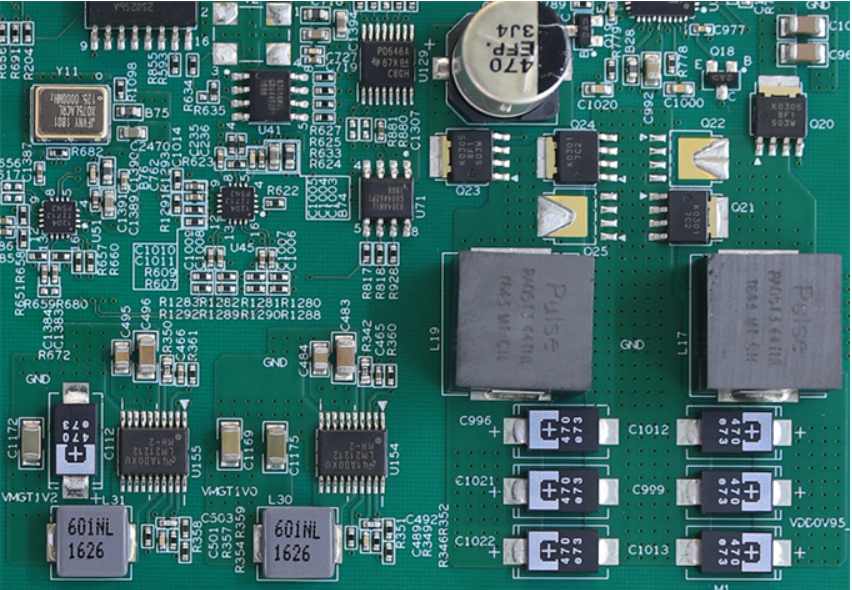
At first glance, no matter what the internal quality of PCB is, it is almost the same on the surface. It is through the surface that we see the differences, which are critical to the durability and functionality of PCB throughout its life.
Whether in the manufacturing and assembly process or in actual use, PCB must have reliable performance, which is crucial. In addition to the related costs, the defects in the assembly process may be brought into the final product by the PCB, which may cause faults in the actual use process, leading to claims. Therefore, from this point of view, it is no exaggeration to say that the cost of a high-quality PCB is negligible.
In all subdivided PCB industries, especially in the markets where products in key application fields are produced, the consequences of such failures are unimaginable.
These aspects should be kept in mind when comparing PCB prices. Although the initial cost of reliable, guaranteed and long-life products is high, they are still worth it in the long run.
14 Most Important Features of High Reliability PCB
1. 25 microns copper thickness of hole wall
benefit
Increased reliability, including improved expansion resistance of the z-axis.
Risk of not doing so
Electrical connectivity problems during hole blowing or degassing, assembly (inner layer separation, hole wall fracture), or failure may occur under load conditions during actual use. IPCClass2 (the standard adopted by most factories) requires 20% less copper plating.
2. No welding repair or open circuit repair for PCB
benefit
The perfect circuit ensures reliability and safety without maintenance and risk
Risk of not doing so
If it is not repaired properly, the circuit board will open. Even if the repair is' proper ', there is a risk of failure under load conditions (vibration, etc.), which may lead to failure in actual use.
3. Cleanliness requirements beyond IPC specifications
benefit
Improving PCB cleanliness can improve reliability.
Risk of not doing so
The accumulation of residues and solder on the circuit board will bring risks to the solder mask, and the ionic residues will lead to the risk of corrosion and pollution on the welding surface, which may lead to reliability problems (poor solder joints/electrical failures), and ultimately increase the probability of actual failures.
4. Strictly control the service life of each surface treatment
benefit
Soldering performance, reliability, and reducing the risk of moisture intrusion
Risk of not doing so
As the surface treatment of the old circuit board will change metallographically, solderability may occur, while moisture intrusion may lead to delamination, separation of inner layer and hole wall (open circuit) and other problems during assembly and/or actual use.
5. Use internationally known base materials – do not use "local" or unknown brands
benefit
Improve reliability and known performance
Risk of not doing so
Poor mechanical performance means that the circuit board cannot perform as expected under assembly conditions. For example, high expansion performance will lead to delamination, open circuit and warping problems. The weakening of electrical characteristics can lead to poor impedance performance.
6. The tolerance of copper clad plate shall meet the requirements of IPC4101ClassB/L
benefit
Strictly controlling the thickness of the dielectric layer can reduce the deviation of the expected value of electrical performance.
Risk of not doing so
The electrical performance may not meet the specified requirements, and the same batch of components may have large differences in output/performance.
7. Define welding resistance materials to ensure compliance with IPC-SM-840ClassT requirements
benefit
NCAB Group recognizes "excellent" ink, realizes ink safety, and ensures that solder mask ink meets UL standards.
Risk of not doing so
Poor quality inks can cause adhesion, flux resistance and hardness problems. All these problems will lead to the separation of the solder mask from the circuit board and eventually lead to corrosion of the copper circuit. Poor insulation characteristics can cause short circuits due to unexpected electrical continuity/arcing.
8. Tolerances defining profiles, holes and other mechanical features
benefit
Strict tolerance control can improve the dimensional quality of products – improving fit, shape and function
Risk of not doing so
Problems in the assembly process, such as alignment/fit (the problem of press fit pin can only be found when the assembly is completed). In addition, due to the increase of size deviation, there will be problems in mounting the base.
9. NCAB specifies the thickness of the solder mask, although IPC does not specify it
benefit
Improves electrical insulation properties, reduces the risk of peeling or loss of adhesion, and enhances resistance to mechanical impact wherever it occurs!
Risk of not doing so
The thin solder mask can cause adhesion, flux resistance and hardness problems. All these problems will lead to the separation of the solder mask from the circuit board and eventually lead to corrosion of the copper circuit. Poor insulation characteristics due to thin solder mask can cause short circuit due to accidental conduction/arc.
10. Appearance requirements and repair requirements are defined, although not defined by IPC
benefit
In the manufacturing process, we carefully care and carefully cast safety.
Risk of not doing so
A variety of scratches, minor damages, repairs and repairs – circuit boards work but don't look good. In addition to the problems that can be seen on the surface, what are the risks that cannot be seen, the impact on the assembly, and the risks in actual use?
11. Requirements for plug hole depth
benefit
High quality plug holes will reduce the risk of failure during assembly.
Risk of not doing so
Chemical residues in the gold deposition process can be left in the hole with insufficient plug hole, resulting in problems such as weldability. In addition, there may be tin beads hidden in the hole, which may splash out during assembly or actual use, causing short circuit.
12. PetersSD2955 specifies the brand and model of peelable blue glue
benefit
The designation of peelable blue glue can avoid the use of "local" or cheap brands.
Risk of not doing so
Poor or cheap strippable adhesive may bubble, melt, crack or solidify like concrete during assembly, so that the strippable adhesive will not peel off/work.
13. NCAB performs specific approval and order placement procedures for each purchase order
benefit
The implementation of this procedure ensures that all specifications have been confirmed.
Risk of not doing so
If the product specification is not carefully confirmed, the deviation may not be found until the assembly or final product, and it is too late.
14. Sheathing with scrap unit is not acceptable
benefit
Not using local PCB Assembly can help customers improve efficiency.
Risk of not doing so
Defective sheathed boards require special PCB assembly procedures. If the scrapped unit board (x-out) is not clearly marked or it is not isolated from the sheathed board, it is possible to assemble this known bad board, thereby wasting parts and time.