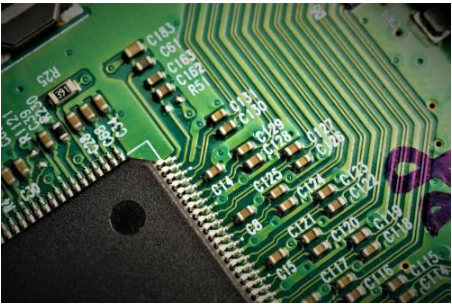
In terms of PCB product manufacturing, it is an essential part of electronic products. With the gradual increase of the production scope and output of PCB, the exhaust gas and wastewater pollutants discharged from the PCB process are also increasing, which has caused serious pollution to the ecological environment. Therefore, how to properly manage the exhaust gas discharged from the PCB production process is also increasingly important Wastewater environmental pollutants.
PCB production
There are generally four kinds of waste gas from PCB production. The first is acid waste gas, which mainly contains H2SO4, fog, SO2, HCl, NOX, HCN, etc; The second is organic waste gas, which mainly contains benzene, toluene, xylene, formaldehyde and non methane total hydrocarbons; The third type is alkaline waste gas, which mainly contains: NH3; The fourth type is lead containing waste gas, which mainly contains lead smoke. The above waste gas is characterized by high irritation and local high toxicity. Direct discharge into the atmospheric environment will certainly cause serious environmental pollution, which must be properly managed before it can be discharged. However, due to the large amount of waste gas produced by PCB plants and the fact that there are a lot of waste gas, the composition is jumbled, and in general, a variety of waste gases are mixed together, the management effect is not ideal. This paper analyzes and discusses the waste gas management of PCB factory, and explores the most effective waste gas management plan.
VOCs in PCB production
In the circuit board industry, ink printing materials containing macromolecular compounds are widely used, such as thermosetting printing materials, liquid photosensitive printing materials and photosetting printing materials. However, ink printing materials generally contain solvents, and diluents are added to obtain appropriate printing performance. The solid content of ink printing materials is generally 65% to 85%, and the solvent or diluent content is 15% to 35%. However, solvents and diluents are all composed of some components in organic compounds (VOCs, that is, volatile organic compounds) such as alcohols, ketones or benzene, ethers, etc. Solvents or diluents composed of VOCs are easy to vaporize at room temperature and heating, and the emitted air may form the ozone layer. This ozone layer is different from the stratospheric ozone layer, which protects the earth from ultraviolet radiation. It is VOCs in the lower troposphere. After photochemical action, some photochemical smog will be generated. Such smog mixed in the air has a greater negative impact on people's external organs and health. Most of the volatile organic compound waste gas comes from the circuit, solder mask, text and ink printing operations or the solvent data stored in the hot air leveling process and warehouse. For the operation process, the common disposal plan is to apply the upward suction gas gathering system to stop the collection of waste gas. However, due to the large suction force of gas gathering, the speed of solvent volatilization is often accelerated, the air flow is relatively difficult to control, and the drying speed of screen printing ink is accelerated beyond a certain limit, resulting in screen blocking. At this time, if the height of the gas collecting hood is set too high, the gas collecting effect is often not ideal. In addition, most factories and enterprises use filling or washing tower to clean volatile organic waste gas, or separate it from acid and alkali chemical waste gas treatment tower to stop treatment. Because the organic compounds contained in the organic waste gas are hydrophobic, the application of the wet disposal plan has great limitations, that is, the waste gas from the indoor operation site is collected and discharged into the atmosphere. Therefore, it is necessary to adopt a dry disposal plan. It will be more effective and reliable to use filled activated carbon for adsorption or incineration for disposal. For the process of hot air leveling, such as pasting mask film in the pressing workshop, baking after pressing, etc., there are also some thermosetting printing materials in the dry curing state in the air circulation oven, which are often not treated during drying. Generally speaking, the straight pipe is used to discharge directly to the outside, which results in the impact on part of the air environment. In the warehouse, there are usually a large number of ink printing materials, solvents and diluents. Generally, the percentage of indoor exhaust gas is high. At the same time, some solid data often contain organic exhaust gas. Generally speaking, the exhaust gas in the warehouse shall be extracted by the direct exhaust ventilator and discharged into the atmosphere without any other treatment.
pcb
2 Measures for waste gas management
In circuit board enterprises, the atmospheric pollutants generated are generally dust, sulfuric acid mist, hydrogen chloride and non methane hydrocarbon discharged during production. Generally speaking, dust is collected by jet dust collector; Sulfuric acid mist and hydrogen chloride shall be discharged only after being treated by countercurrent washing tower and reaching the qualified standard; The adsorption and disposal of non methane hydrocarbon shall be stopped with activated carbon:
(1) Jet dust collector. The jet dust collector shall use high-pressure air to stop radiation and shake off the dust in an instant. The super Venturi tube and the upper air inlet with good classification effect shall be used to prevent the reduction of dust collection performance when the dust just falls, prolong the dust fall cycle time, and greatly improve the dust collection performance and filtering speed.
(2) Counter current washing tower. The waste gas is neutralized with the washing liquid through the packed washing tower (the contact area shall be increased with the filler) to remove the harmful substances.
(3) Activated carbon adsorption. The non methane total hydrocarbon is absorbed by activated carbon, and the residual rate of non methane total hydrocarbon is less than 10% after the above methods. To ensure the normal operation and effect of the activated carbon adsorber, daily maintenance shall be strengthened and the activated carbon shall be replaced at regular intervals.
In addition, most PCB manufacturers often select local raw materials as chemicals, which may cause odor. Therefore, the transportation and storage of drugs should be sealed, the production and processing should be stopped indoors, and the ventilation system should be added to minimize the impact. Odor is often produced during sewage disposal, which affects the surrounding ecological environment. We strongly recommend the circuit board to add green belts around the sewage disposal station, strengthen the management of the conditioning tank that is prone to odor, operate the sewage disposal equipment normally, and stop the timely disposal of the sludge transported away.
3. Green management and promotion of environmental protection plan
"Green management" is a kind of enterprise management idea and management system that has been introduced from western countries to China in recent years, that is, to instill a new concept of environmental maintenance in the operation and management of the company. The environmental protection awareness of the environmental management of domestic PCB enterprises is often weak, the function of the environmental management organization is weak, the level of environmental management is relatively low, and the methods are very backward. PCB enterprises should adopt positive plans, implement green operation strategies and stop green management. First, we should change the traditional concept and establish the concept of green operation. Second, we should make every effort to carry out cleaner production. For the PCB industry, we should focus on cleaner production processes, that is, we should develop and use all kinds of plate making materials and printing inks that have low pollution emissions or are easy to prevent and treat, recycle or recycle organic solvents and special cleaning agents, develop new advanced PCB technology and instruments and equipment, and adopt waste gas and wastewater treatment processes to reduce the content of harmful substances generated from the source, This will reduce pollution. Third, actively apply for green certification and obtain green visa.