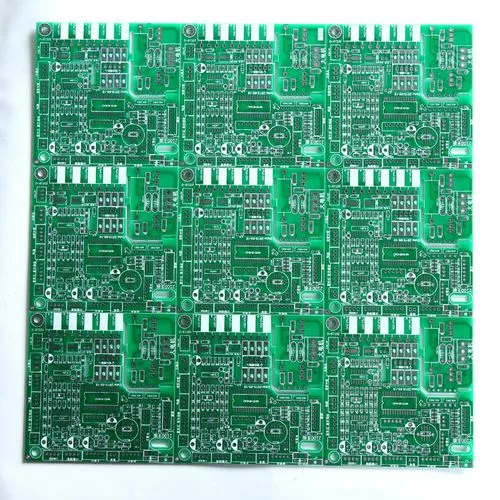
Gas phase reflow welding is also called condensation heat welding. VPS refers to the welding equipment that uses the latent heat released during the gasification of carbon fluoride liquid as the heat medium to provide heat for welding. The first vapor phase reflux thick film circuit.
1、 The principle of vapor phase reflow welding is that the liquid containing carbon fluoride can be heated to the boiling point (about 215 ℃) and vaporized to produce different vapors. As a heat transfer technology medium, the PCB circuit board design for chip processing is put into the steam furnace, and the welding is studied by analyzing the heat (latent heat) in the condensation steam transfer process.
In the vapor phase reflux furnace, when the vaporization temperature is reached, the welding zone (vapor liquid fluorocarbon layer) becomes high-density, replacing saturated steam, air and water. In the place full of steam, the temperature is the same as the boiling point of the liquid in the gasification technology stage. The peak temperature of welding is that the temperature of carbon fluoride liquid is very uniform when the boiling temperature at normal pressure is 215 ℃. VPS welding environment is neutral, it does not need to weld large ceramic BGA, SMT lead-free solder uses nitrogen, which has great advantages.
SMT chip processing
SMT chip reflow soldering
2、 A new type of gas phase reflow welding
With the development of lead-free SMT, students have recently developed a new method based on the principle of jet system on the basis of traditional gas phase welding equipment. This teaching method research can more accurately manage and control the amount of welding medium steam, and at the same time reflow the assembly plate in the closed chamber. The reflow temperature and the degree of freedom to control the curve are higher than the traditional method of gas phase welding system. When welding with molten solder, vacuum can eliminate the formation of bubbles, improve reliability, and reduce the processing cost of PCBA.
The equipment can adopt the advanced spray gas phase welding working mode, and spray a certain amount of emotional medium fluorine oil into the treatment chamber according to the requirements of different environmental temperature change curves of the enterprise. When the liquid contacts the inner surface of the treatment chamber, the liquid evaporates rapidly to form vapor mist. It is possible to control the heat energy carried by the vapor mist by controlling the amount of fluid entering, and it can be very accurate and flexible to control the desired temperature distribution. Compared with the traditional reflow soldering, it has the advantages of high reliability, no voids in the solder joints, low defect rate, etc., and is suitable for the high reliability and safety requirements of China's military PCB product technology.
How to reduce the throwing rate in SMT chip processing
SMT dumping is also commonly referred to as dumping, which means that the material is thrown out when the suction nozzle of the placement machine moves to the PCB placement position after taking the material from the material tray. Generally, this problem is caused by insufficient suction nozzle pressure, damaged suction cups or dirt on suction cups. How to reduce the throwing rate is a problem worthy of attention for most SMT processing plants, because throwing will affect the production efficiency and further affect the production cost.
SMT patch
The throwing rate in SMT chip processing is actually that the SMT machine does not carry out normal chip processing after absorbing the materials during the chip processing, but throws the materials into the throwing box or other places or directly does not absorb the materials. Throwing material will cause excessive material loss, thus prolonging production time and reducing production efficiency. The production efficiency is directly related to the production cost, so each SMT processing plant will seriously reduce the dumping rate.
Generally speaking, the main reasons for high dumping rate are as follows:
1、 The deformation, blockage and damage of the suction nozzle will cause insufficient air pressure and leakage, which will lead to the inability to suck materials, incorrect reclaiming or the failure to identify and throw materials. This problem can be solved by replacing the suction nozzle in time.
2、 Picking position If the picking position is not at the center of the material, or if the picking height is not correct, the deviation and incorrect picking will be discarded by the identification system as invalid material. Therefore, the picking position should be adjusted during smt chip processing.
3、 Pollutant interference recognition on the vision of recognition system and laser lens, improper selection of recognition light source, insufficient intensity and gray scale, damage of recognition system, etc. will cause the increase of throwing rate. This problem can be solved by cleaning and wiping the surface of the recognition system, adjusting the intensity and grayscale, and repairing or replacing the recognition system.
4、 If the vacuum air pressure is insufficient, it may cause the vacuum gas pipe channel to be not smooth, which may lead to unsuccessful reclaiming or falling off during the decal removal after picking up. Therefore, if there is any leakage during SMT patch processing, it needs to be repaired in time, the blockage should be cleaned, and the air pressure should be adjusted as required.