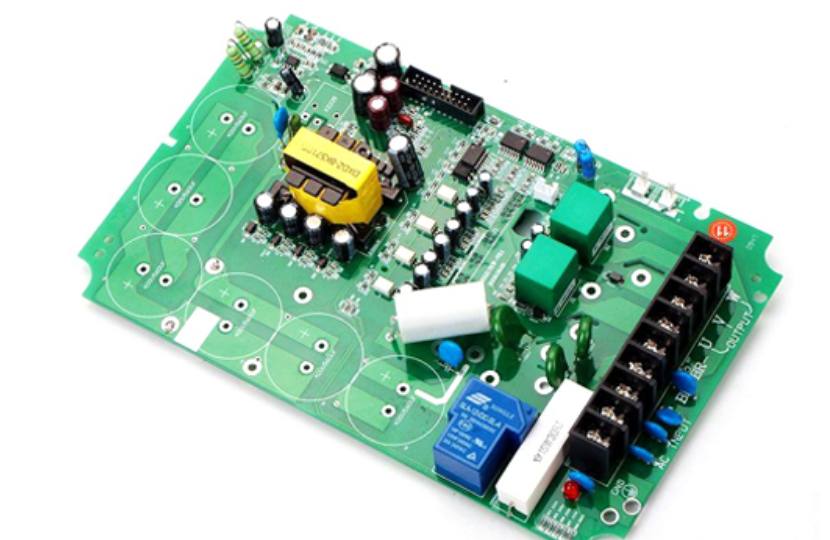
Many companies use [PCBA tracking bar code] so that the factory's field information management System (SFCS, Shop Floor Control System or SFDC, Shop Floor Data Collection system) can track the production quality of PCBA, And this [PCBA tracking bar code] printing also has several ways, from the initial label paper printing bar code after manual attachment, the use of ink jet printing bar code, to now many companies have introduced laser printing bar code can achieve this purpose.
With the development of science and technology, this kind of [PCBA tracking barcode] has evolved from the original one-dimensional barcode to two-dimensional barcode, which not only improves the information capacity of barcode, but also reduces the bar code area required.
The following conditions must be met when printing PCBA tracking bar codes:
Bar codes do not affect the appearance of products or mislead customers.
Bar codes must be clear enough to be interpreted using a scanner.
Bar codes must be able to withstand a certain amount of friction and last longer than a certain amount of time. This is for the future customer response quality problems can look back at the production of the record.
The advantages and disadvantages of the four main printing methods for PCBA barcode tracking in SMT or EMS plants are described below.
One, ordinary sticker bar code after the furnace manually attached
This is the most traditional way of barcode printing and paste. The choice of barcode sticker after the welding furnace is to avoid sticker or printed carbon ink high temperature caused by sticker deformation or handwriting loss, which generally requires manual attachment, more labor costs, and the barcode attached after the furnace means that the state in front of the furnace can not be traced. Sometimes even the AOI behind the furnace cannot be recorded, losing the most useful function of barcode tracking.
Two, high temperature sticker bar code solder paste before printing automatically attached
This is currently the most companies to use the operation, when the empty board on the PCBA bar code, generally have "automatic labeling" and "manual labeling" two methods.
The bar code in front of the furnace must be pasted with high temperature resistant label material and high temperature resistant carbon ink, the cost will be a little higher than ordinary stickers.
In theory, by pasting bar codes in front of the furnace, SFDC can record the quality status of the entire Circuit board assembly (PCBA) operation from the SMT empty board feeding, such as the status of SPI and AOI inspection, but if you want to record the part information above the PCBA, you may face more challenges.
In addition, there will be a problem that needs special attention in front of the furnace, because the bar code sticker has a certain thickness (generally about 0.08mm), this thickness will support the gap between the steel plate and the printed circuit board, will increase the amount of solder paste printing, some parts may cause short circuit (short) phenomenon, so the adhesive position must pay special attention to, Avoid sticking around fine spacing or small parts.
Three, ink jet printing bar code before solder paste printing
Ink-jet printing bar code can also be completed in the stage of empty plate, so it has all the advantages of [high temperature sticker bar code printing furnace automatically attached], relative to the thickness of the plate thickness of the ink is usually negligible, that is to say, it will not affect the quality of solder paste printing.
Ink jet printing must use fast drying ink, otherwise it is easy to stain the subsequent solder paste printing and eat the risk of bad tin, the disadvantage is that the ink storage environment is a little troublesome, and the ink must be used up within the specified time after opening, some may also have to use UV lamp to cure ink.
Four, solder paste before printing laser engraving bar code
More and more companies are adopting PCB "laser-engraved barcodes" because they have all the advantages of [pre-solder inkjet barcodes] without the need to use ink, so there is no risk of ink storage and ink staining.
However, the biggest difference between laser engraving and the first three methods is that laser is used to "remove materials", and other methods are used to increase materials.
Laser engraving is mainly to remove the anti-welding green paint or silk screen white paint on the circuit board and form burn marks, so in the use of laser engraving must pay special attention to its energy can not hurt the anti-welding green paint or silk screen white paint below the copper foil, it is best not to expose the copper foil, otherwise exposed copper foil may have oxidation risk, may affect the characteristics of some products. It is recommended to make a special area printed with white paint to make laser barcodes, which can achieve good barcode recognition rate and avoid damaging copper foil.
Laser engraving is also a point to note, that is, the color of PCB circuit board welding is best "green", this is because the scanning equipment is almost all red, if the use of red welding, almost unable to distinguish bar codes, black welding is not recommended, blue welding barely can.