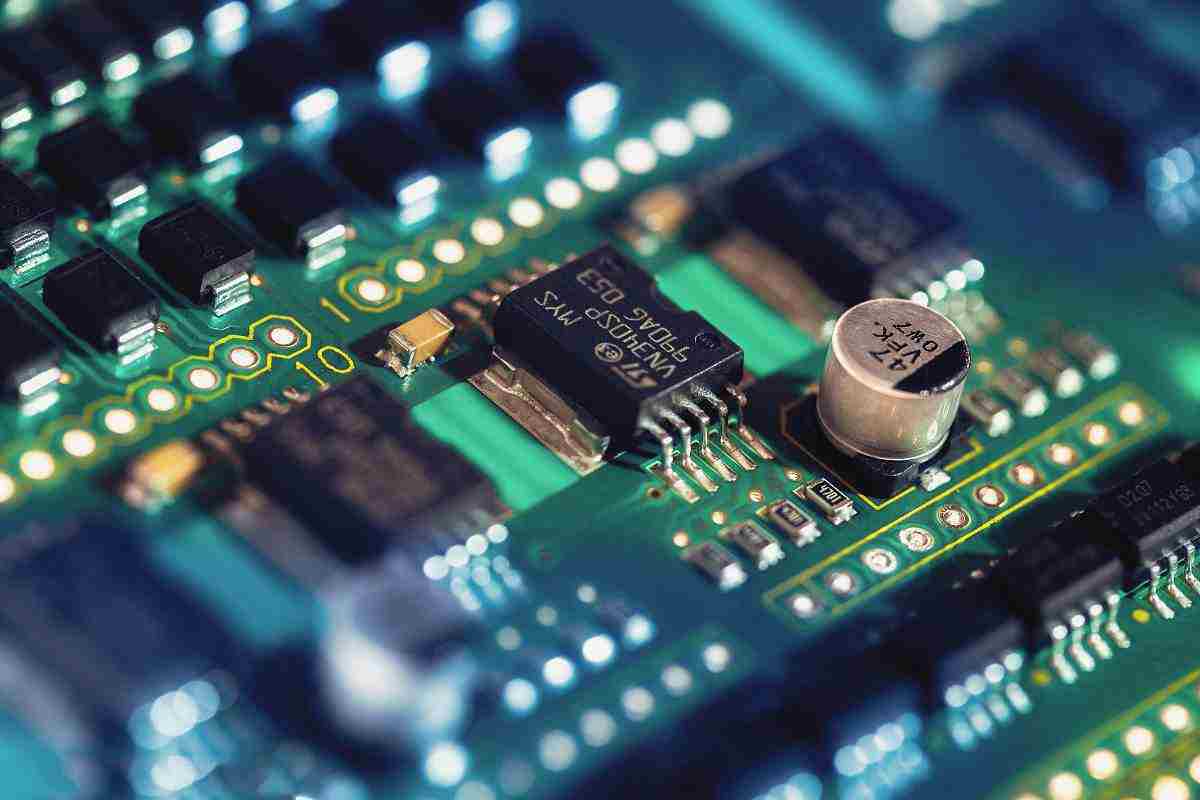
Frontal temperature gun circuit board PCBA office principle
When the infrared frontal temperature gun is aimed at and close to the distance between the measured object and the tube tested by the sensor, press the power/survey button, and maintain for many seconds, the infrared sensor plate in the infrared frontal temperature gun will collect the temperature, and is converted into electrical signals, which will be converted into digital signals, and then transmitted to the MCU through the interface. The single chip computer collects the current background temperature and carries out the corresponding temperature repayment treatment to the temperature value of the measured purpose.
Abstract: Microchip ultra-low power technology and integrated LCD choke function of low cost 8-bit PIC? SCM successfully realized, which contains power plate, button plate, infrared sensor plate, temperature sensor (plate), signal conditioning, voice plate, horn and LCD display plate composition.
Frontal temperature gun circuit board PCBA processing needs to supply information
1. Complete PCB board making files (Gerber files, positioning maps, steel mesh files) and board making requirements;
2. Complete BOM (including model, brand, package, description, etc.);
3. PCBA assembly drawing.
PS: Report the cost of PCBA function test, and provide the method of PCBA function test.
Frontal temperature gun circuit board PCBA processing process
1. Customers place orders
Customers place orders according to their actual needs of PCBA processing plants, and put forward specific requirements. And the factory will use its own experience to evaluate whether it can fulfill the order. If the manufacturer confirms that they can complete the order within the expected time, then the next two convenient will carry out consultation on the production details.
2. Customers provide means of production
After the customer votes to place the order, it will provide a series of documents and detailed registration sheets to the PCBA processing plant, such as PCB electronic files, coordinate files and BOM detailed registration sheets required for production, which must be supplied.
3. Collect and purchase raw materials
PCBA processing plant shall purchase relevant raw materials from designated suppliers according to the documents provided by customers.
4. Incoming material inspection
Before the implementation of PCBA processing, for all the raw materials to be used, the implementation of strict quality inspection, to ensure that the standard after production.
5. Produced by PCBA
In the implementation of PCBA processing time, in order to ensure the production quality, whether the patch is still burning welding production, manufacturers need to strictly control the furnace temperature.
6. PCBA test
PCBA processing plant to implement strict product testing, tested PCB board shipped to customers.
7. Packaging after sale
After the PCBA processing is completed, the products are packaged and then delivered to the customer to complete the whole PCBA processing office.
Frontal temperature gun circuit board PCBA processing several money?
Forehead temperature gun circuit board PCBA processing cost =PCB board cost +PCB test fee +PCB engineering cost (small batch suitable for use)+ component acquisition and purchase cost (local up 5%)+ SMT/DIP welding pin +PCBA testing cost + assembly engineering cost (small batch suitable for use)+ special packaging and logistics cost (such as customer demand).
Frontal temperature gun circuit board PCBA processing how long?
The time composition of PCBA processing of frontal temperature gun circuit board: meta component acquisition and purchase and PCB production +SMT patch processing +DIP plug-in processing +PCBA testing + finished product assembly.
The time details of PCBA processing of the front temperature gun circuit board: the collection and purchase of the components and PCB are generally the same as the current order, with the production demand of PCB being 3-10 days, the collection and purchase of the components being 2-15 days, and the arrival time of the components being relatively uncertain. The SMT and DIP together require 3-5 days, the PCBA test generally requires 1-3 days, and the finished product assembly takes 2-5 days.