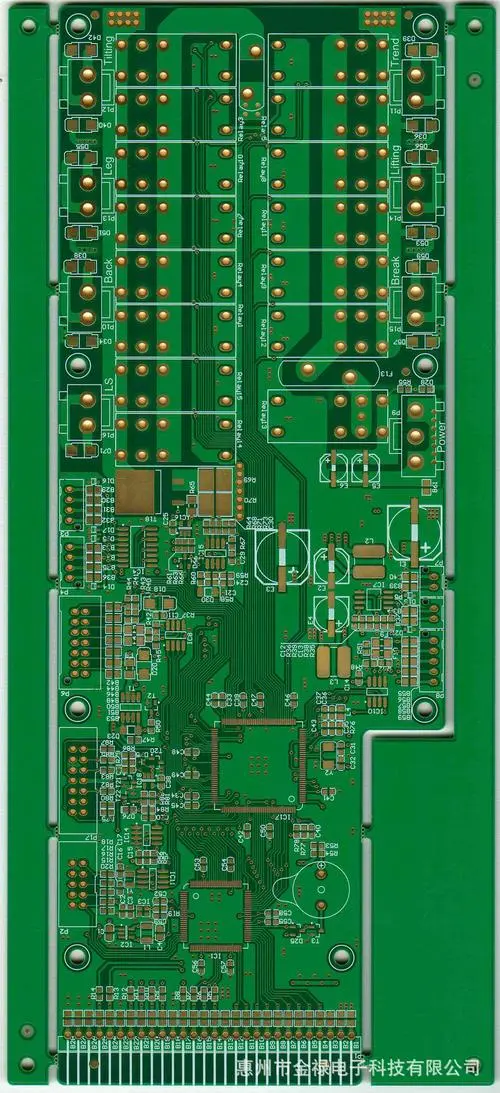
An important part of the PCBA process is the use of solder paste. Solder paste is one of the important raw materials for PCBA processing. How to select the solder paste for PCBA processing will affect the quality of SMT and even PCBA finished products. This article is about PCBA processing. Discuss how to select solder paste.
Solder paste is a paste or paste evenly mixed with alloy solder powder and solder flux. Since the main metal component of most solder pastes is tin, solder pastes are also called solder pastes. Solder paste is an indispensable solder in SMT process and is widely used for reflow soldering. The solder paste has a certain viscosity at room temperature, which can initially bond the electronic components to a predetermined position. At the welding temperature, as the solvent and some additives volatilize, the welded parts will be connected to each other to form a permanent connection.
At present, SMT stencil printing method is adopted for most of the coated solder pastes, which has the advantages of simple operation, fast, accurate and available immediately after production. But at the same time, there are also shortcomings such as poor reliability of solder joints, easy to cause false soldering, waste of solder paste, high cost, etc.
1. Composition of solder paste
The solder paste is mainly composed of alloy solder powder and flux. Among them, alloy solder powder accounts for 85% to 90% of the total weight, and flux accounts for 15% to 20%.
Polychlorinated biphenyls
Alloy solder powder
Alloy solder powder is the main component of solder paste, and is also the most important consideration when selecting solder paste in PCBA process. Common alloy solder powders include tin/lead (Sn pb), tin/lead/silver (Su pb Ag), zinc/lead/bismuth (Su pb Bi), etc. The commonly used alloy compositions are 63% Sn/37% pb and 62% Sn/36% pb/2% Ag. Different alloy ratios have different melting temperatures.
The shape, particle size and surface oxidation degree of alloy solder powder have great influence on the performance of solder paste. Alloy solder powder can be divided into two types according to its shape: amorphous and spherical. Spherical alloy powder has small surface area and low oxidation degree, and the prepared solder paste has good printing performance. The particle size of alloy solder powder is generally 200-400 mesh. The smaller the particle size, the higher the viscosity; If the particle size is too large, the bonding performance of the solder paste will be poor; Too fine particle size will increase the oxygen content on the surface due to the increase of surface area, which is not suitable for use.
flux
In the solder paste, the solder paste flux is the carrier of alloy powder. Its composition is basically the same as that of ordinary flux. In order to improve the printing effect and thixotropy, thixotropic agents and solvents are sometimes needed. The oxide film on the surface of the welding material and the alloy powder itself can be removed through the action of the active agent in the flux, so that the solder can rapidly diffuse and adhere to the surface of the welding metal. The composition of flux has a great influence on the expansion, wettability, collapse, viscosity change, cleaning performance, weld bead splash and storage life of solder paste.
2、 Classification of solder pastes
There are many types of solder paste, which may cause some problems when selecting PCBA process. Solder pastes can generally be classified according to the following characteristics:
1. According to the melting point of alloy solder powder
The melting point of the most commonly used PCB solder paste is 178-183 ° C. Depending on the type and composition of metal used, the melting point of the solder paste can be increased to 250 ° C or higher or lower to 150 ° C, depending on the temperature required for welding. Select solder pastes with different melting points.
2. Activity according to flux
According to the classification principle of general liquid flux activity, it can be divided into three levels: non activity (R), towel equivalent activity (RMA) and activity (RA). Select according to the conditions of PCB components and cleaning process requirements.
3. According to the viscosity of solder paste
The viscosity range is very special, usually 100~60OPa · s, up to 1000Pa · s. Select according to different methods of application c
that can be bent to a certain extent. FPC can be divided into several types according to functions