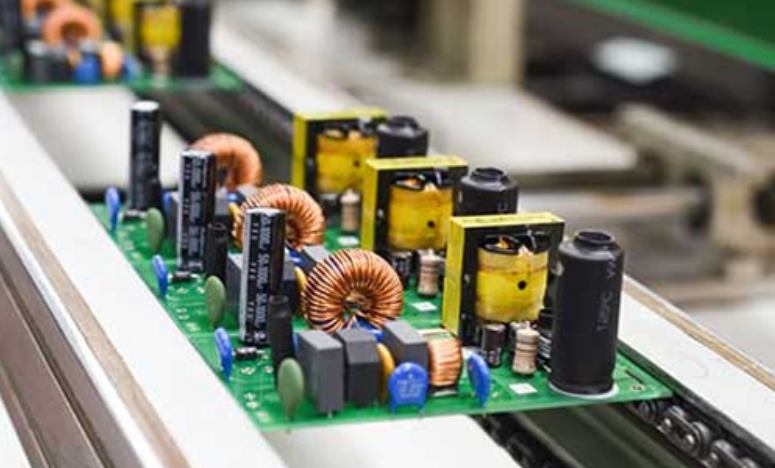
SMT advantage
SMT has the following advantages over traditional through-hole insert technology:
(1) Smaller components. In 2012, it achieved 0.4*0.2mm (0.016* 0.008in: 01005), and has the development trend of miniaturization
(2) Higher component density (number of components per unit area) and more connections per component
(3) Higher connection density
(4) Lower cost and time (on-line production)
(5) Fewer holes in PCB design and production
(6) More simple and fast mounting
(7) Minor errors in component mounting will be automatically repaired by stretching due to surface tension of the melted solder paste
(8) Components can be mounted and welded on the upper and lower sides of the plate
(9) Lower resistance and inductance effects, resulting in less RF signal effect
(10) Better mechanical properties under vibration and drop
(11) Many SMT components are cheaper than plug-in components
(12) Better EMC performance, resulting in lower electromagnetic radiation due to smaller electromagnetic coils
SMT disadvantage
(1) Due to the smaller size and SMD lead spacing, manual repair at mount or component level is more difficult, requiring skilled workers and more expensive repair tools
(2) The SMD component cannot be used directly in the plug-in motherboard (a quick test and proofing tool). A custom printed circuit board is required or the SMD component is soldered to the pin carrier.
(3) SMD solder connections may be damaged by perfusion components during the thermal cycle
(4) SMT welding joints become smaller and smaller spacing, resulting in higher precision SMT process requirements
(5) SMT is not suitable for large volume, high energy, high voltage components, such as transformers in power circuits, etc. It is common to integrate SMT and plug-in processes together.
(6) SMT is not suitable for applications with frequent mechanical stress. For example, some connectors are used as interfaces to connect with the outside. Frequent plug and plug poses challenges to the stability of welding
SMT repair
In the whole process of PCB processing, SMT problem components are often repaired by electric soldering iron or non-contact repair system. In general, a reworking system is a better option, because servicing SMD components requires considerable skill and is not easy. Non-contact welding repair method: infrared welding and hot gas welding.
Infrared mode
By infrared welding method, the welding is heated and melted by long and short wave electromagnetic induction. The advantages are:
(1) Recommended installation
(2) no pressurized air
(3) No need for different components of the nozzle, reduce the cost of replacing the nozzle
(4) The response of fast infrared source
disadvantage
(1) The central region is heated more than the peripheral region
(2) The temperature control is not accurate enough, and it is easy to reach the peak value
(3) Surrounding components need to be covered to avoid damage, which requires more time
(4) The surface temperature depends on the reflectivity of the element
(5) The temperature depends on the surface shape, and the convection energy loss will reduce the temperature of the element
(6) There is no possibility of reflux atmosphere
Hot gas mode
In hot gas welding, the energy heated at the joint is transferred by hot gas, usually with air or nitrogen. advantage
(1) Imitate the scene in reflow welding
(2) Some systems allow switching between hot air and nitrogen
(3) Standard element nozzle, with higher stability and fast processing process
(4) Renewable welding is allowed
(5) Sufficient heat energy, a large number of components can be heated
(6) heat evenly
(7) element heating temperature will not exceed the set gas temperature
(8) Rapid cooling after reflux results in smaller weld lines
Disadvantage: The thermal performance of the heat generator leads to slower reaction. Reworking usually corrects errors caused by humans or machines and involves the following steps
Melt the solder and move the element
Move the residual solder
Direct or distributed printing solder paste on PCB board
Attach new element and reflow weld
In some cases, hundreds or thousands of identical components need to be repaired. This error often occurs and is caught during the mounting process. However, when it is found too late, it is necessary to face mass maintenance, and targeted maintenance strategies are needed to ensure the quality of maintenance