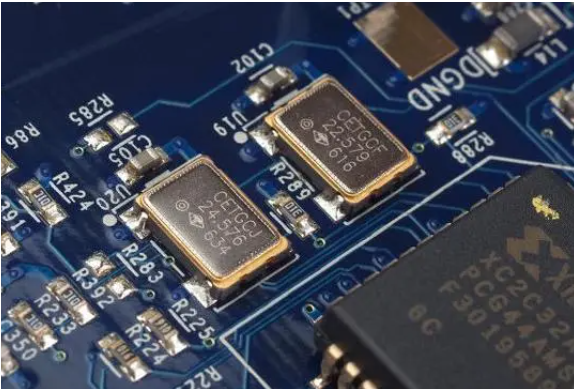
Some sample PCB factories give a few fixed laminated structures, and then let the customer calculate the impedance according to his lamination... To be honest, I really want to be rude to these plate factories! If you can't do it, you can't do it! How can you fool people? You are so good at it!
To do well in the impedance plate, the following three basic points must be done well:
1: Engineering data processing.
For a PCB manufacturer that is truly a multi layer board manufacturer, as a customer, you don't need to calculate the impedance by yourself. You just need to mark the single end and differential line that need to control the impedance and put forward the impedance value requirements. The board manufacturer will help you calculate the impedance according to the parameters of its own PCB factory.
1. The material parameters of each factory are different.
2. Each factory has different line compensation and etching and electroplating solutions.
3. The inspection standards of each factory are different.
The above three points are doomed. It is more reliable for you to assign impedance to PCB manufacturers! For this point, some sample factories ask customers to adjust the impedance and directly go offline, which is totally irresponsible. This may be OK for single ended impedance and individual differential impedance, but it is not reliable for multiple groups of impedance such as DDR!
2: PCB circuit accuracy error control.
The line accuracy is not well controlled, and the impedance deviation is the most common problem in many factories! To control the line accuracy, two points must be met:
1. Good line exposure machine. At present, powerful PCB manufacturers use LDI exposure machine. A good LDI exposure machine, more than 2 million. This is a threshold for small factories to make low-end boards.
2. Vacuum etching machine. The alignment accuracy of line exposure is not enough. When etching with sulfuric acid solution is needed, the line should be fully and accurately etched. This requires a vacuum etcher, especially for 3-4mil circuits. However, while the vacuum etching machine meets the requirements of precision and full etching, it has one characteristic: slow etching efficiency. Low capacity! This is taboo for conventional Allegro!
3: Pressing.
Pressing is very important for PCB impedance boards, especially high multilayer impedance boards! Because the PP dielectric layer will show the glue flow state under high temperature pressing, at this time, for the pressing temperature, PCB process, calibration control is very critical! Otherwise, the thickness deviation of finished dielectric layer will seriously affect the accuracy of impedance value! Therefore, to judge whether a PCB factory can do well in impedance board, it is more important to pay attention to whether they have their own pressing equipment.