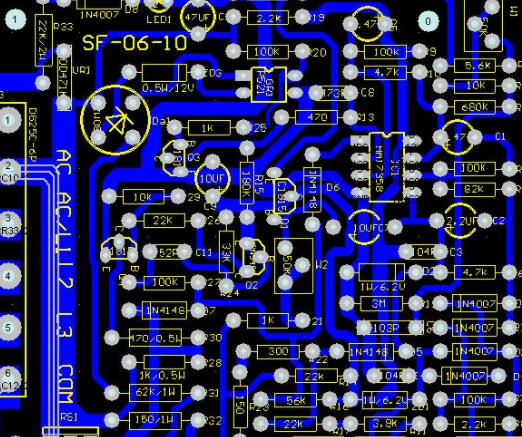
Skills for obtaining high-quality medical grade polychlorinated biphenyls
Don't know how to design and obtain high-quality PCB? printed circuit board or printed circuit board can be used in many fields You will see it in almost every industry They are also very popular in the medical industry Do you know that they are an important part of high-end medical equipment? Medical grade PCB has extremely high precision and accuracy Any medical PCB design should be easy to test and debug because there is no fault tolerance space
It is necessary to know how to design medical PCB. It helps you get the best PCB for your device.
Medical PCB design standard
Monitoring equipment and testing machines help medical manufacturers comply with standards. They produce products that exceed or at least equal to recognized industry standards. There are many potential hazards associated with the use of inferior products.
There is no room for mistakes. PCB designers and manufacturers need to follow the rules and requirements. The Commission formulates these rules and regulations.
Planning and design for easy assembly and maintenance
Circuit board
When designing PCB, many factors are indispensable. Design parameters may vary. However, this will help if you want easy assembly/disassembly and maintenance.
Service matters. It helps to achieve the output required by medical devices and machines. Accuracy and precision are essential for correct diagnosis of the testing machine). Devices that perform complex operations require high-density interconnected medical PCBs. This information is useful for testing, life support, or monitoring.
These PCBs contain a large number of connections in a small space. Many equipment professionals also prefer to combine rigid and flexible medical grade PCB. The rigid flexible PCB can be installed in a small compartment of the device. In addition, they are resistant to damage.
We must attach great importance to the medical PCB design standard
Medical electronic equipment design knowledge
Understand the normal functions and requirements of the target medical electronic equipment. Medical PCB requirements may vary by function. Medical grade PCB with higher thickness is essential for high heat dissipation. The included industry standards are a good reference point. It is helpful to correctly analyze and design medical PCB.
High quality manufacturers of medical grade PCBs comply with the following rules and regulations:
1 FCC (Federal Communications Commission): This is Title 47 of the Code of Federal Regulations.
2 FDA 21 CFR Part 807: Applicable to manufacturing companies or companies selling imported medical devices in the United States. It also includes repackaging/relabeling companies.
1 IEC 60601-1: These discuss the basic efficiency and safety parameters of medical electrical equipment.
2 IEC 61010-1: These are the basic requirements for electrical equipment. We can use it for measurement and control in medical laboratories
1 IPC 6011: Discuss the overall performance specifications of printed boards.
2 ISO 13,485 Medical Devices: Supervision and Operation of Health Management System.
3 ISO 14971 Medical Equipment: It helps manufacturers identify hazards and risks associated with medical equipment.
According to these regulations, you can design more qualified medical PCB devices.
Discard uncertain components
Designing medical PCB requires a lot of hard work. You need theoretical and practical knowledge. There is still much room for innovation.
It is best to exclude trial and error from the equation. You can't risk using medical grade PCBs. Things often happen at the same time. You can opt out of the content you are not sure about. In addition, don't forget the golden rule of electronic products to avoid open circuit.
This will help if you learn to discard uncertain components and avoid taking up space.
Strict requirements for PCB data and specifications
As far as the whole medical industry is concerned, human life is in danger. Medical equipment manufacturing is no exception. Misdiagnosis, monitoring, or support can lead to disaster. The entire industry follows strict agreements in the manufacturing process. These contracts are mandatory for medical PCB service providers. Fortunately, there are also various PCB manufacturing.
You can distinguish PCBs according to several parameters, such as:
PCB shape
Medical PCB usually has two shapes: rectangle and circle. Some manufacturers offer PCB options in custom shapes. It all depends on the customer's requirements.
Substrate used
Choose the right substrate for your design. This is very important in medical PCB design. The classification is as follows:
1. RoHS compliance.
2. High speed digital conversion.
3. High frequency RF.
4. Temperature.
Coating and cladding.
Industrial standard PCB substrates include copper core, RO4003C, domestic Shengyi PI, etc.
The high-density interconnection board or HDI board has more circuit connections. You can't find so many on traditional circuit boards. On the one hand, they contain the connection of the entire PCB (including blind spots and buried spots). The micro through-hole can reach the diameter level of less than 0.006.
There are six HDI boards available, many of which are medical grade PCBs. Some even have through holes that connect from one surface to another. They do this by connecting. In addition, HDI usually has more than two layers. But don't worry. You can connect them through vias and passive non electronic layers. With the aid of layered pair, the structure adopts coreless method.
The advantages of using HDI in medical PCB are shape efficiency and design efficiency.
TG is the abbreviation of glass transition temperature. This is a specific temperature zone. Here, the basic polymer becomes soft rubber material. Polymers used in the manufacture of circuit boards shall not catch fire. TG changes the hole and electronic properties of the transistor substrate. In addition, better TG means superior performance of medical grade PCB. You have better stability and heat resistance, moisture resistance and chemical phenomena.
High quality working environment
The working environment is critical. It helps to determine the required product standards. This is why your manufacturer needs to know the product standards. PCB designers need to know the operating position.
Temperature, pressure, humidity and air quality are all important. Each parameter can change the output of the medical device. In addition, there are more parameters.
Look for reliable manufacturers
Finding a suitable contract manufacturer seems to be an arduous task. More emphasis on accuracy than reliability, efficiency or economy. We need accurate medical equipment and equipment. Manufacturers need to provide products that comply with medical device standards and regulations.
It is wise to prepare a questionnaire for manufacturers. According to their answers, you can choose an appropriate contract manufacturer. This will help you get medical grade PCBs.
Questions to consider:
How long have you been in PCB manufacturing?
A longer time usually means a better experience. You can also expect fast delivery and industry standard follow-up.
Do you manufacture motherboards for other medical device companies?
Medical PCB is a highly specific and task oriented work. Manufacturers who have previously worked for pharmaceutical companies may perform better.
Can you avoid using fake components?
The company that tracks each relevant component may be more responsible. They will provide better products.
What quality assurance practices does the contract manufacturer follow?
Find out if the manufacturer is reliable and able to deliver.