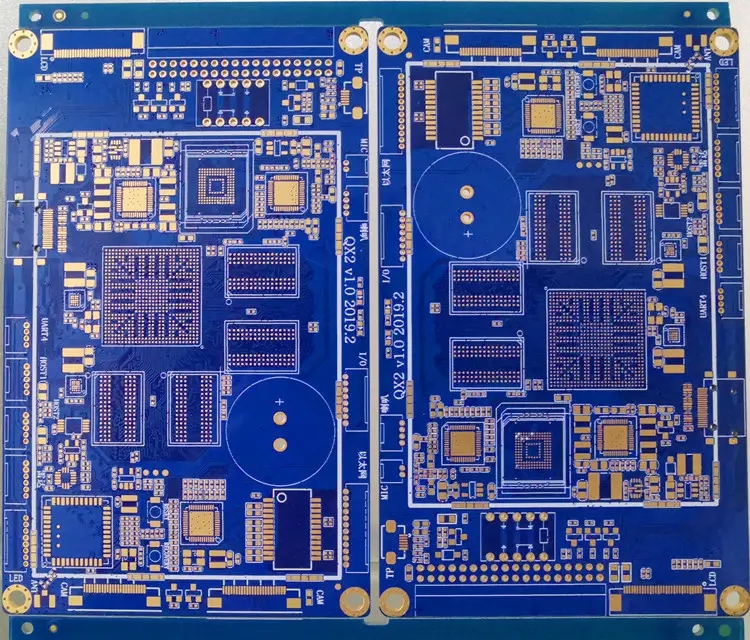
Heat dissipation skills and process control points of PCB aluminum substrate
1. Heat dissipation through PCB board itself: PCB boards widely used at present are copper clad/epoxy glass cloth substrate or phenolic resin glass cloth substrate, and there are a few paper based copper clad boards. Although these substrates have excellent electrical and processing properties, they have poor heat dissipation. As a heat dissipation way for high heating elements, they can hardly be expected to transmit heat from the resin of PCB itself, but to dissipate heat from the surface of the element to the surrounding air. However, as electronic products have entered the era of miniaturization, high-density installation and high heating assembly of components, it is not enough to rely only on the surface of components with very small surface area for heat dissipation. At the same time, due to the large use of surface mounted components such as QFP and BGA, a large amount of heat generated by the components is transferred to the PCB board. Therefore, the best way to solve the heat dissipation is to improve the heat dissipation capacity of the PCB aluminum substrate that directly contacts the heating elements, and transmit or distribute it through the PCB board.
2. For the equipment cooled by free convection air, it is better to arrange the integrated circuit (or other devices) in the longitudinal or transverse way.
3. Use a reasonable routing design to achieve heat dissipation: because the resin in the plate has poor thermal conductivity, and the copper foil lines and holes are good conductors of heat, improving the copper foil residual rate and increasing the thermal conductivity holes are the main means of heat dissipation.
4. Heat sink and heat conduction plate for high heating components: When there are a few components in the PCB with large heating capacity (less than 3), heat sink or heat conduction tube can be added to the heating components. When the temperature cannot be reduced, heat sink with fan can be used to enhance the heat dissipation effect. When there are many heating devices (more than 3), large heat dissipation cover (plate) can be used. It is a special radiator customized according to the position and height of the heating devices on the PCB board, or different component high and low positions can be picked out on a large flat panel radiator. Buckle the heat shield onto the element surface as a whole, and contact each element to dissipate heat. However, the heat dissipation effect is not good due to the low consistency of components during assembly and welding. Usually, a soft thermal phase change heat conduction pad is added on the surface of the components to improve the heat dissipation effect.
What are the key points of process control for aluminum substrate?
1. Making negative film: due to the existence of side corrosion, the line accuracy of the drawing must be sufficient, so certain process compensation must be made when photo drawing negative film, and the process compensation value must be determined by measuring the side corrosion value of different thicknesses of Cu. The negative is negative.
2. Material preparation: purchase 300 as much as possible × The dielectric constant of the plate with fixed size of 300mm and protective film on Al and Cu surfaces is the same as that in the drawing.
3. Graphic preparation: It is recommended to use chemical micro etching to treat the Cu surface, with the best effect. After the Cu surface is treated, the wet film shall be screen printed immediately after drying to prevent oxidation. After development, use a graduated magnifying glass to measure whether the line width and gap meet the requirements of the drawing, and ensure that the lines are smooth without sawtooth. If the thickness of the UFO aluminum substrate is greater than 4mm, it is recommended to remove the upper drive roller of the developer to prevent rework caused by jamming.
4. Etching: use acidic CuCl HCl solution for corrosion. Adjust the solution with the test plate, etch the Al substrate when the etching effect is optimal, and turn the pattern side down to reduce the amount of side etching.
5. Surface treatment (Sn immersion): After the etching process is completed, do not rush to remove the film. Prepare the Sn immersion solution immediately, i.e. remove the film, i.e. soak in Sn, with the best effect.
6. Machining: CNC milling machine shall be used to process PTFE and aluminum substrate separately during contour processing, so as to avoid delamination caused by different thermal conductivity and deformation of the two. The graphic face shall also be upward to reduce delamination and burrs.
PCB manufacturers, PCB designers and PCBA processors will explain the heat dissipation techniques and process control points of PCB aluminum substrate.