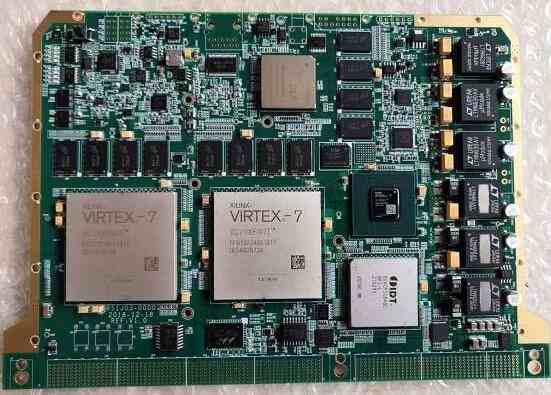
As SMT patch factory, customers provide information, make customers' ideas, data, qualified. To the customer, is our service. The key to realize this project is the selection of SMT patch processing plant. I plant has decades of processing experience, a few days of and you to talk about the advantages and disadvantages of SMT patch processing plant how to judge. The following patch processing manufacturer to explain the advantages and disadvantages of patch processing how to judge and PCBA processing solder paste how to choose the relevant knowledge.
1. How to choose PCBA processing solder paste
(1) According to the value and use of pcb circuit board products, high reliability products need high quality solder paste.
(2) Determine the activity of solder paste according to the storage time of PCB, components and surface oxidation degree. ① RMA grade is generally adopted. ② High reliability products, aerospace and military products can choose R grade. (3) PCB and components are stored for a long time and the surface is seriously oxidized. RA grade should be used and cleaned after welding.
(3) Select solder paste alloy components according to the assembly process of pcb board products, printed boards and components. ① The general lead-plated tin printed board uses 63Sn/37Pb. ② With palladium or palladium silver thick film end and pin poor weldability of components printed board using 62Sn/36 Pb /2Ag. (3) The gold plate generally do not choose the solder paste containing silver. ④ Sn-Ag-Cu alloy solder is generally selected for lead-free process.
(4) Choose whether to use no-clean solder paste according to the cleanliness requirements of the product (surface PCB Assembly board). (1) For no-cleaning process, solder paste without halogen or other weakly corrosive compounds should be selected. (2) High-reliability products, aerospace and military products and high-precision, weak signal instruments, as well as medical equipment involving life safety to use water cleaning or solvent cleaning solder paste, patch processing must be cleaned after welding.
(5)BGA. CSP, QFN generally need to use high quality no-clean solder paste.
(6) When welding thermal components, low melting point solder paste containing Bi should be selected.
(7) Select the particle size of alloy powder according to the assembly density of SMT patch processing (with or without narrow spacing). SMD pin spacing is also one of the important factors in selecting the particle size of alloy powder. The commonly used is No. 3 powder (25~45um) more narrow spacing is generally selected in the particle diameter of 40μm below alloy powder particles.
2. How to judge the quality of patch processing
1. Team:
The team includes business, production, procurement, engineering, quality, warehouse, after-sales, although the strength and ability of the team can not be reflected from the surface, but we can intuitively understand through some data, whether a company attaches importance to quality, whether the configuration of quality inspection personnel is sufficient or not, the configuration of the engineering team is incomplete can be used as a reference.
2. Equipment:
As the saying goes: "no diamond does not hold porcelain live", in the circuit board patch production equipment is. An important link, the production capacity, precision, efficiency of equipment is directly related to the production precision and quality of products.
3. Management:
Delivery time is also a link that we are more concerned about, a company's management is not scientific, directly related to the product through rate, and the through rate is directly related to the product delivery time. The coordination between the pre-production department and the production department is often. Test a company's management, scientific management is not only beneficial to the delivery of products, but also the most important thing for the company's survival and development.
4. Quality control:
The process of quality control is not only to require the company to be responsible for customers' products, but also to correct its own mistakes. This link needs to pay huge costs and costs. Someone once said: "Quality control department, is a finding department, is a pay to suffer department", words are not rough. If there is a problem in the production of the product, the company is willing to spend the time and money to repair it, to "make trouble for themselves". Quality control is the conscience of a factory.
5. Details:
The electronic processing industry itself is a highly refined industry, and the intensity of detail control is directly related to the quality of products. SMT patch processing professionals all know that the invisible damage of static electricity to components is very great, and instantaneous static electricity can reach several thousand volts or even tens of thousands of volts. Invisible static damage is a huge hidden danger to the later stability of products. The static control of a patch factory is not in place, and the static elimination of the production staff is directly related to the performance of the product. Of course, the detail control of the patch processing plant is not only static electricity, but also solder paste storage, production process traceability and so on.
6. Service:
The quality of service is not only for the product process service, more is reflected in the after-sale stage can take the initiative to solve problems for customers. Do electronic products after sales. Is a major concern. Comprehensive above points, coupled with field investigation, I believe that there is no problem in choosing a satisfactory patch processing plant.