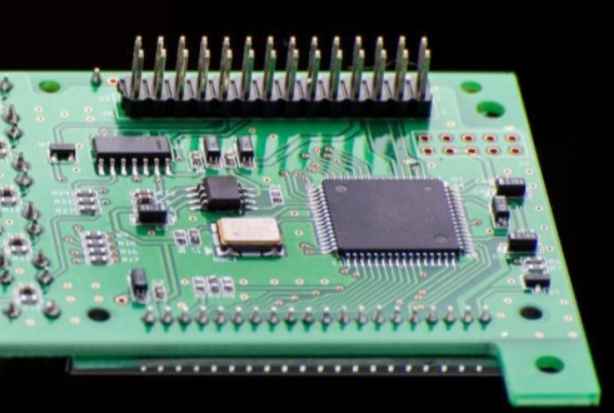
QFN расшифровывается как квадратная плоская бесконтактная упаковка и является одним из корпусов компонентов для поверхностного монтажа SMT. Почему после SMT-обработки и сварки заплат, контактная площадка припоя вокруг стороны QFN не лужится или поднимается по высоте, что не может удовлетворить требования клиентов? Это долговременная головная боль для персонала SMT
Из-за строгости процесса обработки многие специалисты по поверхностному монтажу считают, что боковая площадка QFN должна быть заполнена так же, как штифт QFP, а обнажение меди на стороне QFN, не покрытое припоем, является ненормальной сваркой. На самом деле, это тоже неправильно, олово QFN в основном определяется эффектом сварки в нижней части корпуса, а количество олова, поднимающегося сбоку, обычно соответствует требованиям заказчика. Стандартная боковая накладка QFN IPC-A-610 делится на три класса; Уровень 1: нижняя чаша QFN наполнителя явно мокрая; Уровень 2 составляет 25% высоты боковой накладки; Стандарт класса 3 составляет 50% высоты боковой накладки;
1. Почему сложно залудить сторону QFN?
Поскольку приваренный конец бокового штифта QFN представляет собой голую медь, а медь образует оксид меди из-за химической реакции 2Cu+O2=2CuO в воздухе, хорошо известно, что существует метод обработки поверхности, называемый «голая медная пластина», аналогичный этому явлению, который легко подвергается воздействию кислоты и влажности, не может быть убран в течение длительного времени и должен быть израсходован в течение 4 часов после распаковки. В противном случае оголенная медь будет окисляться на воздухе, что скажется на качестве сварки. Точно так же, если необходимо потребовать, чтобы QFN монтировал олово на своей стороне, необходимо контролировать время после вырезания QFN и воздействия на медь. HОднако, поскольку время транспортировки и хранения между изготовлением QFN и обработкой SMT-заплат намного превышает 4 часа, добиться хорошего эффекта олова нереально. Настоящая причина, по которой сторона QFN не покрыта лужением, заключается в том, что боковой контакт QFN обрезан. После резки поверхность не обработана сварочным аппаратом и имеется оксидный слой.
2. Решение
(1) Может быть уместно использовать внутреннюю резку и внешнюю вытяжку отверстия стальной сетки, внутреннюю резку, чтобы уменьшить положение размера поперечной резки сварочного диска, уменьшить появление олова, моста и других плохих процессов сварки. В то же время отверстие стальной сетки в месте сварочной площадки чипа QFN расширяется, чтобы увеличить количество оловянной пасты штифта QFN и обеспечить достаточное количество олова в процессе подъема олова.
(2) Выберите бессвинцовую экологическую технологию QFN для сварки паяльной пастой. Выберите высокотемпературную паяльную пасту SAC305 или SACX0307 QFN, номер порошка может выбрать использование порошка № 4, в процессе печати стальной сетки имеется большое количество олова, что полезно для лазания по олову;
(3) В случае плохого олова на стороне QFN, соответствующее количество припоя может быть добавлено к периферии перед пайкой оплавлением для обработки патчей SMT, и эффект подъема припоя будет значительно улучшен;
Анализ причин появления отверстий (пузырей) в паяных соединениях во время обработки патчей PCBA
При обработке заплат PCBA, независимо от сварки оплавлением или пайки волной, некоторые отверстия (пузыри) неизбежно появляются после охлаждения паяных соединений PCBA. Основная причина пустот в паяном соединении заключается в том, что пузырьки, образующиеся при пиролизе органического вещества во флюсе, не могут вовремя выйти. Флюс израсходовался в зоне орошения, и вязкость паяльной пасты сильно изменилась. В это время флюс в припое трескается, в результате чего пузырек после высокотемпературного растрескивания не переливается вовремя и герметизируется в припое, образуя полость после охлаждения
1. Влияние активности потока
Из-за высокотемпературного пиролиза органического вещества во флюсе пузырькам воздуха трудно выйти, в результате чего газ заворачивается в порошок сплава. Из процесса видно, что органические вещества, выделяемые теплом, образующимся по основному пути пузырьков: паяльная паста во флюсе, другие органические вещества, флюс для пайки волной или примеси. Эти органические соединения разлагаются при высоких температурах с образованием газов. Из-за относительно небольшой доли газа газ будет находиться во взвешенном состоянии на поверхности припоя во время сварки, и газ в конечном итоге выйдет и не останется на поверхности порошка сплава. Однако при сварке необходимо учитывать поверхностное натяжение припоя и силу тяжести свариваемой детали. Таким образом, поверхностное натяжение паяльной пасты и гравитация компонента должны быть объединены, чтобы проанализировать, почему газ не может выйти с поверхности порошка сплава, образуя таким образом полость. Если плавучесть газа, создаваемого органическим веществом, меньше поверхностного натяжения припоя, то органическое вещество в флюсе после пиролиза при высокой температуре будет окружено газом внутри сварочного шара, газ будет глубоко поглощен сварочным шаром, в это время газу трудно выйти, а затем образуется полость.
2. Это связано со степенью окисления печатной платы
Чем выше степень окисления и загрязнения поверхности контактной площадки печатной платы, тем больше отверстий будет образовано паяными соединениями печатной платы после сварки. Поскольку чем больше степень окисления накладки, тем сильнее требуется активный агент для обработки оксида на поверхности свариваемого объекта. В частности, при обработке поверхности OSP (органический растворитель-консервант) трудно удалить органическую защитную пленку на прокладке OSP. Если вовремя не удалить оксид с поверхности площадки, оксид останется на поверхности свариваемого объекта. В это время оксид будет препятствовать контакту порошка сплава с поверхностью свариваемого металла, что приведет к образованию явления плохого отторжения при сварке. Поверхностное окисление является серьезным, и органический газ, разлагающийся при высокой температуре, будет скрываться в порошке сплава. В то же время поверхностное натяжение без свинца велико, доля сплава относительно велика, газу трудно выйти, газ будет окружен порошком сплава. Следует избегать окислов на поверхности паяльной пасты и свариваемого металла. В противном случае нет другого способа уменьшить образование полостей.
3. Влияние точки кипения растворителя
Будь то растворитель перед пайкой волной припоя или сама паяльная паста, температура кипения между ними напрямую влияет на размер полости паяного соединения печатной платы и вероятность образования полости. Чем ниже температура кипения растворителя, тем выше вероятность образования пустот. Таким образом, вы можете выбрать растворитель с высокой температурой кипения, чтобы избежать кавитации. Если температура кипения растворителя низкая, растворитель будет испаряться в зоне постоянной температуры или в зоне дефлегмации, оставляя только высоковязкое и трудноподвижное органическое вещество, которое необходимо окружить. Поэтому при выборе паяльной пасты старайтесь выбирать паяльную пасту с растворителем с высокой температурой кипения, чтобы уменьшить возникновение явления кавитации.
4.Время сварки
Время пропитки припоем Sn63-Pb37 очень короткое, около 0,6 с против 1,5 с у припоя SnAgCu, в то время как поверхностное натяжение бессвинцового припоя высокое, скорость движения низкая, припой обладает меньшей смачиваемостью и диффузионной способностью, чем у свинцового припоя. В этих случаях газ, образующийся при пиролизе органического вещества, трудно отделить, и газ будет полностью окружен слоем сплава. Конечно, вероятность образования пузырей в бессвинцовом припое намного выше, чем в свинцовом, что также является проблемой и проблемой, с которой сегодня сталкивается процесс бессвинцовой сварки при обработке заплат для печатных плат.
5. Вызвано чрезмерным поглощением влаги из воздуха оловянной пастой
Паяльную пасту следует использовать в соответствии с правильным методом. После извлечения паяльной пасты из холодильника ее следует выдержать при комнатной температуре (25°С±3°С) не менее 4 часов. Когда паяльная паста нагревается, помните, что крышку паяльной пасты нельзя открывать заранее, и паяльную пасту нельзя предварительно нагревать. Также избегайте вдыхания влаги в воздухе. Перед использованием в сети паяльную пасту необходимо перемешать. Цель состоит в том, чтобы равномерно смешать порошок сплава и флюс. В процессе смешивания время не должно быть слишком большим (около 3-5 минут), усилие смешивания не должно быть слишком большим. Если сила слишком велика в течение слишком долгого времени, порошок сплава может быть раздавлен, что приведет к окислению металлического порошка в паяльной пасте. Если порошок паяльной пасты окислен, вероятность появления отверстий после проточной сварки значительно возрастает. После печати паяльную пасту нельзя держать на воздухе слишком долго (как правило, в течение 2 часов), иначе паяльная паста впитает слишком много воды, что повысит вероятность образования полости. Можно видеть, что правильное использование сварочной пасты очень важно и должно осуществляться в соответствии с правильным использованием сварочной пасты, в противном случае дефекты сварки после сварки оплавлением печатных плат будут значительно увеличены. Таким образом, правильное использование сварочной пасты будет необходимым условием для обеспечения качества различных сварочных работ, которому необходимо придавать большое значение.
С быстрым развитием индустрии обработки заплат для печатных плат плотность компонентов становится все выше и выше, а количество слоев подложки печатных плат увеличивается, что ставит новые задачи перед технологией обработки заплат для печатных плат. Что касается надежности печатной платы, то, как только площадь пустот в паяном соединении превысит стандарт IPC, это повлияет не только на механические свойства компонентов, но и на электрические свойства всего продукта. Явление пустот принесет неисчислимый риск паяному соединению. Таким образом, PCBA плюс заводской строгий контроль полости паяного соединения PCBA (пузырька) очень важен, на него следует обращать большое внимание.
Вышеупомянутое содержание предоставлено Kingford-, фабрикой пообработке заплат PCBA, о (анализ причин отверстий (пузырей), образующихся паяными соединениями при обработке заплат PCBA).