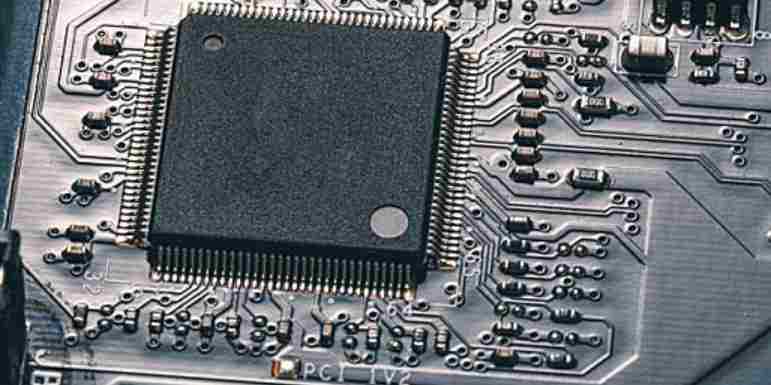
Reinforcement and integration design can be used to improve material performance for high flexural applications
In the process of FPCB, copper foil and substrate will be made first, truncated and then perforated, electroplating operations, roughly in the hole position of FPCB pre-completed, the beginning of the photoresist material coating treatment, the completion of the exposure development process of FPCB, will be prepared to etch the line for processing, Solvent etching is carried out immediately after the exposure development process is completed. At this time, after etching to a certain extent, the conductive circuit is formed, and the solvent is cleaned on the surface to remove the solvent. In this case, the adhesive is evenly coated on the FPCB base and the etched copper foil surface, and then the coating layer is attached to the surface.
After completing the above operations, FPCB has been roughly 80% complete. At this time, we also need to treat the connection points of FPCB, such as adding the guide welding treatment of opening holes, etc., and then carry out the appearance processing of FPCB. For example, after using laser to cut a specific appearance, if the FPCB is a soft and hard composite board or needs to be welded with the function module, At this time for secondary processing, or with reinforcing plate processing design.
The uses of FPCB are quite diverse, and the production difficulty is not high, only FPCB itself can not make too complex and tight circuit, because too thin circuit will be too small copper foil cross-sectional area, if the FPCB bending, it is easy to make the internal line fracture. Therefore, most of the circuits that are too complex will use the core HDI high-density multilayer board to deal with the related circuit requirements, only a large number of data transmission interfaces, or data I/O transmission connection of different functions of the board, will use FPCB for board connection.
This is a time of rapid change. In addition to creativity and design abilities, today's designers face many limitations, and they have to deal with an increasing number of increasingly complex designs -- a series of peripherals connected through IO. What's more, today's design is increasingly geared toward smaller, lower cost and faster products, especially in the mobile device market. In recent years, a large number of high-performance, multifunctional devices emerge in an endless stream, the market development is particularly rapid, so that savvy consumers dizzying. Bringing these products to the electronics design market requires a tight design process, which often involves a high density of electronic circuits, as well as consideration to reduce manufacturing time and cost.
One solution to help designers and design teams meet these challenges is to adopt soft-hard design techniques, or soft-hard design for printed circuit boards (PCBS). While this is not the latest technology, a combination of factors suggests that it is universal and can reduce costs. From the traditional rigid PCB connected by cable to the current soft and hard board technology, from the cost aspect, two hard board and soft cable interconnecting is feasible for short-term design; But that would require connectors on each board, which would need to be attached to circuit boards and cables -- all of which would add to the cost. In addition, rigid cable-connected PCBS are prone to electrowelding, which can lead to failure. In contrast, hard-soft combined circuits can eliminate these virtual solder joints, making them more reliable and providing higher overall product quality.
Taking a closer look at the total cost, Figure 1 compares the simulation manufacturing cost of a rigid PCB with a traditional cable connection and a 3D combination of soft and hard design. While traditional designs consist of rigid boards using flexible cables and connectors, the combination design is embedded in a rigid board with two built-in soft layers in between, and the overall structure is a set of four layers of printed circuit boards. Manufacturing costs for both designs are based on quotes from PCB manufacturers, including assembly costs. In addition, the cost of two separate four-layer circuit boards, connectors, and cables in the traditional design factor is added.
Figure 1: Comparison of assembly costs of rigid PCBS in combination of soft and hard design and cable connection.
As can be seen from the figure, when the number of manufacturing is more than 100 sets, the combination of soft and hard design will save time and increase efficiency compared with the traditional design scheme. This is mainly because the hard-soft circuit does not contain any connector components/cables and does not require connector assembly. Not only that, they have reliable performance and sophisticated technology. And that's just the tip of the iceberg.
With the combination of soft and hard technology, designers can interconnect multiple PCBS in a single package without the need for connectors, wires and cables. Because the combination board does not require cable assembly, it reduces overall assembly consumption and test complexity, both of which help keep costs down. In addition, there are fewer components to buy, which reduces the bill of materials, which reduces supply chain risk and costs. The combination of hard and soft board makes the maintenance of the product more convenient and saves the cost throughout the product life cycle.