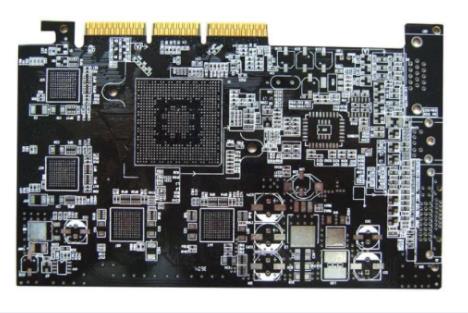
BOM is very important in PCB manufacturing
The importance of efficient production planning cannot be underestimated, because it is very helpful in optimizing production and balancing production lines Therefore, hourly demand is a powerful design data, including PCB layout data, bill of materials, usually called BoM, and product reference
Why BOM is important in PCB manufacturing
In fact, the entire SMT manufacturing process is driven by BoM. This is because the function of the PCB depends on the components listed in the BoM table. Conversely, using the correct components is critical to the functionality of the PCB. Recall that any PCB assembly order needs to be initiated using the BOM. The BoM table contains not only the list of components, but also the location of components on the printed circuit board. In turn, BoM allows procurement experts to find the right distributors for components, while finding cost-effective price points. Some components may not be available, but it provides procurement experts with the opportunity to find alternative distributors so that they can work seamlessly.
Detailed bill of materials, including specification, part description, manufacturer's name, quantity, etc. related to item number, So it's very convenient This not only guarantees the quality, but also ensures that PCB manufacturers can complete before the delivery deadline without any problems For turnkey components, the names and details of dealers and manufacturers must also be mentioned In fact, multiple dealer names can help the procurement process and ensure that time is not wasted when a particular dealer does not have ready parts
An optimized component list allows for a well - assembled plan and clear scheduling steps for the plan This in turn ensures PCB production On the other hand, the lack of an effective BoM may mean that a large number of revisions will be required, which will eventually lead to delivery delays
Circuit board
The manufacturer usually provides a sample for the sample BoM to capture all necessary information, so there is no room for ambiguity. BoM usually also includes support for explosion and implosion. Although explosions refer to display screen components, implosions help to see where specific parts are used and determine which parts are associated with any hazardous parts. Recall that layered BoM can easily study the entire structure.
When creating BoM tables, pay special attention to the following aspects:
Ideally, BoM should help manufacturers build PCB from scratch. If you have received the BoM template from the manufacturer, please ensure that you take sufficient time to complete it and provide all necessary details.
2 Point out where you can allow flexibility. Importantly, some parts may exist where you want the manufacturer to strictly adhere to the approved supplier list. Although there may be other non critical factors, they can be optimized for cost. It is better to clearly state this in the BoM table, so that you will not waste time making unnecessary revisions, or worse, you may encounter procurement errors, which may cause you to pay a heavy price.
3 Make sure that the parts are available when they are listed in the BoM. Quickly checking whether the parts are available will greatly help to ensure seamless production. If you ignore this step, you will usually make expensive design decisions at a later stage.
4 It is important to determine how many levels BoM needs and whether BoM is single level or multi-level. Generally, single-layer BoM is suitable for places seeking compact or pull manufacturing. In addition, it is recommended to use when the manufacturer does not need the overall structure of the product design. On the other hand, multi-level BoM is related. You can share a part of the BoM with the manufacturer, and you can copy subcomponents to other products. You need to determine the level of detail required for multi-level BoM tables and drill down accordingly.
5 The file changes from the prototype stage to the actually generated BoM may be changed, and these changes need to be recorded. It is better to keep a log of all changes and a history of all versions, so that everyone can synchronize not only with changes, but also with the changes that caused them.
Think of the bill of materials as your shopping list. Failure to do so may result in carelessness and costly mistakes. The rule of thumb is obviously to comprehensively assess your needs and build a BoM around them.