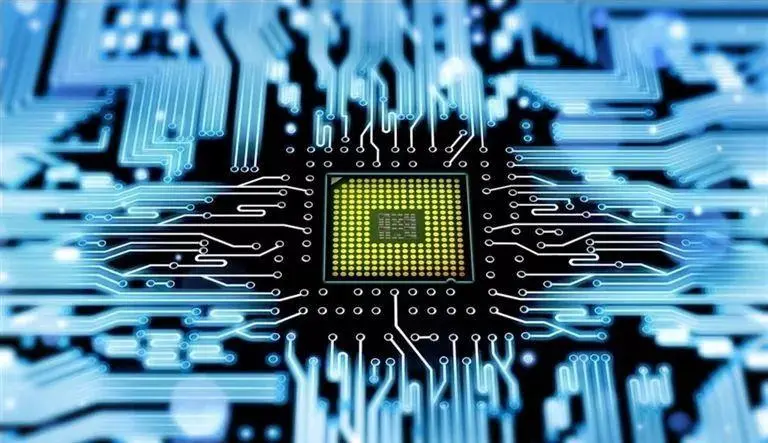
Malaysia Airlines: Malaysia Airlines is the result of organic pollution. Large pits usually indicate oil contamination. If the mixing is not good, bubbles will not be discharged, thus forming pits. Wetting agents can be used to reduce their effects. We usually call small pits pinholes. Improper pretreatment, too little metal impurities, boric acid content and too low bath temperature will produce pinholes. Plating solution maintenance and PCB process control are key, and anti pinhole agent should be used as PCB process stabilizer to supplement.
Roughness and burr: Roughness means that the solution is dirty and can be corrected by proper filtration (if the pH is too high, the precipitation of hydroxide should be controlled). If PCB current density is too high, impurities in anode mud and make-up water will bring impurities, which may cause roughness and burrs in severe cases.
12.jpg
Low adhesion: If the PCB copper coating is not completely deoxidized, the coating will peel off, and the adhesion between copper and nickel will be poor. If the current is interrupted, it will cause the nickel coating to peel off when interrupted, and it will peel off when the temperature is too low.
Fragile coating and poor solderability: When the coating of printed PCB is bent or worn to a certain extent, it usually shows that the coating is fragile. This indicates that there is organic or heavy metal pollution, and excessive additives, entrained organics and electroplating corrosion inhibitors are the main sources of organic pollution, which must be treated with activated carbon. Insufficient additives and high pH value will also affect the brittleness of the coating.
Dark color electroplating and uneven color: Dark color electroplating or uneven color indicates metal pollution. Since copper is usually plated first and then nickel is plated, the introduced copper solution is the main source of pollution. It is important to minimize the copper solution on the hanger. In order to remove metal contaminants in the tank, especially copper removal solution, corrugated steel cathode shall be used. Electroplate 5 amps per gallon of solution at a current density of 2 to 5 a/square inch for 1 hour. Poor pretreatment, poor electroplating, low current density, low concentration of main salt and poor contact of electroplating power circuit will affect the color of electroplating.
Coating burn: Possible causes of PCB coating burn: insufficient boric acid, low metal salt concentration, low operating temperature, high current density, high pH or insufficient stirring.
Low deposition rate: Low pH value or low current density will result in low deposition rate.
Foaming or peeling of coating: poor pretreatment of PCB before electroplating, too long intermediate power off time, organic impurity pollution, too high current density, too low temperature, too high or too low pH, and serious influence of impurities will lead to foaming or peeling.