. In order to distinguish the characteristic impedance from the actual impedance Z, a subscript 0 is specially added to the characteristic impedance. The characteristic impedance of the signal transmission line has been obtained from the above derivation:
Z0 = 1 / (CLU).
If the capacitance value per unit length of the transmission line and the speed at which the signal propagates along the transmission line remain constant, the transmission line has a constant characteristic impedance throughout its length, and such a transmission line is called a transmission line with controlled impedance.
It can be seen from the above brief description that some intuitive knowledge of capacitance can be related to the intuitive knowledge of the newly discovered characteristic impedance. In other words, if the signal wires in the PCB are widened, the capacitance per unit length of the transmission line increases and the characteristic impedance of the transmission line decreases.
Confusion about the characteristic impedance of transmission lines is often heard. From the above analysis, it is known that after connecting the source to the transmission line, you should see the characteristic impedance of the transmission line for a certain value, say 50Ω, whereas if you connect an ohmmeter to a 3-foot length of RG58 cable, the measured impedance is infinite. The answer to the question is that the impedance from the front of any transmission line varies with time. You can measure the surge impedance or characteristic impedance of a cable if the time you measure the impedance of the cable is short enough to match the time it takes the signal to travel up and down the cable. However, if you wait enough time, some of the energy will be reflected back and detected by the measuring instrument, and then the impedance change can be detected. Usually, during this process, the impedance will change back and forth until the impedance value reaches a stable state: If the end of the cable is open, the final impedance value is infinite, if the end of the cable is short, the final impedance value is zero.
For 3-ft long RG58 cables, impedance measurements must be completed within a time interval of less than 3ns. That's what the time domain reflectometer (TDR) does. TDR can measure the dynamic impedance of a transmission line. If it takes a 1s interval to measure the impedance of a 3-foot RG58 cable, and the signal has bounced back and forth millions of times in that interval, you can get completely different impedance values from huge changes in impedance, and end up with infinity because the end of the cable is open.
Precise profiles can be formed on sensitive coverings by laser processes
A similar process applies to the FPC covering film. Covering film is usually composed of polyimide and adhesive layer with thickness of 25μm or 12.5 μm, and is easily deformed. Individual areas (such as pads) do not need to be covered by film for later assembly, connection, etc.
The thin material is very sensitive to mechanical stress -- easily done by non-contact laser processing. At the same time, the vacuum adsorption table can fix its position well and maintain its flatness.
Soft and hard plate processing
The rigid PCB and the flexible PCB are pressed together to form a multi-layer board. During the pressing process, the top of the flexible PCB is not pressed and bonded with the rigid PCB. The rigid cover covered on the flexible PCB is cut and separated by laser fixed depth cutting, leaving the flexible part to form the soft and hard binding board.
This kind of fixed depth machining is also applicable to the blind groove machining of integrated components embedded on the surface of multilayer plates.The UV laser precisely cuts the blind slots of the target layer separated from the multilayer circuit board. In this area, the target layer cannot form a connection with the material covered above it.
High efficiency PCB and FPC board
Post-SMT splicing is the process of cutting circuit boards where various electronic components have been assembled, which is already at the end of the production chain. For subboards, different techniques are available: for conventional PCBS, traditional knife cutting, stamping and contour milling processes are preferred. For more complex electronic circuit and thin substrate especially to mechanical stress, dust and size deviation is very sensitive to the situation, the use of UV laser cutting board has more advantages. The following three charts evaluate the three approaches in terms of different factors.
Figure 4: Comparison of splitter methods: Other methods cannot achieve the quality of UV laser splitter
For full contour cutting, LPKF recommends cutting material thickness of no more than 1.6 mm depending on the laser source used. For some thicker materials, as well as expensive assembly components, safety and quality aspects are prioritized over cutting time.
Figure 5: In Tab-Cut, the laser cuts the breakpoint splice
By cutting the breakpoint plate, the laser system cuts the connection points through a process described earlier. This cutting process can be performed with components close to the edge and is economical for thicker boards.
Other application fields
Because UV laser wavelength is short, it can be used for most material processing. In the electronics industry, for example, it can be used to:
● TCO/ITO glass is processed without damage to the base
● Drill holes in flexible or thin materials
● Welding resistance layer or covering film opening window
● Rigid flexible/flexible circuit board
● Slotting
● Assembled or unassembled circuit board repair
● Cut sintered ceramics
● Precision cutting LTCC
In Tab-Cut, the laser cuts the breakpoint splice
The UV laser system can also cut, write, and drill LTCC components in a single processing job.