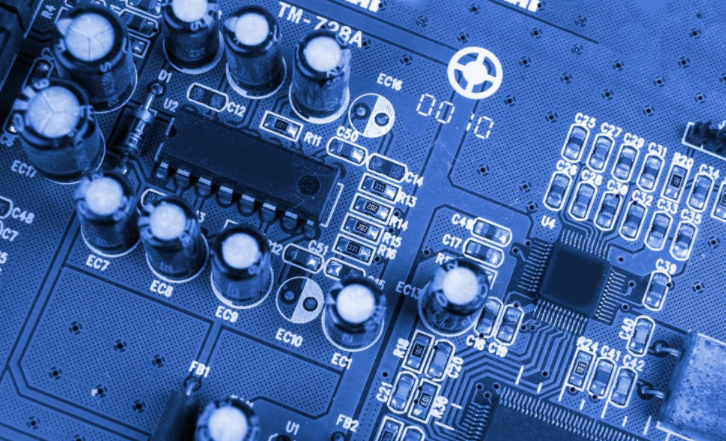
What are the types of SMT processing reflux furnace
Reflow soldering furnace is the main PCB component of welding equipment in the welding industry Welding is one of the most critical processes in Surface Mount Technology The efficiency of equipment directly affects the welding quality In particular, current lead-free soldering has high temperature characteristics, poor wettability, and a small process window Lead free reflow soldering furnace should be selected more carefully There are many types of reflux furnaces, such as hot plate reflux furnace, infrared reflux furnace, hot air reflux furnace, infrared hot air reflux furnace, gas phase reflux furnace, etc Heat the entire PCB; Laser reflow furnace and focused infrared reflow furnace are used for local heating of PCB, Hot air reflux furnace, etc
1) Reflux furnace for heating the entire PCB
Circuit board
Hot plate reflux furnace was used in the early stage of SMT Due to its low thermal efficiency, uneven heating of PCB surface and special sensitivity to PCB thickness, this reflow soldering furnace is soon replaced by other reflow furnaces Infrared reflux furnace was very popular in the 1980s When infrared radiation occurs, dark components absorb more heat than light components, and the infrared has no penetrating ability Parts blocked in the shadow area by large parts are not easy to reach the welding temperature, resulting in large temperature difference on PCB, which is unfavorable to welding Therefore, it is basically unnecessary The hot air reflux furnace has been in use since the mid-1980s In recent years, various measures, equipment structure, data, software and hardware settings, etc. have been taken in the air flow design of the hot air reflux furnace Therefore, all hot air reflow ovens have become the preferred SMT reflow oven today Infrared hot air reflux furnace refers to a heat source that has both hot air and infrared Due to the high welding temperature of lead-free welding, the reflow zone is required to improve the thermal efficiency. In retrospect, an infrared heater is added at the inlet of the hot blast furnace and at the bottom of the reflow zone, which not only solves the problem of high welding temperature, but also speeds up the heating speed and saves energy Therefore, the infrared hot blast stove has a certain utilization rate in today's lead-free welding The gas phase reflux furnace was used in the early 1970s, but due to the high cost of equipment and media, they were quickly replaced by other methods However, the gas phase reflux furnace has the advantage of accurate temperature control. The heating medium with different boiling points can meet the different welding temperatures of different products. It has high heat conversion efficiency, fast heating, and oxygen free environment. The temperature of the entire PCB is uniform, and the welding quality is good Therefore, with the development of lead-free technology, the gas phase reflow furnace has aroused people's interest again, and is used for highly reliable and difficult to heat surface mount panels
SMT wafer processing
2) Reflux furnace for locally heating PCB
The laser beam reflux furnace makes use of the good directivity and high power characteristics of the laser beam. The laser beam is concentrated in a small area in a short time through the optical system, and this welding part forms a highly concentrated local heating area. A reflux furnace. During the welding process, the base plate and the assembly body are kept at a low temperature, and the welding stress is low, so that the components and the base plate will not be damaged. However, because the equipment is very expensive, it is only used for thin pitch local welding of hot parts, valuable substrates and components. Focused infrared reflow furnace is usually applicable to the rework station for rework or partial welding. Hot air reflow furnace refers to a reflow furnace that introduces air or nitrogen into a special heating head and uses hot air flow for welding. This kind of reflow furnace needs to process nozzles of different sizes for solder joints of different sizes, and the speed is relatively slow. This is mainly used for rework or development.