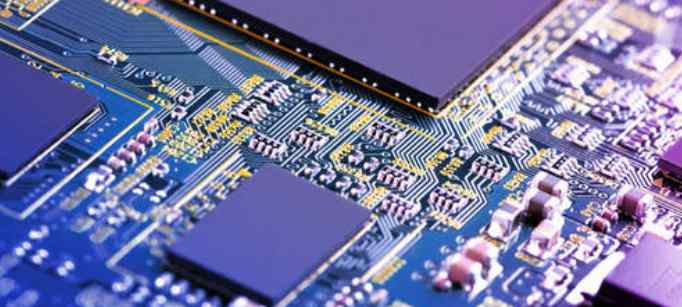
In the process of pcb design, before wiring, we usually stack the project we want to design, calculate the impedance according to the thickness, substrate, layer number and other information, and generally get the following content after calculation.
Single-ended networks are typically designed to be controlled at 50 ohms, so a lot of people ask, why is it required to be controlled at 50 ohms instead of 25 ohms or 80 ohms?
First of all, the default is 50 ohms, which is accepted by everyone in the industry. In general, there must be some standard set by some recognized body, and people design to that standard.
A large part of electronic technology comes from the military. The technology was first used in the military, and then gradually transferred from the military to civilian use. In the early days of microwave application, during World War II, impedance selection was entirely dependent on the need for use, and there was no standard value. As technology advances, impedance standards need to be given in order to strike a balance between economy and convenience.
In the United States, the most commonly used catheters are made from existing measuring rods and pipes. 51.5 ohms are common, but adapters and converters are 50-51.5 ohms seen and used. In order to unite the Army and Navy in solving these problems, an organization called JAN (later DESC) was formed, developed by MIL in particular, and a combination of considerations led to the choice of 50 ohm, from which the relevant conduit was manufactured and thus translated into a standard for various cables.
At this point the European standard was 60 ohms, and before long, under the influence of dominant companies like Hewlett-Packard, the Europeans were forced to change, so that 50 ohms eventually became a standard in the industry, and it became the norm, and PCB's with all kinds of cables, In order to match the impedance, the final requirement is also in accordance with the 50 ohm impedance standard.
Secondly, the formulation of general standards will be based on the PCB production process and design performance, feasibility of comprehensive consideration.
From the point of view of PCB production and processing technology, considering the equipment of most existing PCB manufacturers, it is relatively easy to produce PCB with 50 ohm impedance. It can be seen from the calculation process of impedance that a low impedance requires a wide line width and a thin medium or a large dielectric constant, which is difficult to meet in space for the current high-density plate. Too high impedance requires a finer line width, thicker medium or smaller dielectric constant, which is not conducive to EMI and crosstalk suppression. Meanwhile, the reliability of processing will be poor for multilayer plates and from the perspective of mass production.
Control 50 ohm impedance in the use of common plate (FR4, etc.), common core plate environment, the production of common plate thickness products (such as 1mm, 1.2mm, etc.), can be designed common line width (4~10mil), this sample factory processing is very convenient, the processing of the equipment is not very high requirements.
In terms of PCB design, 50 ohm is also selected after comprehensive consideration. In terms of PCB wiring performance, generally low impedance is better. For a transmission line with a given line width, the closer the distance between the line and the plane, the corresponding EMI will decrease, so will the crosstalk. However, from the perspective of signal full path, the most critical factor should be considered, that is, the driving capability of the chip. In the early stage, most chips could not drive the transmission line with impedance less than 50 ohm, and the transmission line with higher impedance was inconvenient to realize, so 50 ohm impedance was adopted as a compromise.
Lead-free process: One of the basic concepts of lead-free electronic assembly is that the solder used in the soft brazing process is lead-free solder (pb-feer soder), whether manual soldering, dipping, wave soldering or reflow soldering. Lead-free solder does not mean that the solder is 100% lead free. Lead is present as an essential element in leaded solder. In lead-free solder, the basic element does not contain lead.
Lead process: sn-pb solder is generally used in the soft brazing process of the traditional printing plate assembly, in which lead exists and plays a role as a basic element of solder alloy. Lead solder alloy low melting point, low welding temperature, less thermal damage to electronic products; Lead solder alloy wetting Angle is small, good weldability, product solder joint "false welding" possibility is small; The toughness of the solder alloy is good, and the vibration resistance of the solder joint is better than that of the lead-free solder joint.
Compared with.osp lead-free tin spray and gold plating process, these three surface treatments. Although they are all relatively environmentally friendly,
But most common conventional boards are used more for the first two. Because the cost is lower.
osp is suitable for fine line and fine SMT spacing. Low operating temperature, no damage to the sheet material, easy to rework repair.
But the board made by osp process is not acid resistant, and its welding performance will be affected by high humidity environment. It needs to be welded in the shortest possible time and the gold plating is relatively resistant to wear. But there is a difference between the two: gold plating process only on the surface, the side or only copper nickel, a long time easy oxidation, this is a defect of gold plating process, can not be used in the occasion of high requirements.
Do the whole pad, including the side can be plated with nickel gold, is the most stable at present, can be used in a variety of occasions, but nickel gold has a headache, is more difficult to find the problem, that is, the adhesion is not as good as gold plating, easy to fall off after a period of use.