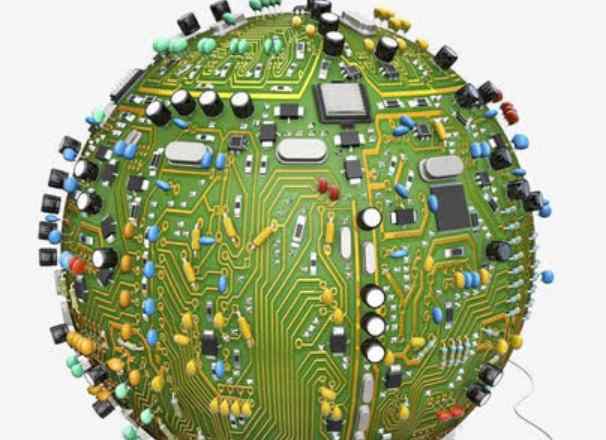
Power circuit is an important part of electronic products, the design of power circuit will directly affect the product performance. Next, Pulin Xiaobian and you share some engineers on the power PCB design experience summary, I hope to help you.
Basic principles of PCB layout and wiring for power supply
1) Select the correct number of sheets and copper thickness.
2) In the system design layout planning, the power circuit should be as close to the load circuit as possible. In particular, the power supply of the core processor should be as close together as possible. If they are far apart, both transient response and line impedance can be problematic.
3) The cooling circuit should be as close as possible to the power supply circuit to reduce thermal resistance.
4) On the board with heat dissipation convection, pay attention to the layout of large passive devices (inductors, large capacitors), do not hinder the air convection of the chip and MOSFETs.
Summary of experience in PCB design of power supply
1. When placing devices, if there are some large capacitors or resistors together with relatively small resistors and capacitors, choose the way of center alignment rather than edge alignment. Because when doing packaging, is to carry out the pad compensation, so in the actual welding, it is not aligned, so it is not beautiful.
2, in the power chip layout and wiring, the first should download the data manual for reference.
3. For the layout and wiring of switching power supply, it is to find the main circuit of input and output. That is, VIN, VOUT, when you put the device, it has to be compact, first large and then small (the volume of the device). It's compact, but it has to leave room for holes and copper.
4, the layout is a font, this is the case of abundant position. Wiring is mostly copper treatment, a small part of the wiring, wiring at least 10mil start. If 10mil of wire exceeds the size of the pad, you can first walk out of the pad and then walk the wire into 10mil.
5. The current of 20mil wire crossing 1A, and the current of 10/20 crossing 1A through hole. Note that these are theoretical values, in practice, you have to leave a certain margin. As many holes as you put in your input loop, you have to put the same number of holes in your output loop.
6. Consider the problem of welding. If the copper skin and the pad are fully connected, when you get on the solder, due to the large contact area, the heat dissipation is relatively fast, so there is no device, the solder has been solidifying. So we use cross connection for Pin and copper, which is better for welding.
7. The feedback path, usually the FB signal of the last device, or the SENS signal, goes 20mil.
8. The wiring of the power supply is short, straight and thick, similar to that of the radio frequency.
9, power board part of the inductance, do not follow the line, and the middle needs to be hollowed out. Because inductance is a large source of interference. If there are multiple outputs, the presence of multiple inductors, adjacent to each other using vertical placement.
10, the capacitor must be placed close to the chip pin, so that the filtering effect is the best. The signal has to pass through the capacitor before it enters the chip.
11. The input port should not be in front of the capacitor, and the output port should be placed after the capacitor, and the GND port should be placed nearby.
12, power for high-speed board, need to consider the problem of PI, is the problem of power integrity, this simulation can be measured.
13. The integrity of the power supply should also have certain requirements for the lamination of the high-speed plate. We can design the lamination according to the previous experience, or use the SI9000 to calculate the impedance, and then communicate with the plate factory to get reasonable results.
14. For the division of the power layer, the division is the core power supply of the board. What is the core power supply, is some power supply current, the number of the kind. A plane, not more than 3 power supply division. It is important to consider that segmentation cannot present current-carrying bottlenecks.
15, when there is a digital and analog ground, the need to be covered with copper processing, commonly used is the use of zero ohm resistance or magnetic beads for bridging, and play the right amount of holes, can not interfere with other signals.
16, in the cascade setting, need to meet the principle of 20H, that is, the power plane than the ground plane shrink 20mil, if the board is big enough, can be adjusted by 30-50mil. And the inner part of the hole with the right amount of ground. (100-150mil equal spacing)