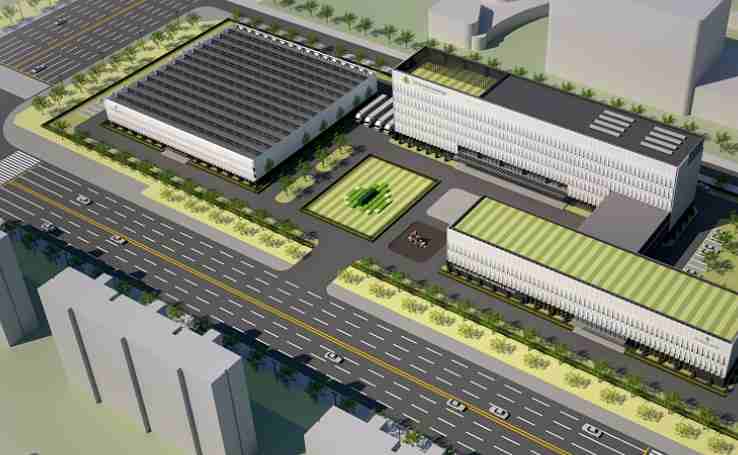
PCB is one of the indispensable parts of electronic equipment, it appears in almost every kind of electronic equipment, in addition to fixing a variety of large and small parts, the main function of PCB is to let the parts electrical connection. Since the raw material of PCB board is copper-covered board, copper dumping will occur in the process of PCB production. Then what are the reasons for copper dumping of PCB board? Here is to introduce it to you.
Four reasons for PCB board copper throwing
1, PCB circuit design is not reasonable, with thick copper foil design of too thin line, will also cause excessive line etching and copper.
2, copper foil etching is excessive, the electrolytic copper foil used on the market is generally single-side galvanized (commonly known as gray foil) and single-side plated copper (commonly known as red foil), the common copper is generally more than 70um galvanized copper foil, red foil and 18um below the basic ash foil has not been a batch of copper.
3. Local collision occurs in PCB process, and the copper wire is separated from the substrate by external mechanical force. This defect manifests as poor positioning or orientation, falling copper wire will have obvious distortion, or in the same direction of the scratch/impact mark. Peel off the bad part of the copper wire to see the copper foil surface, you can see the normal color of the copper foil surface, there will be no bad side erosion, copper foil peeling strength is normal.
4. Under normal circumstances, as long as the hot pressing high temperature section is over 30min, the copper foil and the semi-cured sheet are basically combined, so the pressing generally will not affect the binding force of the copper foil and the substrate in the laminate. However, in the process of laminate stacking and stacking, if PP pollution or copper foil surface damage, it will also lead to insufficient bonding force between copper foil and substrate after laminate, resulting in positioning (only for the large plate) or sporadic copper wire loss, but the stripping strength of copper foil near the stripping line will not be abnormal.
Welding principle and welding tools
First, welding principle
At present, the soldering technology of electronic components is mainly used. Tin welding technology uses tin alloy material mainly as solder, solder melts at a certain temperature, mutual attraction, diffusion and combination between metal welds and tin atoms, forming a combination layer of infiltration. It seems that the copper platinum of the printing board and the leads of the components are very smooth, but in fact, there are many small convex and convex gaps on the surface of them. The molten solder diffuses along the surface of the welds with the help of capillary suction, forming the infiltration of solder and welds, firmly bonding the components and the printing board, and has good electrical conductivity.
The conditions of tin welding are: the surface of the solder should be clean, oil dirt, rust will affect the welding; Metals that can be moistened by tin solder can be weldable. For materials that are easy to generate oxide film on the surface of brass and other materials, you can use flux to solder the surface of the welding parts before soldering; To have appropriate heating temperature, so that the solder material has a certain fluidity, can achieve the purpose of welding, but the temperature can not be too high, too high is easy to form oxide film and affect the welding quality.
Two, electric soldering iron
The main tool for manual welding is the electric soldering iron. There are many kinds of electric iron, direct heat type, induction type, energy storage type and temperature control type, electric power is 15W, 2OW, 35w...... 300W variety, mainly according to the size of the weldment to decide. General components of the welding to 2OW internal hot electric soldering iron is appropriate; Energy storage electric soldering iron can be used when welding integrated circuits and vulnerable components; Large welding parts can be used 150W~300W high power external heat type electric soldering iron. Small power electric soldering iron head temperature is generally between 300~400℃.
Soldering iron head is generally made of red copper material. In order to protect the iron head from oxidation and rust under high temperature conditions of welding, the iron head is often treated by electroplating. Some iron heads are also made of alloy materials that are not easy to oxidize. The new iron head should be tinned before formal welding. The method is to polish the iron head with gauze paper, and then dip into the rosin, dip in the solder on the hard object (such as wood) repeatedly grinding, so that each face of the iron head all tin. If the use of a long time, the iron head has been oxidized, to use a small file to gently file the surface oxidation layer, after exposing the bright copper with the same method as the new iron head tin plating for processing. When only a electric iron is used, the temperature of the iron head can be adjusted by using different methods to insert the iron core into the iron head. The longer the iron head is pulled out from the iron core, the lower the temperature of the iron head is relatively, and the higher the temperature is on the contrary. It can also be used to change the size and shape of the iron head to adjust the temperature of the iron head. The thinner the iron head, the higher the temperature; The thicker the iron head, the lower the relative temperature.
According to the type of welding components can choose the appropriate shape of the iron head. The shape of the iron head is conical, inclined oval and chisel and so on. Conical welding can be used for small solder joints, and chisel or cylindrical welding can be used for large solder joints.
There is also a tin absorbing electric iron, which is composed of a tin absorbing mechanism increased on the direct heat type electric iron. This kind of electric iron is used when dissoldering components in the circuit
Three, solder and flux
Solder is the main material for welding. Solder for welding electronic components is actually a kind of tin lead alloy, different tin lead ratio solder melting point temperature is different, generally 180~230 ℃. Manual welding is suitable for the use of tubular solder wire, solder wire sandwiched with rosin and activator, extremely convenient to use. Tubular solder wire has 0.5, 0.8, 1.0, 1.5... Such as a variety of specifications, can be conveniently selected.
Flux, also known as flux, is a kind of material that can clean and protect the surface of the welding metal after being heated. An oxide film is readily formed on the surface of the metal in the air. This oxide film prevents the solder from wetting the welding metal. The proper use of flux can remove the oxide film, so that the welding quality is perfect, the surface of the solder joint is smooth and rounded.
Flux has inorganic series, ** series and rosin series three, among which inorganic flux activity is strong, but has strong corrosion effect on metal, electronic components welding is not allowed to use. ** flux (such as diethyl hydrochloric acid) activity is second, but also slightly corrosive. Rosin flux is widely used. Melt rosin into alcohol (1:3) to form "rosin". Dip a small amount of rosin into the solder joint during welding to achieve good welding aid effect. When the amount of excessive or multiple welding, forming black film, rosin has lost the role of welding aid, need to clean up before welding. For metal components that are difficult to weld with rosin flux, about 4% diethyl or triethyl hydrochloride (6%) can be added. As for all kinds of flux sold on the market, it is necessary to understand its composition and corrosion effect on components before using. Do not blindly use, so as to cause the corrosion of the components in the future, its infinite consequences.