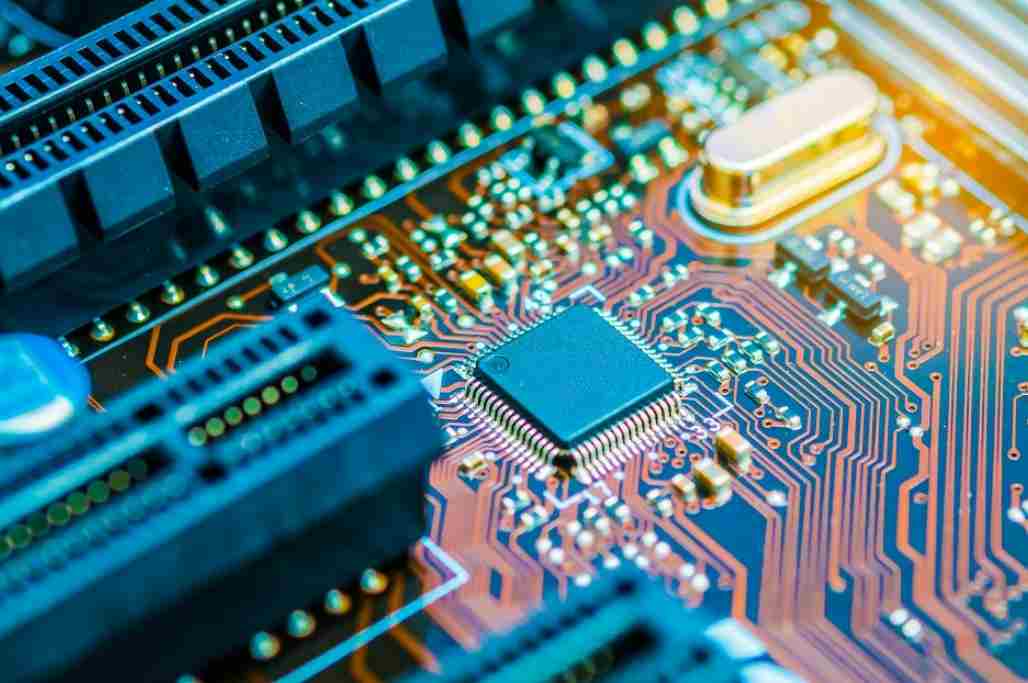
SMT technology, as a new generation of mounting technology, only has a history of more than 40 years, but this technology has fully shown its strong vitality at the beginning of the world. It has gone through the journey from birth, perfection to maturity with extraordinary speed, and entered the flourishing period of large-scale industrial application. Now, whether it is investment electronic products or civilian electronic products, there are its shadow. Why is SMT developing so fast? This is mainly due to the following advantages of SMT.
1. High assembly density
Chip components than the traditional punched components of the area and mass is greatly reduced. Generally, the use of SMT can reduce the size of electronic products by 60% ~ 70%, 75% quality. The through-hole installation technology is based on 2.54mm grid installation components; The SMT assembly component grid has been developed from 1.27mm to the current 0.5mm grid, with a higher density of installed components. For example, a DIP integration block with 64 pins has an assembly area of 25mm×75m, while the same lead uses a QFP with 0.63mm lead spacing and has an assembly area of 12mm×12mm, which is 1/12 of the through-hole technology.
2. High reliability
Due to the high reliability of chip components, small and light components, so strong anti-seismic ability, can adopt automatic production in electronic processing, high mounting reliability, generally bad solder joint rate is less than 10 million, an order of magnitude lower than through hole insertion components peak welding technology, electronic products assembled with SMT MTBF average 250,000 hours, SMT technology is used in almost 90% of electronic products.
3. Good high-frequency characteristics
As chip components are firmly mounted, the components are usually leadless or short leads, which reduces the influence of parasitic inductance and capacitance, and improves the high frequency characteristics of the circuit. The maximum frequency of the circuit designed by SMC and SMD is 3GHz, while that of the through-hole components is only 500MHz. SMT can also shorten the transmission delay time and can be used in circuits with clock frequency of 16MHz or more. If MCM technology is used, the high-end clock frequency of computer workstation can reach 100MHz, and the additional power consumption caused by parasitic reactance can be reduced to 1/3 ~ 1/2 of the original.
4. Reduce costs
Printed board use area is reduced, the area is 1/12 of the through hole technology, if using CSP installation, its area will be greatly reduced.
The number of holes in the printed board is reduced, saving the cost of repair.
As the frequency characteristic is improved, the cost of circuit debugging is reduced.
The small size and light weight of chip components reduce the cost of packaging, transportation and storage.
With the rapid development of SMC and SMDS, the cost is falling rapidly. The price of a chip resistor and a through-hole resistor is already less than 1 cent RMB.
5, easy to automate production
At present, to achieve full automation of perforated printed circuit board installation, it is necessary to expand the original printed board area by 40%, so that the automatic plug-in cartridge head to insert the components, otherwise there is not enough space clearance, will damage the components. The automatic placement machine adopts vacuum suction and discharge components. The vacuum suction nozzle is smaller than the component shape, which can improve the installation density. In fact, small components and fine spacing QFP components are produced by automatic SMT machine, in order to achieve full automatic production.
Of course, there are also some problems in the mass production of SMT. For example, the nominal values on components are not clear, which brings maintenance difficulties and special tools are needed. Multi-pin QFP is easy to cause pin deformation and lead to welding failure. The thermal expansion coefficient between components and circuit boards is inconsistent, and the solder joints are subjected to expansion stress when the electronic equipment is working, resulting in solder joints failure; In addition, the integral heating of components during refluidwelding will also lead to the thermal stress of the components, which will reduce the long-term reliability of its electronic products. However, these problems are in the process of development. With the emergence of special disassembly equipment and new low expansion coefficient printed boards, they are no longer obstacles to the further development of SMT.