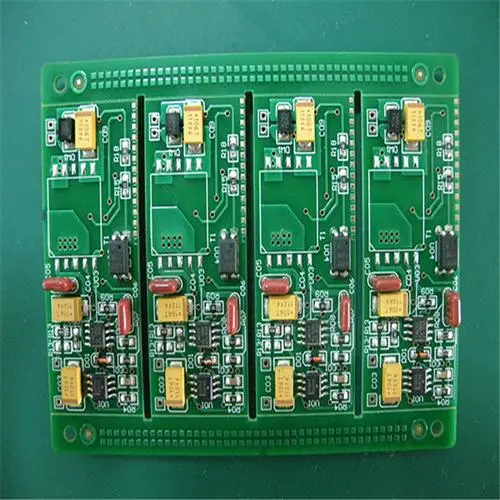
In the process of pcb board design, the possible problems of the base plate mainly include the following
1、 Signs of various PCB welding problems: there are blasting holes in cold welded joints or tin welded joints.
Inspection method: always analyze the hole before and after immersion welding to find out where the copper is stressed. In addition, check the feeding of raw materials.
Possible causes:
Bursting holes or cold welding spots can be seen after welding operation. In many cases, poor copper plating will expand during the welding operation, resulting in holes or orifices on the metallized hole wall. If this is generated during wet processing, the absorbed volatiles are covered by the coating and then discharged under the heating of immersion welding, which will produce a nozzle or orifice.
Solution:
Try to eliminate the pressure of copper. The expansion of the laminate in the Z-axis or thickness direction is usually related to the material. It can promote the fracture of metallized holes. Work with laminated PCB manufacturers to obtain recommendations for materials with low Z-axis expansion.
Second, symptom of adhesive strength problem: PCB pad and wire are separated during immersion welding operation.
Inspection method: During incoming inspection, fully test and carefully control all wet processing processes.
Possible causes:
1. Separation of pads or wires during processing may be caused by electroplating solutions, solvent etching, or copper stress during electroplating operations.
2. Punching, drilling, or punching will partially separate the pad, which becomes apparent during hole metallization operations.
3. During wave welding or manual welding operation, the falling off of welding pad or wire is usually caused by improper welding process or high temperature. Sometimes, pads or leads will separate due to poor adhesion or low thermal peel strength of the laminate.
4. Sometimes the pcb board design wiring will cause the bonding pad or wire to be separated at the same position.
5. During the welding operation, the absorbed heat retained by the component will cause the bonding pad to separate.
Solution:
1. Provide the laminate manufacturer with a complete list of solvents and solutions used, including processing time and temperature for each step. The copper stress and overheating impact during electroplating were analyzed.
2. Carefully observe the mechanical processing method of pushing and storage. Periodic analysis of metallized holes can control this problem.
3. Because of loose requirements for all operators, most pads or wires are separated. Separation also occurs when the temperature test of the solder pool fails or the dwell time in the solder pool is prolonged. In manual welding and finishing operations, pad separation may be caused by the use of electric ferrochrome with inappropriate wattage and the failure to carry out professional process training. At present, some laminated PCB manufacturers have manufactured laminates with high peel strength at high temperatures for strict welding.
4. If the disconnection caused by the design wiring of the PCB board occurs at the same position of each circuit board; Then the printed circuit board must be redesigned. Usually, this happens where thick copper foil or wires are at right angles. Sometimes, this phenomenon also occurs on long wires. This is because the coefficient of thermal expansion is different.
5. Remove heavy components from the entire pcb board design, or install them after welding operations. Generally, low wattage electric soldering iron is used for careful welding, which is shorter than immersion welding of components.
3. Symptoms of excessive size change: the size of the base plate exceeds the tolerance or cannot be aligned after processing or welding.
Inspection method: comprehensive quality control shall be carried out during processing.
Possible causes:
1. The structure and texture direction of paper-based materials are ignored, and the positive expansion is about half of the horizontal expansion. In addition, the substrate cannot be restored to its original size after cooling.
2. If the local stress in the laminated PCB is not released, irregular size changes may occur during processing.
Solution:
1. Instruct all production personnel to cut the plates along the same structural texture direction. If the size change exceeds the allowable range, the base can be considered.
2. Please contact the laminate PCB manufacturer to learn how to reduce the material pressure before processing.