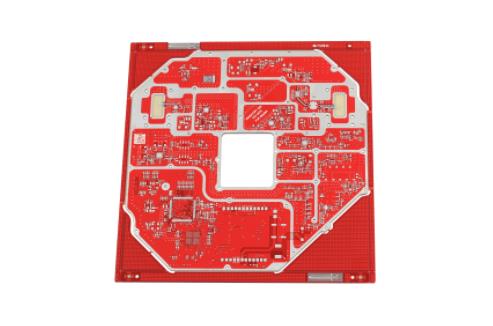
PCB factory: What is the residual copper rate of PCB board?
PCB manufacturers, PCB designers, and PCBA manufacturers will explain to you what PCB manufacturers are: what is the residual copper rate of PCB boards?
PCB factories can never avoid touching a word - PCB residual copper rate. However, some children are confused about this concept. Today, I will thoroughly explain to you what is the residual copper rate of PCB!
The concept of residual copper rate of PCB: The manufacturing process of PCB starts from the PCB "substrate" made of glass epoxy resin or similar materials. The first step of production is to draw PCB design wiring online between parts. The method is to "print" the circuit negative pole of the designed PCB on the metal conductor through negative film transfer.
This technique is to lay a thin layer of copper foil on the entire surface and eliminate the excess. If double-sided board is made, copper foil will be laid on both sides of PCB substrate. To make multilayer boards, you can "press" two double-sided boards with a special adhesive.
Next, you can drill holes and electroplate the components on the PCB board. After drilling by machines and equipment according to the drilling requirements, the inside of the hole wall must be plated (Plated - Through Hole Technology, PTH). After metal treatment inside the hole wall, the internal circuits can be connected with each other.
Before electroplating, the sundries in the hole must be removed. This is because the epoxy resin will produce some chemical changes after heating, and it will cover the internal PCB layer, so it should be cleaned first. Cleaning and electroplating will be completed in the chemical process. Next, PCB manufacturers need to cover the solder mask (solder mask ink) on the outermost PCB design wiring, so that PCB design wiring will not touch the electroplating part.
Then, various components are screen printed on the circuit board to mark the position of each component. It cannot cover any PCB design wiring or gold finger, otherwise it may reduce the solderability or the stability of current connection. In addition, if there are metal connection parts, the "golden finger" parts are usually gold-plated, so that high-quality current connection can be ensured when inserting the expansion slot. The last is testing. The PCB factory will test whether there is short circuit or open circuit in the PCB, which can be tested optically or electronically. Optical scanning is used to detect defects in each layer, while electronic testing typically uses flying pins to check all connections. Electronic tests are more accurate in detecting short or open circuits, but optical tests can more easily detect incorrect gaps between conductors.
After the completion of the circuit board substrate, the finished motherboard will assemble various sized components on the PCB substrate as required - first, use the SMT automatic placement machine to "solder" IC chips and chip components, and then manually insert some tasks that cannot be completed by the machine. These plug-in components are firmly fixed on the PCB through the wave crest/reflow soldering process to produce the motherboard. PCB manufacturers, PCB designers, and PCBA manufacturers will explain to you what PCB manufacturers are: what is the residual copper rate of PCB boards?