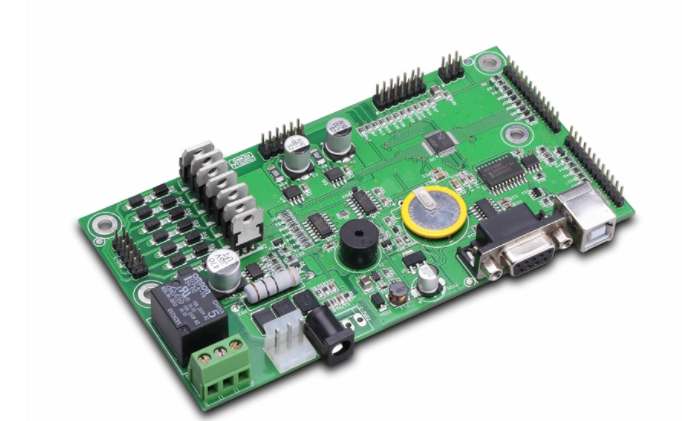
As grille array packages grow larger, it becomes more difficult to set security levels for these steps. As the use of lead-free equipment expands, so does the interest of users; Because there are a lot of users facing quality issues. As interest grew, IPC felt it was necessary to help other companies develop testing methods that would ensure that BGA was not damaged during manufacturing and testing.
1. How to select an SMT factory
As a link in the entire electronic product manufacturing process, with highly developed equipment and perfect management, the professional Cooperation of SMT processing plant seems to determine whether your PCBA board can be delivered on time, whether the quality can be controlled, and whether it can be repaired in time. The added value is much higher than the unit price difference between 8 and 9 per cent. How to check the cooperation degree of ? Start with people. Talk with the management and even the boss of the SMT factory to see if they havSMT factorye a sincere attitude and belief. In addition, the third party can also know the reputation of the processing plant and the customer cases served and so on.
2, Quality Control process (Quality Control) Many SMT processing plants in order to reduce the unit price in the market, at the risk of sacrificing quality, reduce QC personnel or do not equip with AOI for testing and other means. In the process of evaluating SMT processing plant, it is necessary to observe and understand in detail whether IQC, post-furnace inspection, QC and other series positions are set up in the warehouse, whether AOI inspection equipment is reasonably equipped, whether it is opened and used, and how engineers introduce quality management methods and documents, etc. Only with a comprehensive understanding, can you ensure that your products can be perfectly processed.
The spiritual outlook of front-line employees and managers determines whether your products can maintain high yield, consistency, etc., because products are made by people or operating equipment. Whether the communication with the manager is smooth, whether there is passion, whether the staff work meticulously, each does his job.
4. Give Up These Audits · Look at factory scale: Unless your order is enough for 100k, any SMT factory can do it · Look at SMT equipment: Unless PCB board has very small material (such as 0201 and below) or complex process (POP, etc.), general factory SMT equipment can be done. · Look at the quotation: If the quotation is slightly out of line at the first glance, one SMT factory will be rejected, and it may be a very good one. Those who dare to say anything are competent and have requirements on quality. The initial quotation can only be referred to, or even not referred to. It is very risky to choose this supplier based on the chest pounding promise of SMT factory or happy chat. Good companies have long-term stable SMT processing plants, but poor companies are always looking for, repeat yesterday's story. It's time to reflect on your purchasing behavior. Grasp the above several methods to select SMT factory, can be in the choice of suppliers without disadvantage.
2. How to reduce the failure of SMT patch processing
Testing and so on put a lot of mechanical stress on the package, which can lead to failure. As grille array packages become larger and larger, SMT patch processing is how to reduce the number of failures! SMT fabrication, handling and printed circuit assembly (PCA) testing can cause a lot of mechanical stress on the package, which can lead to failure. As grille array packages grow larger, it becomes more difficult to set security levels for these steps. As the use of lead-free equipment expands, so does the interest of users; Because there are a lot of users facing quality issues. As interest grew, IPC felt it was necessary to help other companies develop testing methods that would ensure that BGA was not damaged during manufacturing and testing.
This work was carried out jointly by the IPC 6-10d SMT Accessories Reliability Test Methods Working Group and the JEDEC JC-14.1 Packaging Equipment Reliability Test Methods Sub-Committee and has been completed. The test method specifies eight contact points arranged in a circular array. A PCA with a BGA in the center of the PCB is arranged so that the component is mounted face down on the support pins and the load is applied to the back of the BGA. Position the strain gauge adjacent to this component in accordance with the recommended gauge layout of IPC/JEDEC-9704. The PCA will be bent to relevant tension levels, and failure analysis can determine the extent of damage caused by bending to these tension levels. The tension level without damage can be determined by an iterative method, which is the tension limit.
SMT patch processing advantages: high assembly density, small size of electronic products, light weight, the size and weight of the patch components is only about 1/10 of the traditional plug-in components, generally after the adoption of SMT, the size of electronic products reduced by 40%~60%, 60%~80% weight reduction. High reliability and strong vibration resistance. Low defect rate of solder joint. Good high frequency characteristics. Electromagnetic and radio frequency interference is reduced. Easy to realize automation, improve production efficiency. Reduce the cost by 30%~50%. Save materials, energy, equipment, manpower, time, etc. Due to the complexity of SMT processing process, there are many smt processing factories, which specialize in smt processing. In Shenzhen, thanks to the booming development of the electronics industry, Shenzhen smt processing has achieved a prosperity of the industry.
3. How to reduce the production cost of SMT patch processing
Global Wei technology to share with you how to reduce the production cost of SMT plant manufacturers! Product production cost is the total of direct materials, direct labor, expenses due to product quality problems, and other direct or indirect expenses actually consumed by an enterprise in the process of product production.
In the survey table of production costs of SMT enterprises, the percentages are generally as follows: equipment and maintenance account for 40% ~43% of the total cost, material loss account for 19%~22%, product repair and maintenance expenses account for 17%~21%, labor costs account for 15%~17% of the total SMT cost, and other expenses account for 2%. It can be seen from the above that SMT production costs are mainly concentrated in equipment and other fixed assets, repair and maintenance costs, raw material loss and scrap costs and SMT production materials costs. Therefore, the production cost can be reduced from the above aspects, which will be discussed later.
SMT production cost is generally divided into manufacturing cost and quality cost. Product manufacturing cost refers to the direct materials, direct labor and other direct expenses actually consumed by enterprises in the process of product production and service provision. In SMT production, direct materials refer to electronic components, screen printing templates, welding materials, dispensing materials, cleaning materials, etc. Wages, labor expenses, bonus allowances, overtime pay, etc., for directly engaged in SMT production; Other manufacturing expenses refer to all costs associated with the manufacturing process in addition to materials and labor, including various items consumed in the workshop, the cost of materials used for maintenance of machinery and equipment, water, electricity, lighting, air conditioning and office expenses used in production.
Quality cost is the cost caused by enterprises to ensure satisfactory quality and the loss caused by failure to obtain satisfactory quality. Among them, the prevention cost refers to the cost paid to prevent the occurrence of quality defects; Appraisal cost refers to the cost paid for testing, inspection and inspection in order to assess whether the product has the specified quality; Internal defect cost refers to the loss caused by the failure of the product to meet the specified quality requirements before delivery (in the whole process); External defect cost refers to the loss caused by the failure of the product to meet the specified quality requirements after delivery. External quality assurance cost refers to the cost incurred in providing objective evidence, demonstration and proof to meet the quality assurance requirements stipulated in the contract.