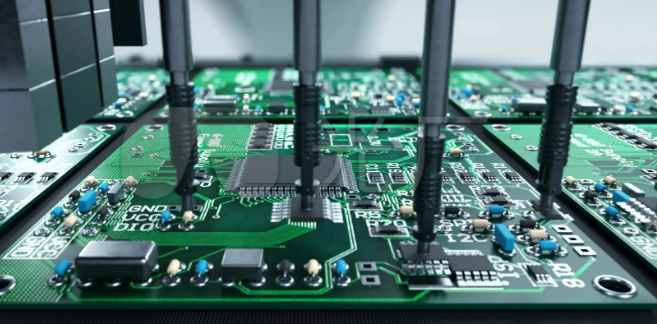
Now gasoline cars, diesel cars, new energy vehicles, electric cars, agricultural vehicles, motorcycles, racing cars, special vehicles, military vehicles, mountain bikes, special cruise cars, unmanned combat vehicles, unmanned vehicles, toy cars, etc., all need PCBA integrated circuits, then related to personal safety and the use of safety Automotive electronics quality and performance requirements are much higher than consumer PCBA integrated circuits, Now let's talk a little bit about common automotive electronics.
First of all, automotive electronics has its own industry strict quality system:
Automotive PCB manufacturers shall comply with ISO9001 regulations. PCB manufacturers are fully compliant with the ISO9001:2008 Quality management system and are committed to adhering to the strictest standards in manufacturing and assembly.
Automobile products have their particularity. In 1994, Ford, General Motors and Chrysler together established a quality control system in the automotive industry, QS9000. In the early 21st century, with the ISO9001 standard compatible, a new quality control system was published in the automotive industry, that is, ISO/IATF16949.
ISO/IATF16949 is a set of technical regulations for the global automotive industry. Based on ISO9001, and with the special requirements of the automotive industry, it focuses more on defect prevention, reducing quality fluctuations and waste easily generated in the automotive parts supply chain. When implementing ISO/IATF16949, special attention must be paid to the following 5 main tools: PPAP (Production parts Approval process), which specifies that the product should be approved by the customer before mass production or after modification; APQP (Advanced product quality Plan), stipulates that quality plan and previous quality analysis should be carried out before production, then FMEA (failure mode and impact analysis) analysis and proposed measures to prevent potential product failure, MSA (measurement system analysis) must analyze changes in measurement results to confirm measurement reliability, SPC (Statistical Process Control) master production procedures and use statistical techniques to change product quality. Therefore, the first step for PCB manufacturers to enter the automotive electronics market is to obtain the IATF16949 certificate.
Electronic integrated circuit types are now gradually integrated and intelligent from the original wiring harness:
Various types: PCB, FPC, FPC+PCB combination, ceramic PCB, 3D organic resin, etc
As a combination of mechanical and electronic devices, modern vehicle technology combines traditional technology with the latest science and technology. Different parts depend on electronic devices with different functions, resulting in the application of PCBS with different tasks.
Based on the difference of PCB substrate materials for automobile, they can be divided into inorganic ceramic based PCB and organic resin based PCB. Ceramic based PCB's leading characteristics are high heat resistance and excellent dimensional stability, suitable for engine systems in high temperature environments. However, the manufacturability of ceramic-based PCB is poor, resulting in high cost of PCB. With the development of newly developed resin substrates with higher heat resistance, resin-based PCBS are mostly used in most modern vehicles.
Follow a general rule: Apply PCBS with different performance substrate materials to different parts of the vehicle, responsible for different functions. The following table describes the types of PCBS that are compatible with some of the vehicle equipment or instruments.
Basic performance requirements
a. High reliability
Automobile reliability mainly comes from two aspects: life and environmental resistance. The former refers to the fact that normal operation can be guaranteed over the life of the service, while the latter refers to the fact that the PCB function remains the same when the environment changes.
The average lifespan of a car in the 1990s was 8-10 years, currently it is 10-12 years, which means that both automotive electronic systems and PCBS should be within this range.
During the application process, the car should withstand the effects of climate change, from extremely cold winter to hot summer, from sunlight to rain, as well as environmental changes caused by the temperature rise caused by its own driving. In other words, automotive electronic systems and PCBS must withstand a variety of environmental challenges, including temperature, humidity, rain, acid fog, vibration, electromagnetic interference and electrical surges. In addition, since PCBS are assembled inside the car, they are mainly affected by temperature and humidity.
b. Light weight and small size Light, tiny cars help save energy. Lightness comes from reducing the weight of each ingredient. For example, some metal parts are replaced by engineering plastic parts. In addition, automotive electronic equipment and PCB should be miniaturized. For example, the volume of the ECU (electronic control unit) in automotive applications was about 1200 cm 3 at the beginning of 2000, while less than 300 cm 3, through four drops. In addition, starting guns have been changed from mechanical guns connected by wires to electronic guns connected by flexible wires with PCB inside, reducing the size and weight by more than 10 times.