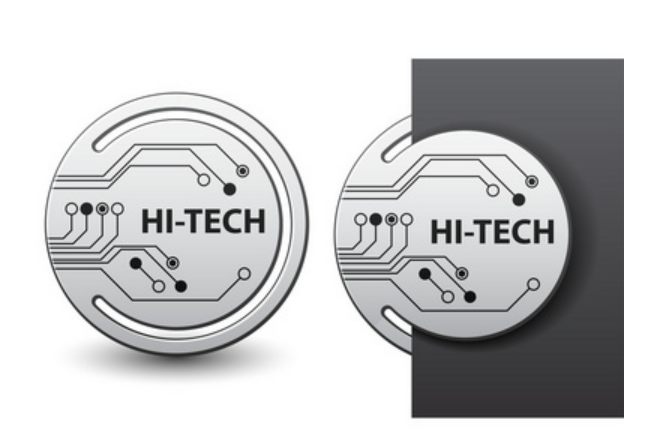
The same "isolation zone" shall be set up between the chassis floor and the circuit floor of each layer; If possible, keep the spacing at 0.64mm.
At the first and bottom layers of the card near the mounting holes, connect the chassis floor and circuit floor with 1.27mm wide wires along the chassis ground wire every 100mm. Adjacent to these connection points, a pad or mounting hole for mounting is placed between the case ground and the circuit ground. These ground connections can be cut open with a blade to keep the circuit open, or a jump with a magnetic bead/high frequency capacitor.
If the circuit board will not be placed in a metal case or shielding device, do not apply solder resistance on the first layer of the circuit board and the bottom case grounding wire, so that they can be used as ESD arc discharge electrode.
To set up a ring around the circuit in the following manner:
(1) In addition to the edge connector and chassis floor, the entire perimeter is placed on the ring path.
(2) Ensure that the annular ground width of all layers is greater than 2.5mm.
(3) Connect the rings with holes every 13mm.
(4) Connect the ring ground to the common ground of the multilayer circuit.
(5) For the double panel installed in the metal case or shielding device, the ring should be connected with the circuit common ground. An unshielded double-sided circuit should be connected to the ring floor. The ring floor should not be coated with solder resistance so that the ring can act as an ESD discharge. A gap of at least 0.5mm wide should be placed somewhere on the ring floor (all layers) to avoid forming a large loop. The distance between signal wiring and ring ground should not be less than 0.5mm.
1, the input end and the output end of the line should avoid parallel adjacent, so as to avoid interference. Grounding should be added when necessary, two adjacent layers of wiring should be vertical to each other, parallel easy to produce parasitic coupling.
2. Add decoupling capacitance between power supply and ground wire. It is better that the ground cable is wider than the power cable. The relationship between them is ground cable > power cable > signal cable. Usually, the width of signal cable is 0.2 ~ 0.3mm, and the width can reach 0.05 ~ 0.07mm
3, digital circuit and analog circuit common ground processing, digital circuit frequency is high, analog circuit sensitivity is strong, for the signal line, high frequency signal line as far as possible away from the sensitive analog circuit devices, for the ground wire, rectifier PCB to the outside only one node, so ** in the PCB internal processing number, mode common ground problem, And inside the board the digital and analog ground is actually separate and they are not connected to each other, only in the PCB and the external connection interface (such as plugs, etc.). There is a little bit of short circuiting between digital and analog, but note that there is only one connection point. There are also differences on the PCB, which is determined by the system design.
4. Shorten the connection between high-frequency components as far as possible, and try to reduce their distribution parameters and electromagnetic interference between each other. Easily disturbed components should not be too close to each other, input and output components should be as far away as possible. There may be a high potential difference between some components or wires. The distance between them should be increased to avoid accidental short circuit caused by discharge. Components with high voltage should be arranged as far as possible in places that are not easily touched by the hand during debugging.
5. For circuits working at high frequency, the distribution parameters between components should be considered. General circuits should be arranged as parallel as possible. In this way, not only beautiful. It is easy to assemble and weld. Easy to mass produce.
6. Input and output wires should be avoided as far as possible. It is better to add ground wire between lines to avoid feedback coupling.
7, printed wire bend generally take circular arc, and right Angle or included Angle in high frequency circuit will affect the electrical performance. If you must take a right Angle, generally use two 135 degrees to replace the right Angle.
8. Power cord design
According to the size of the printed circuit board current, try to rent the width of the power line, reduce the loop resistance. At the same time, the direction of the power cord and ground wire is consistent with the direction of data transmission, which helps to enhance the anti-noise capability.
9. Ground wire design
The principles of ground design are:
(1) digital and analog separation. If the circuit board contains both logical and linear circuits, keep them as separate as possible. Low frequency circuit should be as far as possible to use a single point of parallel grounding, the actual wiring difficulties can be partially connected after the parallel grounding. The high frequency circuit should be grounded in series at multiple points, the ground should be short and rented, and the high frequency element should be surrounded by a large area of grid foil as far as possible.
(2) The ground wire should be as thick as possible. If the grounding wire is very flexible line, the grounding potential changes with the change of current, so that the noise resistance performance is reduced. The ground wire should therefore be thickened so that it can pass through three times the allowable current on the printed board. If possible, the ground cable should be at least 2 mm to 3mm.
(3) The ground wire constitutes a closed-loop road. For printed boards composed only of digital circuits, the ground circuit is arranged into a group loop, which can improve the noise resistance.