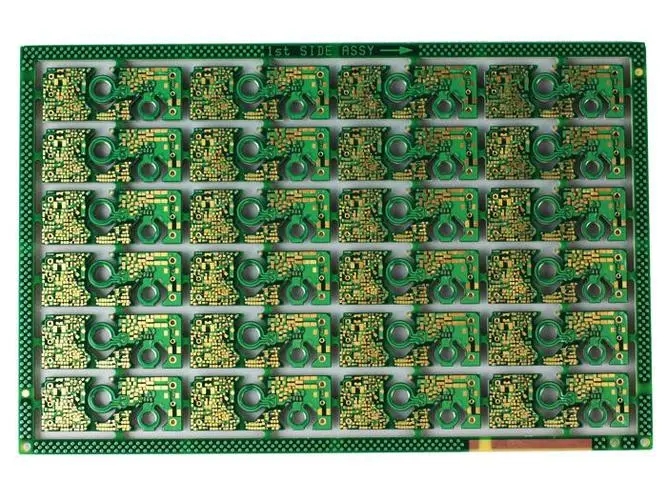
Several inspection methods for defects of BGA solder ball welding
In general, when we check the solder quality of BGA solder balls, if there are shortcomings in bridging/short circuit, we can usually find them by using X-ray equipment; However, if you want to check whether the solder ball is empty or cracked, it will be more complicated.
Basically, there are three ways to check the weldability of BGA, including X-Ray, penetrant dye test and sectioning. In any case, before you want to analyze the weldability of BGA, it is recommended that you use X-Ray to check to see if you can see any problems. After all, this is a non-destructive inspection. Only when X-Ray cannot determine the problem, can you continue to use the latter two destruction methods.
1、 Check BGA weldability with X-Ray
General X-ray inspection machines can only view two-dimensional (2D) images, but it is difficult to see whether there are empty solder joints or solder ball cracks in two-dimensional (2D) images, because the image can only see the shape of the whole solder ball, but if there are too many or too large bubbles in the solder ball, it is very likely to cause the problem of fracture. In addition, if the outer diameter of the solder ball is larger or smaller than other adjacent solder balls, it is also possible to cause empty solder joints.
In addition, recently, there are new X-Ray inspection machines that can produce stereoscopic image results similar to those of hospital computed tomography scanning. They can present stereoscopic images and check whether there are defects in soldering. However, because the cost of this machine is too expensive, it is impossible for ordinary factories to purchase such equipment. A more feasible way is to rent this kind of X-Ray machine to an external laboratory for preliminary inspection. If this kind of inspection can detect the problem of BGA defect, it is unnecessary to use the subsequent destructive test.
2、 Red Dye Penetration Test
This is a destructive test. It is usually used for defective boards that cannot be disassembled in all non-destructive tests. Because if the destructive test continues, this board and BGA will be scrapped, and even the original evidence may be destroyed. Generally speaking, the red dye test can see the soldering of all tin balls under a whole BGA.
Its theory is to fill the bottom of the whole BGA with obvious red liquid, make use of the property that the red liquid can penetrate into all small cracks, and then when the BGA is removed from the circuit board, check the distribution of the red liquid and the results of the solder ball. When judging, it is necessary to simultaneously check how much red liquid remains in the solder pad on the circuit board and the solder ball on the BGA. The recording method is usually a drawing with a table, These tables will correspond to the position of BGA solder balls, and then record the residue of red liquid on each solder ball.
3、 Check BGA solderability by slicing circuit board
This method is also a destructive experiment, and it is more laborious than the red dye test. It usually requires a more accurate pre job analysis. Use the electrical test to check that the tin ball may have problems, and then do the slicing. You can temporarily imagine that slicing is to take a knife to cut down from the place you think there is a problem. The section structure of the tin ball can be checked in detail at the cut place, Even the lines and nodes on the circuit board can be seen. Sometimes the BGA problem does not come from the solder ball soldering of the BGA, but from the circuit board. You can also analyze the problem with the circuit board by using slicing.
However, if the mechanical action of the slice is too big or too fast, it is easy to damage the original BGA and the wiring connection structure on the circuit board, so you must be very careful, grind the section you want to check slowly bit by bit, and remove dust and special development at the grinding place, otherwise some phenomena are not easy to be detected by the microscope, because it is time-consuming and labor consuming, Therefore, it is generally sent to the laboratory outside the pcb factory for slicing.