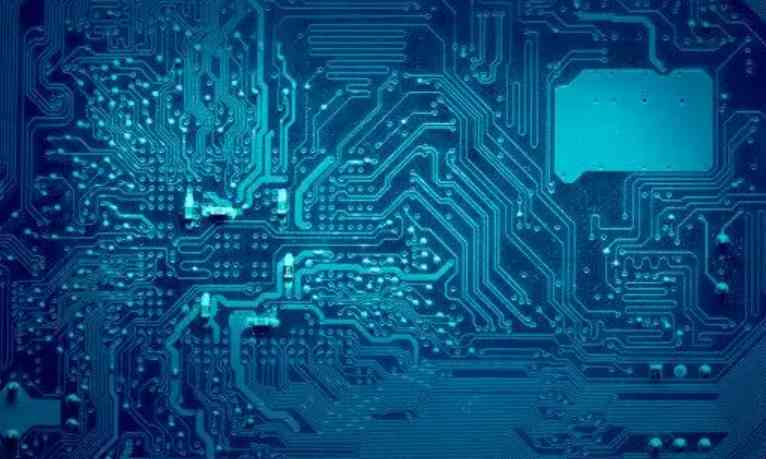
In the rapid update of electronic products now, PCB printing from the previous single-layer board expanded to double-layer board and high precision requirements of more complex multi-layer board. Therefore, the circuit board hole processing requirements are more and more, such as: the aperture is smaller and smaller, hole and hole spacing is smaller and smaller. It is understood that epoxy resin matrix composites are used more in plate factories now. The definition of hole size is that the diameter below 0.6mm is small hole, and the diameter below 0.3mm is micro hole. Today I will introduce the processing method of small holes: mechanical drilling.
In order to ensure high processing efficiency and hole quality, we reduce the ratio of defective products. During mechanical drilling, both axial force and cutting torque are taken into account which may directly or indirectly affect the quality of the hole. Axial force and torque with the feed, the thickness of the cutting layer will also increase, then the cutting speed will increase, so that the number of cutting fibers per unit time will increase, the amount of tool wear will increase rapidly. Therefore, different sizes of holes, drill tool life is not the same, operators should be familiar with the performance of the equipment in time to replace the drill tool. This is why the cost of processing small holes is higher.
In the axial force, the static component of FS affects the wide cutting of the transverse edge, while the dynamic component of FD mainly affects the cutting of the main cutting edge. The dynamic component of FD has a greater effect on the surface roughness than the static component of FS. Generally, when the aperture of prefabricated hole is less than 0.4mm, the static component FS decreases sharply with the increase of the aperture, while the dynamic component FD decreases flatly.
The wear of PCB bit is related to cutting speed, feed rate and slot size. The ratio of bit radius to glass fiber width has a great influence on tool life. The larger the ratio is, the larger the cutting fiber bundle width is, and the higher the tool wear is. In practice, the 0.3mm drill tool life can drill 3000 holes. The bigger the drill knife, the fewer holes will be drilled.
In order to prevent drilling when encountering stratification, hole wall damage, stains, burrs, these problems, we can in the stratification of the first in the following put a 2.5mm thickness of the plate, the copper plate on the plate above, and then on the copper plate above the aluminum, aluminum role is 1. Protect the surface of the board will not wipe flowers. 2. Good heat dissipation, the drill will generate heat when drilling. 3. Buffer function/lead function to prevent deviation hole. The way to reduce burrs is to use vibration drilling technology, using carbide drill bit drilling, hardness is good, the size and structure of the tool also need to be adjusted.
What is the importance of BOM in PCB Assembly
PCB production involves a variety of raw materials and needs to be assembled before actual production can begin. How to determine the PCB raw material requirements? Bill of Materials (BOM) is the answer. The appropriate PCB component material list enables you to know the exact components and materials required, as well as their brand, quantity, size, and other details. Typically, in the case of PCB assembly, the BOM includes a list of wires, boards, surface mounted components and circuit requirements, etc. This article discusses the importance of BOM for PCB assembly and other relevant factors.
What is a Bill of Materials (BOM)?
A bill of Materials (BOM) is a list of the raw materials, components, and parts needed to make a specific final product. It mainly includes part number, name and quantity. It may also have a manufacturer or supplier name, other feature columns, and comment sections. This is the key link between the customer and the manufacturer, and it provides detailed information about the items purchased. If the product is to be produced within the organization, it can also be made available to internal departments.
Why is BOM important for PCB assembly?
Designing PCBS and then assembling many of them is very complicated. Therefore, it is vital that you fill in the information accurately. Here are some reasons why BOM is important:
l This list is handy, so you know exactly what materials you have, how many and what spare parts you need.
It also estimates the number of employees needed for a particular assembly based on the parts purchased.
L BOM helps with proper planning and smooth operation.
A BOM is required for auditing, which helps keep track of parts purchased and available parts in stock.
l It is essential to get exactly the part you want or the part made by a particular manufacturer.
l If not available, other options can be discussed and provided immediately.
Factors to consider when making a BOM
If you receive an order for 50 PCB components from a consumer electronics manufacturer, here are some things to consider when making a BOM:
l It is not a good idea to consider the full number you think you need (50 PCB components at a time).
l Instead consider a PCB component, find out the type of PCB and the required components, and list part details for only one component.
l Have your team of engineers figure out all the parts you need.
l Send the list to your customer for verification.
l Almost always, you may need more than one BOM.
l Finalize the BOM after final discussions with your team and customer.
It is critical that lBOM answers the "when," "what," and "how" questions related to the project.
Therefore, never do a BOM hastily, as it is easy to miss some parts or mention the wrong amount. This leads to a lot of back and forth emails and wasted production time. Most companies provide BOM in a format that is easy to fill out. However, in addition to the BOM, it is critical that your PCB components be accurate and functional. Therefore, dealing with reliable PCB component manufacturers and service providers is critical.