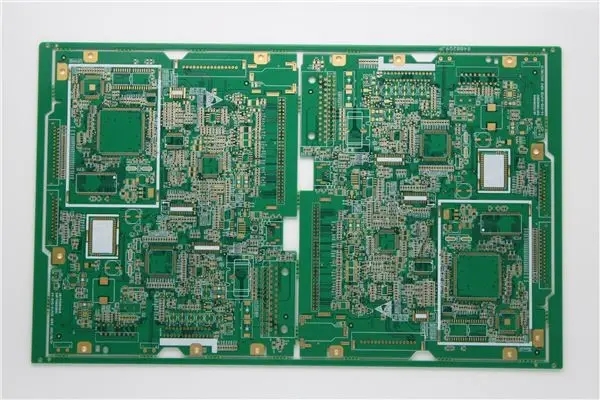
Circuit board manufacturer explains chip deflection and its solution
PCB manufacturers, PCB designers and PCBA manufacturers will explain the chip deflection and its solutions
Due to the continuous growth of flip chip in the next generation of products, it is necessary to avoid chip deflection. Now let's take a look at how to solve the chip deflection problem
1、 Question
In many areas of the electronic industry, flip chip is integrated into new products, showing the law of growth. Therefore, we must understand many variables related to design, materials, processes and equipment to ensure the successful implementation and survival of this technology. For example, the processing and mounting of bare chips create new challenges that are not usually encountered in standard surface mount assemblies. A customer recently asked, "We have seen an increase in the number of skewed chips in our flip chip assembly process - what may cause this problem, and how can we correct it?"
2、 Problem solving
Chip skew is a process problem that may occasionally occur when dealing with bare chips. Some factors in flip chip assembly process may cause such mounting defects, including improper equipment settings, incorrect process parameters and incompatible assembly materials. In addition, the mounting accuracy is affected not only by the chip mounting process, but also by other manufacturing processes, such as flux loading, board transfer and solder reflow. It is often a challenge for manufacturing engineers to quickly determine and eliminate the variables that cause this special deflection problem.
For the special case of chip deflection mentioned above, we follow a series of steps to find the cause of the problem and provide a solution. When working with the customer, the initial focus is on determining which process step is causing the problem. Process inspection shall be conducted on upstream and downstream processes, mainly including reflow of flux and solder, to determine the potential impact of each process. After drawing the conclusion that the process and equipment conditions are within the specification range and ensuring that all independent and dependent variables are correct, we observed the chip mounting in the customer's factory. The observation shows that different types of nozzles have a significant deflection effect on various chip batch numbers.
Then, the mounting process is simulated on a surface mounting line, and the variables and conditions are the same as those used by the customer's factory. Use the customer's actual products and various chip batch numbers. During the mounting process, high-speed photography is performed when two nozzle models are used. The film shows that when the chip is released, the chip also adheres to the B-type nozzle (rubber), but when the A-type nozzle is used, there is no chip adhesion. No flux is used during mounting to highlight the adhesion of the chip to the nozzle. The plate is rigidly supported to reduce the elastic effect of the plate. Information was also collected to determine the interaction of each nozzle type with various chip lot numbers.
The contamination on the chip and nozzle, as well as the surface finish of the chip and nozzle, were thoroughly investigated. The characteristics of the samples of the nozzle type (old and new) and each chip batch number were analyzed, including solvent extraction, scanning electron microscopy (SEM) and Fourier transform infrared spectroscopy (FTIR). The analysis showed that the back concave appeared on the failed chip batch number (about 30mm in diameter and 8mm in depth). Organic compounds are also found - mainly adhesive and free hydroxide groups. This can lead to chip adhesion problems, either due to excessive adhesion or due to local effects of vacuum. In addition, FTIR analysis revealed that there were compound groups on the old nozzles (both type A and type B), indicating that there were free hydroxide compound groups, which may be found in organic acids, alcohol and solvents. The possible cause of chip adhesion is the excessive adhesion between the chip and the suction nozzle due to the interaction or reaction of hydrogen and oxygen compounds. A new suction nozzle was installed on the mounting machine, and the deflection problem was immediately corrected.
In this special case, the solution to the chip deflection problem is only a simple correction. The surface condition of the nozzle is critical for obtaining proper adhesion and separation between the nozzle and the chip. Proper nozzle surface cleaning method is critical to ensure the performance of the nozzle (and mounting).
PCB manufacturers, PCB designers and PCBA manufacturers will explain the chip deflection and its solutions.