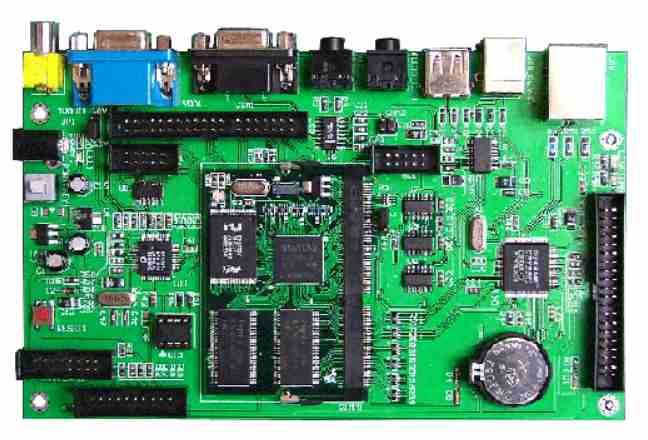
If not properly targeted maintenance and treatment, then it will easily affect the normal work of the patch machine, severe will also lead to some parts of the machine internal excessive strain or severe accidents, in order to avoid this situation again, so it is necessary to combine with scientific maintenance is the most appropriate maintenance, The following SMT manufacturer will take you to know how to maintain the SMT SMT machine and how to reduce the SMT SMT processing pollution.
1. How to reduce SMT patch processing pollution
It seems that the processing of electronic products does not produce any harmful substances, but since the country has introduced relevant environmental policies, suddenly development, the whole SMT patch processing unexpectedly has so many pollutants, and the pollution is quite serious pollution, such a situation is terrified many people, as our environment is gradually bad, Environmental protection has become the most popular keyword at this stage. If the environmental pollution has not been reduced in the whole patch processing, it will certainly become the primary target of operation.
In the whole SMT patch, the components and circuit boards are the most harmful, because the welding between the two consumes a lot of power, so it causes great harm to the environment. In order to solve this problem, at present, major enterprises have started to carry out corresponding welding of curing furnace, because the heat insulation of furnace will save energy. But the most important elements are the melting point of the solder, the length of the furnace and the number of hot zones (heating capacity). The heat declared by the device must be removed by the HVAC (heating, ventilation, and air conditioning) equipment, which consumes double the power. At the same time, the welding is directly affixed to the surface of the printed circuit board, and the electrode is welded to the same surface of the components on the pad.
In this way, the through hole on the printed board only plays the role of the circuit connecting wire, the diameter of the hole is only determined by the technological level of the metallized hole when the printed circuit board is made. There is no welding pad around the through hole, so that the wiring density of the printed circuit board is greatly improved. These two methods fundamentally eliminate the harm in the whole patch processing, reduce energy consumption and reduce the harm to the environment
2. How to maintain SMT placing machine
Of course, the large department of the situation is caused by the impact of the environment, on the other hand, also take into account the dust is not cleaned in time, the machine produces a lot of dust or oil dirt and so on will cause a very serious impact on the machine itself, the relationship between the advantages and disadvantages are affected to the service life of the machine. Therefore, if the situation is generalized, if it is not properly targeted maintenance and treatment, then it will easily affect the normal work of the patch machine, severe will also lead to some parts of the machine internal excessive strain or severe accident, in order to avoid this situation again, Therefore, it is necessary to combine the scientific maintenance method to carry out maintenance is the most appropriate, according to the quantitative and regular maintenance of the equipment, only in this way, to ensure that the SMT machine can from beginning to end to control the working function well, so as to achieve the use of the whole life.
How to maintain SMT mounter regularly:
First, take out the Nozzle. 1. Put the nozzle down first. 2. Wait until the origin. At this time take OFF the waste component box and put the "HEAD SERVO" to off. 3. Turn the head between positions 7 and 8 using the manual handle. 4. Use a mirror to place it on the platform below the head. The reason for this is to find the screws easily. 5. Loosen the screw at the bottom with the M5 trapezoidal hexagon wrench, and then remove the fixed block at the head. 6, one hand with a wrench to the top of the slide block attached to the head, the other hand is gripping the head so that it can slowly out. 7. Press the trachea interface with needle-nose pliers, pull out the trachea, and remove the sticker head. Note: the first sticker head of the trachea is more difficult to pull out, this need to pay attention to do not pull the inner side of the trachea connector loose.
Then is the head step: 1, usually in the eight position to start the installation of the sticker head. 2. Connect the sticker head to the trachea. 3. Attach the positioning hole of the sliding block to the positioning pin of the target head, and then press down to fix the sliding block. 4. Install the upper fixed block with M5 trapezoidal hexagon wrench. When tightening the screws, the two screws should be locked together. 5. After all the stickers are installed, Nozzle will be installed and adjusted centrally. 6. Prepare the materials. 7. Retest the parameters of fetching height/installation height of components. 8, prepare a piece of Panasonic SMT equipment calibration scale plate (1.6mm thick), and then use black tape to stick on the board. 9. Correct the Head Position Offset as prompted.
SMT placing machine daily maintenance method:
1, thoroughly to the machine and the surface of the electrical board generated by the dust and dirt carefully cleaned, so as to avoid dust and dirt in the internal parts of the machine, of course, the main purpose is to prevent electrical overheating to cause damage. 2. The internal gas path, solenoid valve and vacuum generating device should be thoroughly disassembled and cleaned, so that the electrical apparatus will not be blocked due to scaling. Of course, the vacuum generating device and the cylinder are all components together, so it is easy to cause component strain together.