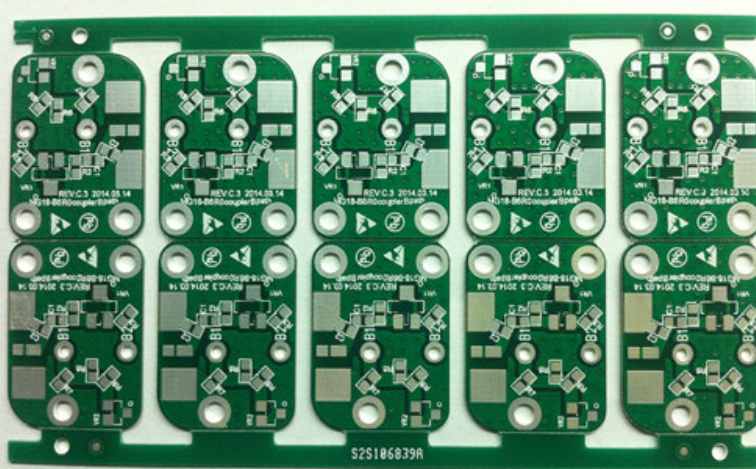
The so-called solder paste low viscosity phenomenon refers to the phenomenon that the parts have no way to be glued to the solder paste during or after the punching. Possible reasons for low viscosity include: insufficient tin paste coating, insufficient flux viscosity, inappropriate metal content, particle size is too rough, the circuit board moves quickly during the printing, the circuit board support is poor during the printing, the influence of humidity and so on.
If the solder paste circuit board printing is insufficient, the solder paste can not keep the parts on the circuit board is understandable. Flux is the decisive factor of solder paste adhesion, low viscosity flux will naturally produce low viscosity solder paste. Because tin powder itself can not provide viscosity, excess powder particles to maintain viscosity is not good. However, the relationship between metal content and viscosity is rather complicated. With the increase of metal content, the viscosity decreases rapidly at the beginning, and then the rate of decrease gradually slows down. The decreasing trend is probably related to the thickness of the test sample.
Generally speaking, the less the powder content, the more solder paste will be squeezed during the viscosity test period, and the smaller the gap between the test probe and the substrate, which is conducive to maintaining the integrity of the printing and avoiding leakage. When the metal content exceeds about 40%, according to the test experience value of a solder paste, the viscosity will increase slightly with the increase of metal content and then decrease.
The increase in viscosity should be due to the increase in cohesion caused by the reinforcement effect of packing. When the metal content exceeds a certain critical value, the viscosity will continue to decline because of the inadequate coating and bonding of the flux to the tin powder, which will gradually increase. The viscosity is proportional to the adhesive force and cohesion of the solder paste, which is dominated by a single element of flux. The cohesion will increase with the decrease of powder size, which is due to the increase of solder paste viscosity, resulting in an increase in viscosity.
The fastness of the piece is not only determined by the viscosity of the solder paste, but also by the complex problems involved in the equipment. For a piece of equipment, the use of some solder paste is good, but it is a pity to change the equipment on the problem. One of the important factors affecting the maintenance ability of parts is the movement of printed circuit board. If the circuit board is moving fast during the printing stage, the inertia of the part may exceed the adhesive force of the solder paste, which will cause the part to slip sideways.
Another factor is the stability of the circuit board itself when printing. If the circuit board is not well supported and fixed, when the impact of the placement arm, the circuit board will have a larger shake, so there will be a problem of dropping pieces. Proper process design should include a reasonable support mechanism and a solid fixture to hold the PCB board.
Viscosity is an important characteristic function of flux, some flux will quickly absorb water, humidity will inevitably affect the viscosity of solder paste. High humidity may cause surface crusting, solder paste thinning and viscosity reduction, these problems should be avoided.
When the solder paste just exposed to the air, there will be appropriate or high viscosity. However, after the printing of the circuit board, the viscosity decreases rapidly with time, which will make the operating range of the circuit board processing become very narrow.
Possible reasons for the short adhesive time include: too high metal content, too high solvent volatility, coarse powder size, the surface of the printed solder paste begins to develop hard skin, large air flow in the operating environment, improper humidity, high ambient temperature, the use of steel plate is too thin, and so on.
The problem of metal content has been discussed again and again. The stickiness time will be shortened with the increase of metal content. It is obvious that if the flux content is increased, it will inevitably increase the adhesive time of the solder paste, which can also be explained by the influence of the solvent content increase. This can understand many circuit board manufacturers or literature statements, there are reasons to keep the solder paste metal content does not exceed about 90% of the recommendations.
The increased surface area of the particles helps the solvent to retain for a longer time, which is due to the enhanced surface adsorption between the particles and the solvent. However, if the powder particles are small, the chemical reaction between the flux and the powder particles will be increased and faster, and the surface crust may be produced and the viscosity time will be reduced.