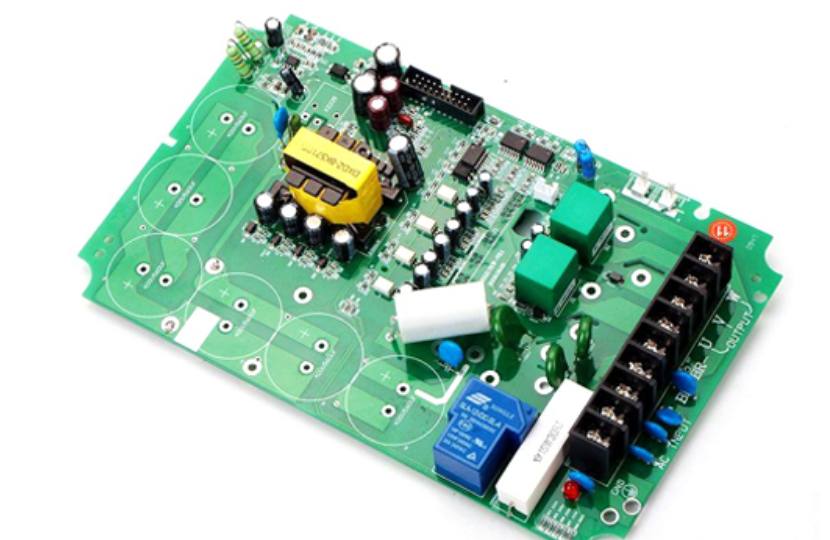
The concept of DFM was first proposed by the American Assembly Association in 1995, which was limited to printed circuit boards (PCB). In the late 1990s, it was introduced into China by Professor Xue Jingcheng from Singapore. "Circuit manufacturability design" is a new design concept put forward in 1998. It does not involve the specific circuit design, nor does it introduce the specific process method. What it wants to solve is the interface relationship between circuit design and electronic manufacturing. Its purpose is to accelerate the development progress, reduce the production cost, and establish a rapid response platform for our electronic products. And the quality of the product is often in the circuit design and process of the interface between manufacturing! Its typical manifestation is: design does not know how to manufacture, and the process does not know how to design.
printed circuit board manufacturability design is an advanced design concept emerging in the middle of 1990s. Circuit manufacturability design involving printed circuit board, complete machine and unit module, radio frequency cable assembly, multi-core radio frequency cable assembly and microwave circuit module is the frontier technology and advanced design concept of electronic manufacturing industry in the 21st century.
In order to develop the miniaturization and reliability of electronic products, the electronic research institute and the production unit must attach great importance to the design of manufacturability, strive to create the enterprise design culture of manufacturability, and improve the design of manufacturability into the new product introduction process of the electronic research institute and the production unit. Only by establishing strict and perfect import process of electronic products manufacturability design, can we ensure that the designed products meet the actual situation of the unit and establish a rapid response platform of electronic equipment.
Manufacturability design is a system engineering that can be roughly divided into board level and machine/cable component level in terms of electronic assembly. Board level can be divided into general PCBA and Micro-PCB-PCBA. The manufacturability design content of PCBA alone is very rich, including :PCBA manufacturability design defects case analysis; Basic concept of circuit manufacturability design; The relationship between circuit manufacturability design and forbidden (limited) process; Core concept of modern electronic assembly; PCBA-DFM program; PCB drawing regulations and the relationship with electronic assembly; Acceptable conditions for highly reliable PCBS; High reliability electronic equipment electronic components selection requirements; The basic contents of PCB manufacturability design apply SMT component layout design and chip component pad design; SMT component pad design; Application of wave-crest welding technology component layout design and welding plate graphic design; Component installation design; PCBA testability design (DFT) other design experience SMTequipment design requirements; PCB manufacturability design audit PCBA lead-free mixed process DFM and welding technology.
How to ensure product quality from DFM-DFA and electronic assembly logistics process control and process optimization design? How to comply with prohibited process requirements? How to optimize the process design of cable assembly and microwave circuit board? What kind of design and assembly can meet the requirements of welding quality of electronic machine, microwave module and cable assembly? And how to correctly set and verify the welding temperature of manual welding? And so on.
The scope of DFM involves the whole electronic equipment, so the development and application of PCBA-DFM analysis software requires a strong technical foundation.