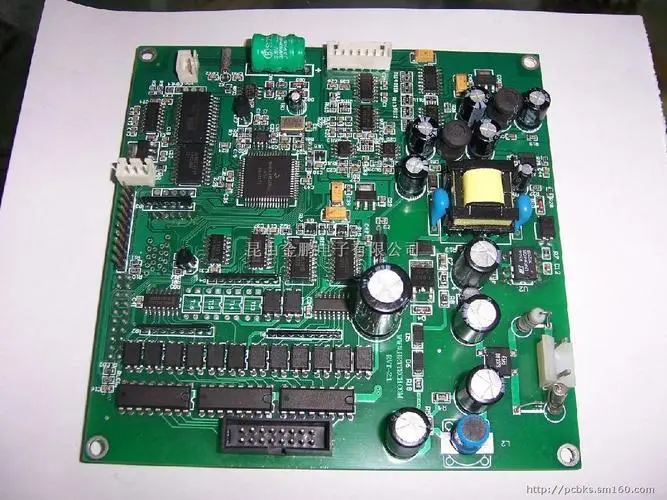
SMT processing plant assembly process is closely related to each process step before welding, including capital investment, PCB design, pcb component solderability, assembly operation, flux selection, temperature/time control, solder and crystal structure, etc.
At present, the most commonly used solder for wave soldering is eutectic tin lead alloy: tin 63%; Lead is 37%, and the solder temperature in the solder pot shall be controlled at all times. The temperature shall be 183 ℃ higher than the alloy liquid temperature, and the temperature shall be uniform. In the past, the soldering pot temperature of 250 ℃ was considered as "standard".
With the innovation of flux technology, SMT processing plant has controlled the uniformity of solder temperature in the entire solder pot, and added a preheater. The development trend is to use a lower temperature solder pot. It is common to set the temperature of solder pot within the range of 230-240 ℃. Generally, the components do not have uniform thermal quality. It is necessary to ensure that all welding points reach sufficient temperature so as to form qualified welding points. It is important to provide enough heat to increase the temperature of all leads and pads, so as to ensure the fluidity of solder and wet both sides of the solder joint. The lower the temperature of the solder, the lower the thermal shock to the components and substrate, which helps to reduce the formation of scum. Under the lower strength, the joint action of the flux coating operation and the flux compound can make the wave crest outlet have enough flux, which can reduce the generation of burrs and solder balls.
The solder composition in the solder pot of SMT processing plant is closely related to time, that is, it changes with time, which leads to the formation of scum, which is the reason for removing residues and other metal impurities from the welded components and the reason for tin loss in the welding process. These factors can reduce the fluidity of solder. During procurement, the maximum limit of tin content of metal trace scum and solder should be specified in various standards (such as IPC/J-STD-006). During welding, the requirements for solder purity are also specified in ANSI/J-STD-001B standard. In addition to the limitation on scum, 63% tin; The minimum tin content specified in 37% lead alloy shall not be less than 61.5%. Gold and organic layer copper concentrations on wave soldering components accumulate faster than in the past. This aggregation, coupled with significant tin loss, can lead to loss of solder mobility and welding problems. Rough and granular solder joints are often caused by dross in solder. The accumulated scum in the solder pot or the dim and rough granular solder joints of the inherent residues of the components themselves may also be a sign of low tin content, either local special solder joints or the result of tin loss in the solder pot. This appearance may also be caused by vibration or impact during solidification.
The appearance of solder joints in SMT processing plant can directly reflect process problems or material problems. In order to maintain the "full pot" state of solder and follow the process control plan, it is important to check the solder pot analysis. It is usually unnecessary to "dump" the solder in the solder pot because there is scum in the solder pot. As solder is required to be added to the pot in conventional applications, the solder in the pot is always full. In the case of loss of tin, the addition of pure tin helps to maintain the desired concentration. In order to monitor the compounds in the tin pot, a routine analysis should be performed. If tin is added, it shall be sampled and analyzed to ensure correct solder composition ratio. Too much scum is a thorny problem. There is no doubt that scum always exists in the solder pot, especially when welding in the atmosphere. The use of "chip wave crest" is very helpful for welding high-density components. Because the solder surface exposed to the atmosphere is too large, the solder will be oxidized, so more scum will be generated. When the solder surface in the solder pot is covered with a scum layer, the oxidation rate slows down.
In PCB welding, more scum will be produced due to the turbulence and flow of wave peaks in the tin pot. The recommended conventional method is skimming the scum. If skimming is carried out frequently, more scum will be produced and more solder will be consumed. The scum may also be mixed in the wave crest, causing instability or turbulence of the wave crest. Therefore, more maintenance is required for the liquid composition in the soldering pot. If it is allowed to reduce the amount of solder in the tin pot, the dross on the solder surface will enter the pump, which is likely to occur. Sometimes, the granular solder joints will be mixed with scum. The scum found initially may be caused by rough wave crest and may block the pump. The tin pot shall be equipped with adjustable low capacity solder sensor and alarm device.