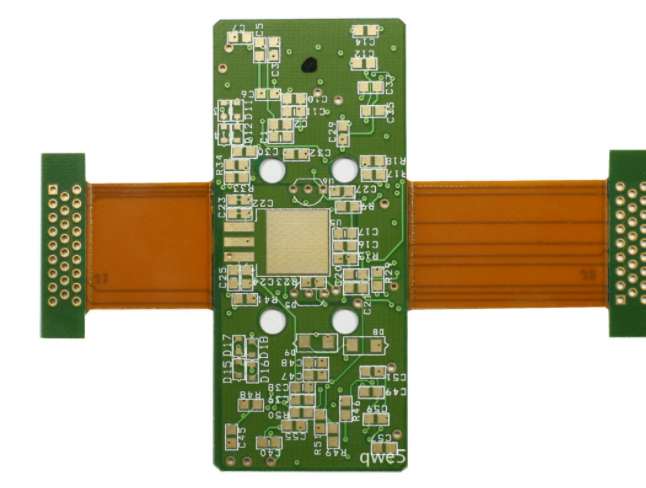
High quality SMT plant must have high quality, high precision processing equipment, in order to ensure the reliability of PCBA welding. Including printing machine, patch machine, reflow welding, detector, and AOI, etc. Today, we are going to share with you how PCBA processing plants choose high quality reflow welding. Hope to bring you some help!
1. Look at the heating method of reflow welding
The heating methods of reflow welding are generally divided into two categories: one is by the red lamp and adapted tube heater; The other type is ceramic plate, aluminum plate and stainless steel plate heater.
Tubular heater: It has the advantages of high working temperature, short radiation wavelength and fast heat response, but because of the production of light when heating, it has different reflection effect on welding components of different colors, at the same time, it is not conducive to matching with forced hot air.
Plate heater: slow thermal response, slightly low efficiency, but due to the large thermal inertia, through the perforation is conducive to the heating of the hot air, the color sensitivity of the welded element is small, the shadow effect is small, the current sales of reflow welding furnace, the heater is almost all aluminum plate or stainless steel heater.
2. Investigate the actual temperature difference of reflow welding
In order to consider the temperature difference in the actual operation of a reflow welding machine, the actual operation measurement of the field equipment is required. Open the track of the reflow furnace to the maximum position, place a PCBA, and set 5 ~ 6 test points on the PCBA along the cross section of the furnace, measure the temperature difference of the plate surface when no load, the temperature difference should be less than 1 degree Celsius. Then continuously put PCBA(full load), measure the temperature of the last PCBA panel (same as the first one), in order to distinguish the temperature difference on the PCBA when the full load, generally around plus or minus 3 degrees Celsius. In the third step, different analog IC blocks were placed on the PCBA and then tested. This judgment can effectively see the temperature change when the reflow furnace is fully loaded. At the same time, the actual temperature change shown on the reflow welding table should not exceed plus or minus 5 degrees Celsius.
3, equipment size supply capacity
The width of 400mm*400mm more than the choice of large equipment or medium. The width of furnace net belt in 8-temperature zone for medium reflow welding is 400mm, and the width of furnace net belt in 12-temperature zone for large reflow welding is 550mm. If a guide is required, the standard 12-temperature zone width of the guide is 450mm. According to the size of your product to determine the width of the net belt, after all, the shape of the network bandwidth equipment also increase.
3. Operation power of reflow welding
The operation power of large reflow welding equipment is higher than that of small reflow welding equipment. But the same temperature zone models of different manufacturers, its normal operation power is not the same. In the normal operation of the equipment, the electric energy is mainly provided for the welding of the equipment, but it will also cause the heat loss of the equipment. The good insulation effect can save a lot of electricity, and the poor insulation will cause excessive energy loss and increase the production cost.
4. Look at appearance and volume
Reflux welding is surface welding by high temperature action. The longer the PCBA stays in reflow welding, the better the welding effect will be. Therefore, the larger the volume of the reflow welder, the longer the heating area.
5. Transmission stability
The reflow welding process is performed by a relatively good process. In operation to ensure that the PCBA transmission network belt is stable, will not shake. If the belt vibrates, welding defects will result.
6. Operation control system
The first is the computer +PLC control reflow welding machine, high temperature control precision, easy to operate, with memory function, suitable for more varieties, welding process requirements of higher products, shortcomings, relatively high price;
The second is the push-button +PLC controlled reflow welding machine, the price is relatively cheap, suitable for varieties more single, or the process requirements are not high.
7. Cooling method
The main cooling methods of reflow welding equipment are: 1. Natural air cooling; 2. 3, plasma air cooling; 4, water cooling; 5. Nitrogen cooling. The commonly used cooling method of reflow welding equipment is air cooling, and the better cooling method is water cooling and nitrogen cooling, but these two kinds of relatively expensive.
2. What processing equipment is needed for a complete SMT production line?
The so-called complete SMT production line means that relatively complete equipment is equipped for SMT processing and welding of PCBA. Only with relatively complete processing equipment can an SMT plant effectively guarantee the processing quality of PCBA. In Shenzhen, there are many SMT patch factories, but it is not many to find a factory with perfect equipment. Next, kingford, Shenzhen SMT factory, will share with you what equipment is needed for the complete SMT production line? Hope to bring you some help!
1, board machine
The loading machine is a kind of auxiliary equipment in SMT production and processing. Its main function is to place the unmounted PCB board in the SMT loading machine and automatically send the board to the transmission track, and then transfer the PCB through the track to the solder paste printing machine to brush the solder paste.
2. Solder paste printing machine
Solder paste printing machine is used to print solder paste to the corresponding solder pad on the smt production process. The PCB printed by the solder paste press is convenient for the later patch machine to attach the patch components to the circuit board. Solder paste printing machine is generally composed of PCB clamping, solder paste, printing, transmission and other mechanisms.
3. SPI(3D solder paste detector)
SPI is short of Solder Paste Inspection. General people in the industry are directly called SPI (3D solder paste detector). Generally speaking, 70-80% defects in SMT patches come from solder paste printing, so it is necessary to configure an SPI to detect solder paste printing quality after solder paste printing. PCB with poor solder paste printing will be screened before the solder paste printing, so as to improve the straight-through rate after reflow welding. Now more and more 0201 small components need patch welding, so the quality of solder paste printing needs to be higher, and the defects checked after solder paste printing are much lower than the maintenance costs checked after reflow welding.
4. Patch machine
The SMT machine is also known as the "paste machine". In the production line, it is arranged after the SPI(3D solder paste detector), and it is a kind of equipment that accurately places the surface mount components on the PCB pad by moving the paste head. As the key and complex equipment in the whole SMT production line, the SMT machine is used to implement the equipment of high speed and high precision. Now, the SMT machine has developed from the early low speed to limited high speed optical alignment, and to multi-function, flexible connection modular development.
5, the first piece of detector
The first-piece detector is a new reform of the traditional first-piece detection method of PCBA. It can greatly improve the efficiency of the first piece detection, prevent errors and omissions in the detection process, realize the traceability of the detection process, save manpower and reduce the cost of the first piece detection. Use high LCR tester instead of multimeter, BOM self-check, BOM and coordinate data bidirectional comparison, fast error correction, with screen printing and direction element system automatic optical comparison detection, no manual participation.
6. Reflow welding
Reflow welding, also known as reflow welding and reflow welding, refers to the same equipment. Reflow welding has the functions of high production efficiency, less welding defects and stable performance. It is an important welding equipment in SMT plant. The main function of reflow welding is to put PCB board attached with components into the track of reflow welding machine. After temperature rise, heat preservation, welding, cooling and other links, the solder paste from paste to liquid through high temperature, and then to solid after cooling, so as to realize the role of welding between the patch components and PCB board.
7. Get off the board
The unloading machine is used at the back end of the SMT line, or the PCBA board will be automatically received into the material frame after reflow soldering, without manual board picking operation. And the role of the board machine is similar, one is automatic board, one is automatic board. With automatic lifting/automatic counting/automatic in and out of the material frame and fault alarm function. It can also set the lifting step of the material frame according to the thickness of PCBA.
8. AOI detection
AOI is actually an optical identification system, which has been widely used in today's electronic processing industry and has gradually replaced the traditional manual visual inspection method. The role of AOI is to use imaging technology to determine whether the object under test meets the standard by comparing whether there is too much difference between the object under test and the standard image. In the actual SMT plant, AOI is used to test whether the machining quality and welding quality of electronic components on the circuit board meet the processing standards, so that problems can be found in time and solved in advance. AOI includes online detection and offline detection.
9. X-Ray
With the development of electronic technology, PCBA is ubiquitous in our life. Every electronic product has PCBA, so the application of iSMT patchs more and more popular. Due to intellectualization and miniaturization, the size of the chip is getting smaller and smaller, with more and more pins. Ordinary manual detection cannot fundamentally judge the quality of solder joints. AOI detection equipment can only detect the components welded on the surface of PCBA, but cannot detect the reliability requirements of welding quality inside the pins that pass through the board. X-Ray, the official name is X-ray nondestructive testing equipment. Similar to the X-ray machines used in hospitals to take pictures, the main role of electronic manufacturing is to scan and image the inside of the product, especially components such as pin BGA QFN, to detect whether there are abnormal solder joints, such as weak welding, short circuit, etc.
The above content is shared by kingford (the processing equipment needed for a complete SMT production line). Of course, here we are talking about the processing equipment used online. Apart from the equipment used online, there are many related equipment used in SMT processing. Including (solder paste mixer, dispenser, oven, docking station, programming system, monitoring system), etc.; For more information about SMT, please visit Shenzhen kingford Co., LTD