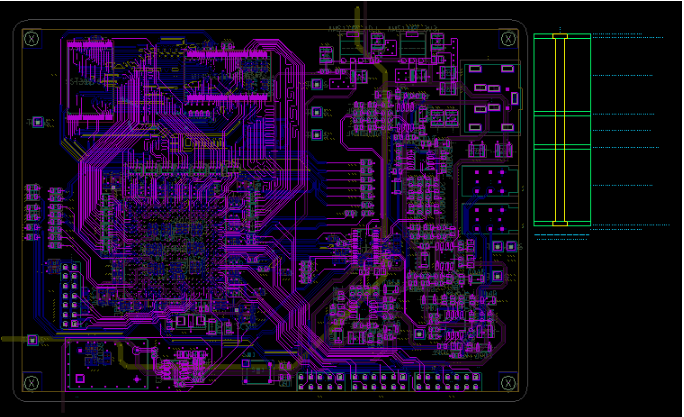
1. A headache in PCB industry, customers often design VIA holes with green oil and no windows on both sides, or some windows with green oil or windows on one side. How should we deal with this design
Answer: What surface treatment should we first consider for this PCB? If it is HALS, we must avoid the single-sided plug hole process, because the depth of the single-sided plug hole is low, it is easy to cause solder bead plugging during tin spraying, and the solder bead plugging has a great impact on the appearance.
In case of other surface treatment, such as gold, OSP, silver, etc., single side is acceptable. After considering the above factors, we will look at the customer's green oil window design. If the window is partially opened, we should try to avoid using green oil to cover the hole edge, and allow green oil to enter the hole, because this way is also easy to cause solder beads.
To sum up the above two situations, the best treatment is to allow 1-2
MIL tin coils on the side of double sided plug holes or green oil cover holes, which is most popular with PCB manufacturers. Of course, the oil plugging here is for ordinary photographic oil, not thermosetting oil.
2. When the green oil window is opened, it is generally stipulated that the green oil cannot enter the through hole. However, the green oil plug hole requires the green oil to enter the hole. Have questions about this?
Answer: The green oil is used to open windows (mainly for the plug-in holes, mounting holes, test points, etc. of surface mounted pads and devices. At this time, the green oil cannot cover PCB pads and holes, because the green oil is a non-conductive substance. If it is inserted into the hole or disk, it will cause poor welding, poor detectability, etc.)
Resin plug hole
A. If you want to get a PCB board, all via pad surfaces and holes are sprayed with tin (or other surface processes) like other device pads. When you process data, you need to open a window for solder blocking. The via has good conductivity.
B. If the density of your PCB board is very high, it is better to require a plug hole for vias, that is, fill the vias arm with green oil and seal the surface. This will reduce short circuit during welding.
C. Of course, the silk screen should be strict. If it is pressed onto the plate to be welded, the reliability cannot be guaranteed during PCB welding.
3. What is the standard of BGA plug hole? Sometimes a plug hole is required, sometimes a plug hole is not required. I don't know when to plug it, but when not to plug it, thank you
Answer: For vias close to the pad or densely wired vias (less than 0.4mm in size, usually 0.3/0.25mm), plug holes are required to prevent short circuit. Through hole at the bottom of BGA: if it is not a test point, it needs to be plugged to prevent short circuit and tin bead. If you want to use it as a test point, you can open a window on the bot side, open a small window on the top side or cover it with green oil. (When the pitch of bga is large, it is recommended to open a small window at the test point. When the pitch is less than 1mm, it is recommended to cover it with green oil.)