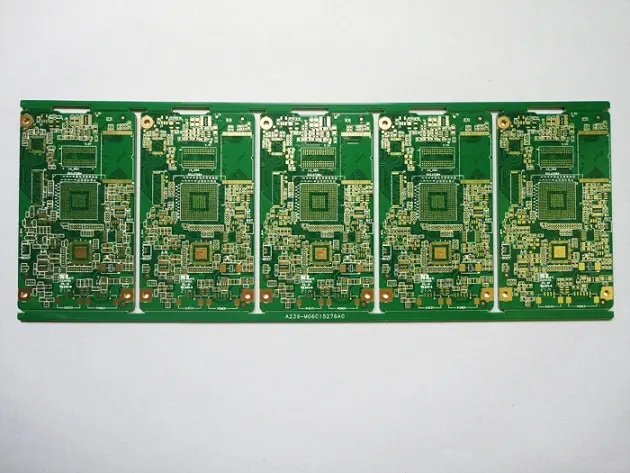
Circuit board factory: temperature zone division and furnace temperature of reflow soldering furnace
In the process of PCBA processing, reflow welding is an important processing link with high process difficulty. It is a group of welding processes. All electronic components on the PCB board are completed by overall heating and one-time welding. This process requires experienced operators to control the furnace temperature curve of reflow welding, ensure the welding quality, and ensure the quality and reliability of the final product. How can we set the furnace temperature curve of reflow soldering furnace and obtain excellent welding quality? There are many literatures and materials on the network, but most of them are difficult to understand. Next, we will briefly introduce how to set the furnace temperature curve of reflow soldering. backflow
In the process of PCBA processing, reflow welding is an important processing link with high process difficulty. It is a group of welding processes. All electronic components on the PCB board are completed by overall heating and one-time welding. This process requires experienced operators to control the furnace temperature curve of reflow welding, ensure the welding quality, and ensure the quality and reliability of the final product. How can we set the furnace temperature curve of reflow soldering furnace and obtain excellent welding quality? There are many literatures and materials on the network, but most of them are difficult to understand. Next, we will briefly introduce how to set the furnace temperature curve of reflow soldering.
The reflow soldering furnace has four zones, which are divided into preheating zone, constant temperature zone, tin melting zone and cooling zone. Most solder pastes can operate in these temperature zones. In order to deepen the understanding of the ideal temperature curve, the temperature, residence time and changes of solder pastes in each zone are introduced as follows:
1、 Preheating zone
The purpose of preheating area is to heat PCB board to achieve preheating effect, so that it can be fused with solder paste. But at this time, the heating rate should be controlled within a suitable range to avoid thermal shock and damage to circuit boards and components. The temperature rise slope of the preheating zone shall be less than 3 ℃/sec, and the set temperature shall be between room temperature and 130 ℃. The residence time is calculated as follows: if the ambient temperature is 25 ℃, (150-25)/3 is 42s if the heating rate is 3 ℃/sec, and (150-25)/1.5 is 85s if the heating rate is 1.5 ℃/s. It is usually the best to adjust the time according to the difference degree of element size to regulate the heating rate below 2 ℃/s.
2、 Constant temperature zone
The main purpose of the constant temperature zone is to stabilize the temperature of the components on the PCB and minimize the temperature difference. We hope that the temperature of large and small components can be balanced as much as possible in this area, and the flux in the solder paste can be fully volatilized. It is worth noting that in this section, the components on the circuit board should have the same temperature to ensure that they will not have poor soldering when entering the reflow section. The set temperature of the constant temperature zone is 130 ℃~160 ℃, and the constant temperature time is 60~120s.
3、 Reflow zone
The temperature in this range is the highest, which makes the temperature of components rise to the peak temperature. In reflow soldering, the peak welding temperature is different depending on the solder paste used. Generally, we recommend using the melting point temperature of the solder paste temperature plus 20~40 ℃. The peak temperature is 210 ℃~230 ℃, and the time should not be too long to prevent adverse effects on PCB. The temperature rise rate in the reflux zone shall be controlled at 2.5-3 ℃/s, and the peak temperature shall be reached within 25s-30s generally. A trick here is that the tin melting temperature is above 183 ℃, and the tin melting time can be divided into two parts, one is 60~90s above 183 ℃, the other is 20~60s above 200 ℃, and the peak temperature is 210 ℃~230 ℃.
4、 Cooling area
The lead tin powder in the solder paste in this section has melted and fully wetted the connected surface, so it should be cooled as quickly as possible, which is helpful to get bright solder joints with good shape and will not produce rough solder joints. The cooling rate of the cooling section is generally 3~4 ℃/s, which can be cooled to 75 ℃, and the cooling slope is less than 4 ℃/s.
Of course, in mass production, the actual working curve of each PCB product should be obtained through repeated adjustment according to the size of SMA, the number of components and the type of components. From the time perspective, the entire reflow time is 175sec-295sec, that is, about 3-5 minutes (excluding the time before entering the first temperature zone).